What is Reliability-Centred Maintenance (RCM) ?
Reliability-Centred Maintenance (RCM) is a systematic maintenance approach that ensures the reliability, safety, and optimal performance of equipment and systems while minimising maintenance costs.
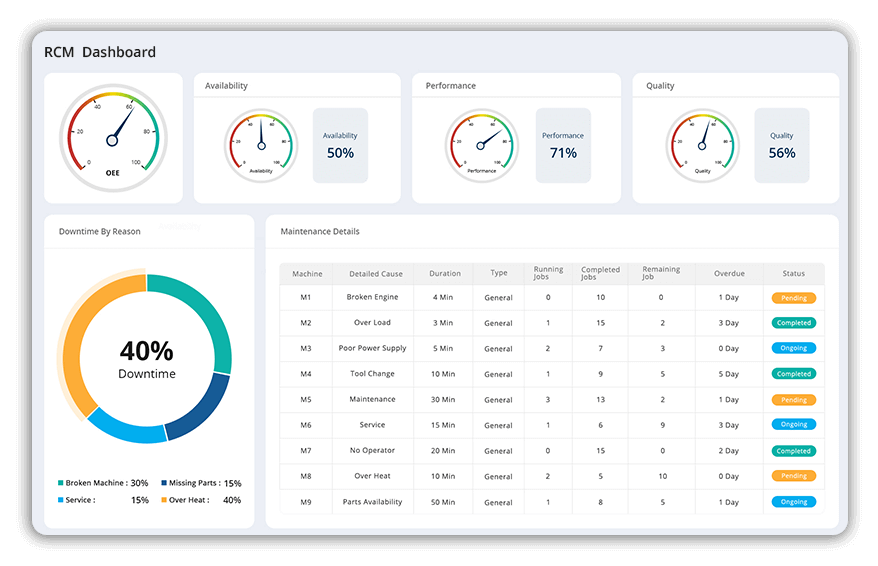
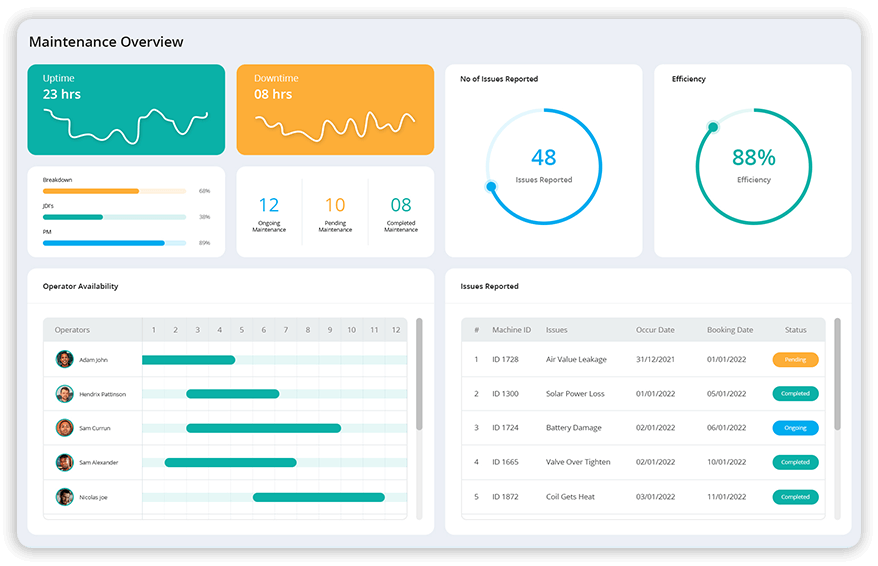
Why is Reliability important in Maintenance?
Ensuring reliability in maintenance is crucial for consistent performance and asset longevity. Reliable equipment ensures operational efficiency, minimises downtime and reduces the risk of unexpected failures. By employing proactive maintenance strategies, organisations can enhance the dependability of their systems, leading to increased safety, cost optimisation, and improved overall performance. Industrial assets need to undergo regular maintenance to ensure reliability, sustainability, and operational continuity, which, in turn, helps meet production targets and mitigate potential risks.
