5 Best Predictive Maintenance Techniques
September 8, 2023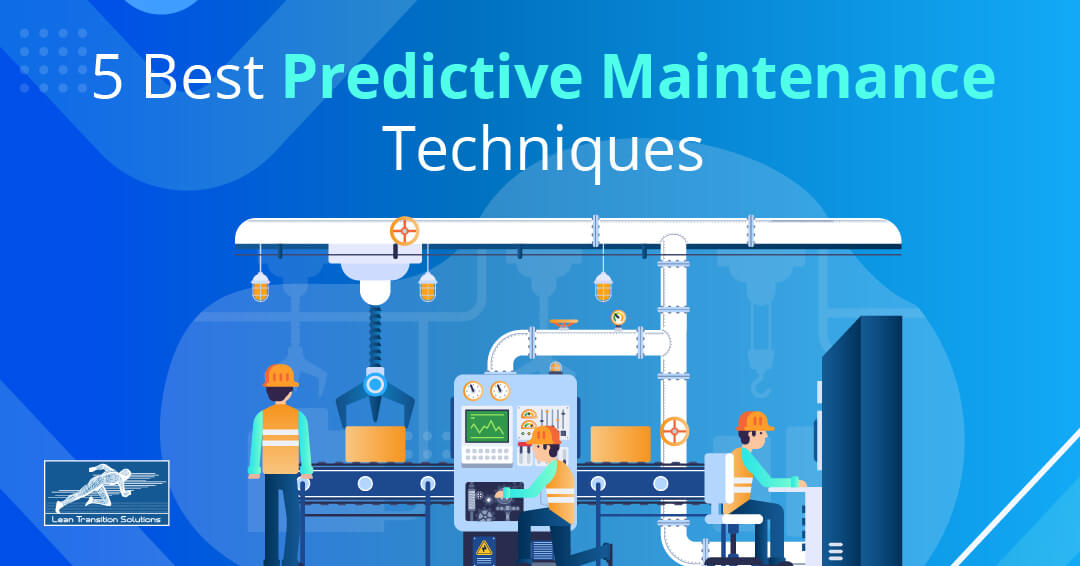
Maintenance is crucial for industrial equipment to ensure smooth operation, increased reliability, and extended lifespan. Traditionally, organisations have relied on two primary maintenance strategies: reactive maintenance and preventive maintenance. While these approaches have their merits, they also have significant drawbacks that can lead to operational disruptions, increased costs, and even safety hazards.
In recent years, a transformative shift has occurred in the maintenance world, driven by technological advancements and data analytics. Predictive maintenance (PdM) is a proactive strategy that outshines traditional reactive and preventive maintenance methods, as it anticipates issues before they arise, saving maintenance costs and ensuring uninterrupted operations. Let's understand how organisations can greatly benefit from predictive maintenance strategies over other maintenance methods.
What is Predictive Maintenance (PdM)?
Predictive Maintenance (PdM) is an advanced maintenance strategy organisations use to monitor and predict the condition of their equipment and machinery in real-time or near-real-time. Instead of performing maintenance tasks on a fixed schedule (preventive maintenance) or waiting for equipment to break down (reactive maintenance), PdM relies on real-time data and predictive analytics to identify potential issues before they lead to unplanned downtime, costly repairs or safety hazards. PdM utilises data collection, analysis, and various technologies to make informed decisions about when and how to perform maintenance tasks, ultimately optimising equipment reliability and operational efficiency.
5 Best Predictive Maintenance Techniques you should know
1. Vibration Analysis
Vibration analysis is a predictive maintenance technique that monitors the vibrations of rotating equipment such as motors, pumps, and turbines. By analysing these vibrations' frequency, amplitude, and patterns, maintenance teams can detect irregularities that indicate potential issues like misalignment, imbalance, or wear in machine components. Vibration analysis is highly effective in detecting equipment issues at an early stage, allowing for timely maintenance and preventing costly equipment failures. It is vital in enhancing equipment reliability and reducing downtime while leveraging data analytics and sensor technology for continuous monitoring and predictive insights.
2. Infrared Thermography
Infrared thermography is a non-contact technique that uses thermal imaging to detect anomalies in equipment temperature, making it a valuable tool for predictive maintenance. It can identify overheating components or electrical connections, which may indicate issues such as loose connections, bearing wear, or insulation problems. Infrared thermography visually represents temperature variations, enabling maintenance teams to pinpoint potential issues quickly. This technique is highly effective for electrical systems and is essential for preventing electrical fires, minimising energy wastage, and ensuring the safety and longevity of equipment.