Types of Reliability-Centred Maintenance Techniques
- Functions-Based Approach: The functions-based approach in RCM centres on critical system functions. It identifies potential failure modes affecting various functions and develops targeted maintenance strategies.
- Components-Based Approach: The components-based RCM approach focuses on individual system components. It identifies potential failure modes, assesses consequences, and determines targeted maintenance actions.
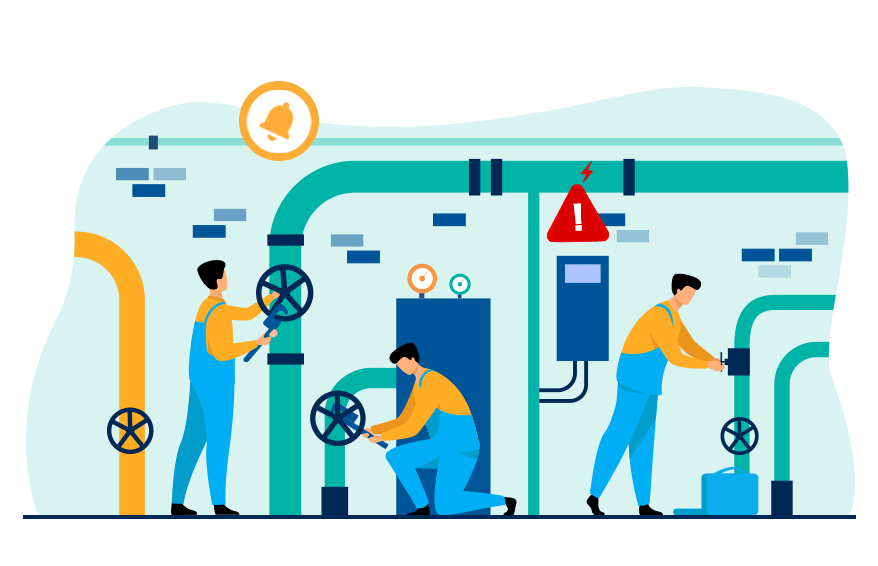
Contents
- Benefits of implementing Reliability-Centred Maintenance in your organisation
- Key Principles of RCM
- What is the concept of Reliability in Maintenance?
- 7 Steps to Implement Reliability-Centred Maintenance
- How can you Measure Reliability?
- 7 Questions to ask on your next Reliability-Centred Maintenance program
- History of Reliability-Centred Maintenance
- Can Reliability-Centred Maintenance be integrated into existing maintenance programs?
- What role does Risk Assessment play in Reliability-Centred Maintenance?
- Reliability-Centred Maintenance (RCM) vs Failure Modes and Effects Analysis (FMEA)
- In which industries is Reliability-Centred Maintenance commonly applied?
- Example of Reliability-Centred Maintenance
- Differences between Risk-Based Maintenance (RBM) and Reliability-Centred Maintenance (RCM)
- What software tools are recommended for Reliability-Centred Maintenance analysis and documentation?
- How can Reliability-Centred Maintenance optimise Maintenance costs and increase ROI?
- What training is required for personnel involved in Reliability-Centred Maintenance Implementation?
- How frequently should Reliability-Centred Maintenance analysis be conducted for optimal results?
- What are the potential pitfalls to avoid while Implementing Reliability-Centred Maintenance?
Benefits of implementing Reliability-Centred Maintenance in your organisation
- Enhanced Reliability: Reliability-Centred Maintenance improves system reliability by systematically identifying and addressing potential failure modes.
- Cost Optimisation: By prioritising maintenance tasks based on their impact and cost-effectiveness, Reliability-Centred Maintenance helps optimise maintenance expenditures.
- Extended Asset Life: Proactive and targeted maintenance strategies under Reliability-Centred Maintenance contribute to extending the lifespan of critical assets.
- Safety Improvement: Through thoroughly analysing failure modes and consequences, Reliability-Centred Maintenance enhances safety by mitigating potential risks.
- Operational Efficiency: Reliability-Centred Maintenance streamlines maintenance efforts, ensuring resources are allocated efficiently to areas with the highest impact on asset performance.
- Downtime Reduction: By addressing failure modes before they lead to critical issues, Reliability-Centred Maintenance minimises unplanned downtime and production interruptions.
Key Principles of RCM
- Maintains the functionality of the system.
- Recognises potential failure modes that may impact the system's functionality.
- Establishes a hierarchy to prioritise these failure modes.
- Implements relevant and efficient tasks to manage and control the identified failure modes.
Reliability-Centred Maintenance aims to enhance equipment reliability, reduce maintenance costs, improve safety, and avoid any maintenance tasks that are not effective for specific machinery or equipment. Components of Reliability-Centred Maintenance include preventive maintenance, reactive maintenance, proactive maintenance and predictive testing and inspection. The three phases of a Reliability-Centred Maintenance program are initiation, analysis, and implementation. Each phase is crucial for identifying optimal maintenance strategies, ensuring the efficient use of resources, and fostering a proactive maintenance culture within an organisation.
What is the concept of Reliability in Maintenance?
In maintenance, reliability refers to the ability of a system or asset to perform its intended functions consistently without unexpected failures. It measures the dependability and consistency in achieving desired performance levels over time. Reliability in maintenance is crucial for minimising downtime, optimising operational efficiency, and ensuring the longevity of assets. Organisations take proactive measures to identify, assess, and mitigate possible failure modes to ensure optimal functionality and avoid unplanned disruptions. The concept of reliability plays a fundamental role in guiding maintenance practices towards achieving these goals. Organisations can enhance their systems' overall dependability and performance by implementing targeted maintenance strategies, increasing efficiency and reducing downtime.
7 Steps to Implement Reliability-Centred Maintenance
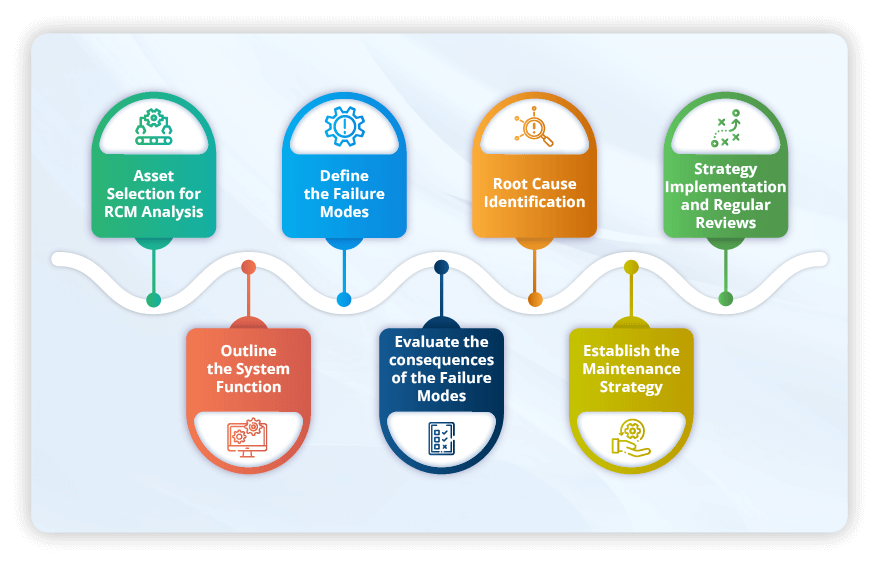
- Asset Selection for RCM Analysis: Choose a specific asset for Reliability-Centred Maintenance (RCM) analysis. This could be a critical piece of equipment or a system whose reliability is important to your operations.
- Outline the System Function: Trace the functions of the chosen system or asset. This involves a detailed understanding of its intended purposes and operational requirements to provide a foundation for subsequent analysis.