3. Oil Analysis
Oil analysis monitors lubricating oil in machinery to predict maintenance needs. Organisations can detect issues such as excessive wear, contamination, or chemical degradation in equipment components like engines, gearboxes, and hydraulic systems by analysing the oil's composition, viscosity, and contaminants. Oil analysis offers insights into the health of critical components and helps organisations make informed decisions regarding oil changes and equipment maintenance schedules. It extends the lifespan of machinery, reduces maintenance costs, and minimises unplanned downtime.
4. Ultrasound Testing
Ultrasound testing is a versatile Predictive Maintenance technique used to detect issues in various equipment, including air compressors, steam traps, and valves. It relies on high-frequency sound waves beyond the range of human hearing to identify abnormalities like leaks, friction, and bearing defects. Ultrasound testing provides early warning signs of potential problems, allowing maintenance teams to address issues before they escalate. It is highly sensitive, cost-effective, and crucial in optimising equipment reliability and reducing energy consumption through leak detection.
5. Machine Learning and AI
Machine Learning (ML) and Artificial Intelligence (AI) are cutting-edge technologies revolutionising Predictive Maintenance. ML algorithms analyse vast historical and real-time data to create predictive models for monitoring equipment health. These models can forecast when maintenance is needed, detect anomalies, and provide actionable insights for maintenance teams. By integrating ML and AI into Predictive Maintenance systems, organisations can enhance the accuracy of predictions, adapt to changing conditions, and optimise maintenance strategies. These technologies are at the forefront of Industry 4.0, allowing for data-driven decision-making and continuous improvement in maintenance practices.
Enhancing Predictive Maintenance with CMMS
In today's industrial landscape, the integration of advanced sensors such as Infrared Analysis Sensors, Motor Circuit Analysers, Vibration Analysis Sensors, and Ultrasonic Analysis Microphones into Computerised Maintenance Management Systems (CMMS) has ushered in a new era of proactive maintenance. CMMS is the central hub where all this diverse data is collected, organised, and analysed, identifying anomalies, patterns, and trends that indicate equipment failures or maintenance needs.
Processing and interpreting data from various sources can provide valuable analytical insights into operational procedures. Organisations can utilise sensors like Infrared Analysis for capturing temperature changes, Motor Circuit analysers for monitoring electrical circuits, Vibration Analysis sensors for detecting mechanical vibrations, and Ultrasonic Analysis microphones for detecting acoustic abnormalities.
CMMS helps transform raw sensor data into valuable information for predictive analytics, empowering organisations to schedule maintenance activities precisely when needed, minimising downtime, reducing maintenance costs, and extending asset lifespan. This integration enhances the Overall Operational Efficiency (OOE) and marks a pivotal shift towards predictive maintenance strategies that optimise asset performance and reliability.
Steps to implement Predictive Maintenance strategy in your organisation
1. Assessment and Planning
- Identify Critical Equipment: Determine which equipment and assets are critical to operations and should be prioritised for PdM implementation.
- Establish Objectives: Define clear goals and objectives for implementing PdM, such as reducing downtime, cutting maintenance costs, or enhancing safety.
- Resource Allocation: Allocate the necessary budget, personnel, and technology resources for PdM implementation.
2. Data Collection and Acquisition
- Select Sensors and Tools: Choose appropriate sensors and data acquisition tools based on the type of equipment and parameters to be monitored.
- Install Sensors: Properly install sensors on selected equipment to collect real-time data. Ensure sensors are calibrated and configured correctly.
3. Data Integration and Storage
- Data Management System: Implement a robust data management system to collect, store, and organise the data generated by sensors and equipment.
- Data Security: Ensure data security and compliance with relevant regulations, especially if sensitive information is involved.
4. Condition Monitoring
- Real-Time Monitoring: Continuously monitor the condition of critical equipment using the installed sensors and data collection tools.
- Data Analysis: Employ data analytics techniques to analyse the collected data for patterns, anomalies, and early warning signs of equipment degradation.
5. Alert Generation
- Set Maintenance Triggers: Establish alert thresholds based on the predictive models to trigger notifications when equipment conditions deviate from normal.
- Prioritising Critical Issues: Develop a system for prioritising alerts based on the severity of potential issues.
6. Maintenance Planning and Scheduling
- Maintenance Recommendations: When an alert is triggered, the system should generate maintenance recommendations, including the type of maintenance required (e.g., lubrication, calibration, part replacement).
- Scheduling: Scheduled maintenance activities based on the recommendations, considering equipment availability and production schedules.