- Define the Failure Modes: Identify potential failure modes by considering ways the system may deviate from its intended functions. This step involves a comprehensive examination of possible failure scenarios.
- Evaluate the consequences of the Failure Modes: Evaluate the consequences associated with each identified failure mode. This includes an analysis of the impact on safety, operational efficiency, and overall system performance.
- Root Cause Identification: Determine the root causes contributing to each failure mode. Understanding the underlying reasons for potential failures is crucial for developing effective maintenance strategies.
- Establish the Maintenance Strategy: Establish a maintenance strategy for each identified failure mode. This involves selecting the most appropriate and cost-effective approach to mitigate or prevent failures, ranging from reactive to proactive measures.
- Strategy Implementation and Regular Reviews: Implement the selected maintenance strategies and conduct regular reviews to ensure their ongoing effectiveness. This step involves a continuous improvement cycle, where adjustments can be made based on evolving system conditions and performance feedback.
How can you Measure Reliability?
Measuring reliability in maintenance involves assessing various Maintenance KPIs (Key Performance Indicators). Here are the most commonly used maintenance metrics for measuring reliability:
- Mean Time to Repair (MTTR): MTTR is the average time taken to repair equipment after a failure, and a lower MTTR indicates a more efficient maintenance response.
- Mean Time Between Failure (MTBF): MTBF calculates the average time elapsed between consecutive failures. A higher MTBF signifies greater reliability, indicating longer periods of uninterrupted operation.
- Uptime: Uptime is the proportion of time a system or equipment is operational. It is the complement of downtime and is expressed as a percentage. Higher uptime values indicate better reliability.
- Planned Maintenance Percentage (PMP): PMP represents the percentage of maintenance activities that are planned or scheduled in advance. A higher PMP suggests a proactive approach to maintenance, reducing unplanned downtime.
- Overall Equipment Effectiveness (OEE): OEE provides a holistic assessment of equipment performance by considering availability, performance efficiency, and quality factors. A high OEE indicates optimal equipment reliability and effectiveness.
- Preventive Maintenance Compliance (PMC): PMC measures how scheduled preventive maintenance tasks are completed as planned. It reflects the organisation's adherence to proactive maintenance strategies.
7 Questions to ask on your next Reliability-Centred Maintenance program
The following questions are to be asked to evaluate any asset or system with the RCM (Reliability Centred Maintenance) process:
- What functions and performance standards are expected from each asset?
- How can each asset fail to perform its intended functions?
- How can each functional failure occur?
- What is the root cause of each failure mode?
- What are the consequences of each failure?
- What should be done to predict or prevent each failure?
- What actions should be taken if a suitable proactive task cannot be determined?
History of Reliability-Centred Maintenance
Reliability-Centred Maintenance (RCM) originated from a study on aircraft maintenance and reliability requirements conducted by engineers Tom Matteson, Howard Heap, and Stanley Nowlan for United Airlines. Recognising the significance of their work, the U.S. Department of Defense later sponsored their project, amplifying its reach and impact. This historical initiative marked the inception of Reliability-Centred Maintenance as a systematic approach to maintenance, emphasising the need for a structured methodology in identifying and addressing potential failures in complex systems.
Can Reliability-Centred Maintenance be integrated into existing maintenance programs?
Reliability-Centred Maintenance (RCM) can be seamlessly integrated into existing maintenance programs. RCM offers a flexible framework that can complement and enhance established maintenance practices. By incorporating RCM principles, organisations can systematically identify and prioritise maintenance tasks, ensuring a proactive and targeted approach to asset reliability. This integration allows for the optimisation of existing maintenance efforts, minimising costs while maximising the effectiveness of maintenance strategies. RCM's adaptability makes it a valuable addition to any organisation seeking to improve the reliability, safety, and efficiency of its maintenance programs without a complete change in existing maintenance systems.
What role does Risk Assessment play in Reliability-Centred Maintenance?