7. Documentation and Reporting
- Maintaining Historical Records: Maintain detailed records of all maintenance activities, including repairs, replacements, and the effectiveness of PdM interventions.
- Reporting: Generate reports and dashboards to track the performance and impact of PdM on equipment reliability and operational efficiency.
8. Training and Skill Development
- Training Programs: Train maintenance teams and operators on using PdM tools, data interpretation, and best practices for equipment maintenance.
- Continuous Learning: Encourage continuous learning and skill development to stay up-to-date with evolving PdM technologies and techniques.
9. Integration with Existing Systems
- Integrate with CMMS: Integrate PdM systems with Computerised Maintenance Management Systems (CMMS) to streamline maintenance workflows and data management.
- IoT Integration: If applicable, ensure seamless integration with IoT platforms and Industry 4.0 technologies.
10. Monitoring and Evaluation
- Key Performance Indicators (KPIs): Define and track maintenance KPIs such as Mean Time Between failures (MTBF), Mean Time To Repair (MTTR), equipment uptime, and maintenance costs to measure the success of PdM implementation.
- Regular Audits: Conduct regular audits and assessments to evaluate the effectiveness of PdM strategies and make necessary adjustments.
Benefits of Implementing Predictive Maintenance software in an organisation
- Minimise Downtime: PM allows organisations to detect and address equipment issues before they result in unplanned downtime. This proactive approach ensures that machinery remains operational, reducing production interruptions and associated revenue losses.
- Reduces Maintenance Cost: By identifying and addressing maintenance needs precisely when required, predictive maintenance (PdM) prevents unnecessary maintenance activities, reduces labour costs, lowers spare parts consumption, and minimises emergency repairs, ultimately leading to significant cost savings.
- Extended Asset Lifespan: Predictive Maintenance optimises equipment maintenance and extends asset lifespan, reducing costly replacements or upgrades.
- Improved Safety: Predictive Maintenance detects safety hazards early, allowing organisations to prevent accidents and legal liabilities while protecting employees.
- Enhanced Equipment Reliability: Regular monitoring and analysis of equipment performance enable organisations to maintain higher levels of reliability. This reliability, in turn, leads to consistent product quality and customer satisfaction.
- Data-Driven Decision-Making: Predictive maintenance (PdM) relies on data analysis to give organisations valuable insights into equipment health and performance. This data enables informed decision-making regarding maintenance schedules, resource allocation, and capital investments.
- Adaptability to Industry 4.0: In the era of Industry 4.0 and the Internet of Things (IoT), PdM aligns with the latest technological advancements. Organisations can further integrate sensors and data analytics to enhance their maintenance strategies, staying relevant and competitive in an evolving landscape.
5 Predictive Maintenance Program Implementation Pitfalls
1. Incomplete Data Collection
Insufficient or inconsistent data can hinder accurate predictions. Ensure comprehensive data collection from sensors and equipment and implement data quality checks.
2. Lack of Clear Objectives
Without well-defined goals, PdM efforts may lack direction. Establish specific maintenance objectives and KPIs to guide the predictive maintenance program effectively.
3. Neglecting Continuous Improvement
Failing to adapt to changing conditions can lead to outdated models. Continuously refining predictive models and updating strategies based on evolving data can help to overcome these maintenance challenges.
4. Inadequate Management Support
Insufficient resources and lack of top-level support affect the effectiveness of the predictive maintenance program. To maintain support, secure management backing, allocate necessary resources, and demonstrate ROI (Return on investment).
5. Resistance to Change
Resistance to PdM adoption by employees can impede success. Implement change management strategies to communicate the benefits of implementing maintenance software within the organisation, address concerns, and secure buy-in from all stakeholders.
Best Practices and Tips for Predictive Maintenance(PM) Strategies
- Establish a clear Predictive Maintenance Strategy
- Select appropriate PM techniques.
- Form a cross-functional team.
- Analyse maintenance data regularly.
- Continuously improve and adapt PM processes as necessary.
As we wrap up our exploration of the five best predictive maintenance techniques, it's essential to emphasise the tremendous value that PdM can bring to organisations of all sizes and industries. With uncertainties and high costs, the traditional approach of reactive or preventive maintenance is gradually being replaced by a more proactive and data-driven method. Predictive Maintenance empowers organisations to predict, prevent, and proactively address equipment issues, leading to reduced downtime, enhanced safety, and significant cost savings.
Today's business environment is fast-paced and competitive, making it imperative for organisations to adopt predictive maintenance programs. By embracing this transformative strategy, you can stay ahead of the curve and secure a future where maintenance is necessary and a strategic advantage that boosts your organisation's efficiency and reliability to new heights.