RCM employs risk assessment to systematically identify and prioritise maintenance tasks based on their impact on asset reliability and safety. This process involves analysing the criticality of failure modes and considering factors such as safety, environmental impact, and operational consequences. By incorporating risk assessment, RCM ensures that maintenance efforts are directed towards addressing the most significant risks, thereby optimising resource allocation and enhancing the overall effectiveness of the maintenance strategy.
Reliability-Centred Maintenance (RCM) vs Failure Modes and Effects Analysis (FMEA)
Reliability-Centred Maintenance (RCM) and Failure Modes and Effects Analysis (FMEA) are both methodologies aimed at enhancing system reliability but differ in their approaches. Reliability-Centred Maintenance helps identify, prioritise, and mitigate potential failure modes and ensures equipment reliability through proactive maintenance. On the other hand, FMEA primarily involves systematically evaluating failure modes, their causes, and consequences without emphasising specific maintenance strategies. While RCM is holistic, considering the entire system, FMEA is often more focused on individual components. RCM tends to be more comprehensive in its application, incorporating broader considerations for optimising maintenance efforts. At the same time, FMEA provides a detailed analysis of failure modes and their potential effects. Organisations often choose between RCM and FMEA based on their specific needs and objectives, with RCM offering a more comprehensive framework for maintenance decision-making.
In which industries is Reliability-Centred Maintenance commonly applied?
Reliability-Centred Maintenance (RCM) finds widespread application across various industries due to its versatility and effectiveness in optimising maintenance strategies. Common industries utilising RCM as a maintenance strategy include manufacturing, automotive, plant hire, electrical, oil and gas, energy production, construction, pharmaceuticals, healthcare, marine vessels, aviation, and transportation. The adaptability of RCM makes it applicable to diverse sectors where equipment reliability, safety, and operational efficiency are paramount concerns. The structured approach of RCM proves valuable in mitigating risks, minimising downtime, and extending the life of critical assets in these diverse industrial settings.
Example of Reliability-Centred Maintenance
In the automotive industry, consider the application of Reliability-Centred Maintenance (RCM) for a specific asset, such as an automated paint booth used in the painting process. The organisation was struggling with frequent breakdowns and unexpected downtime, which has led to production delays and increased maintenance costs.
- Identifying Critical Functions: In this case, critical functions may include consistent paint application and curing for a paint booth.
- Defining Potential Failure Modes: RCM analysis proceeds to identify potential failure modes that could impact the critical functions. For instance, this could involve considering issues like malfunctioning spray nozzles or inadequate temperature control during curing in a paint booth.
- Assessing Consequences of Failure Modes: For a paint booth, a malfunctioning spray nozzle could lead to uneven paint application, affecting the quality of the finish. At the same time, a failure in temperature control during curing might result in paint defects and increased rework.
- Root Cause Analysis: After identifying failure modes and their consequences, a thorough root cause analysis is conducted to understand the underlying reasons behind these failures. This could involve investigating issues such as nozzle calibration problems or malfunctions in temperature sensors.
- Establishing Maintenance Strategies: Based on the Root Cause Analysis, specific maintenance strategies are developed to address and mitigate the identified failure modes. This might involve implementing regular calibration checks for spray nozzles and timely replacement of temperature sensors.
- Implementing and Reviewing Strategies: The developed maintenance strategies are implemented, and their effectiveness is regularly reviewed. This iterative process ensures that the chosen strategies remain relevant and effective in maintaining the reliability of the automated paint booth over time.
This proactive approach helps prevent unexpected breakdowns, ensures consistent product quality, and optimises maintenance efforts in the automotive painting process.
Differences between Risk-Based Maintenance (RBM) and Reliability-Centred Maintenance (RCM)
Risk-Based Maintenance (RBM) and Reliability-Centred Maintenance (RCM) are maintenance strategies with distinct focuses. Risk-Based Maintenance prioritises maintenance tasks based on risk assessments, considering the probability and consequences of equipment failures. It emphasises a holistic risk management approach, incorporating safety, environmental impact, and operational disruptions. In contrast, Reliability-Centred Maintenance prioritises system functions by systematically identifying and mitigating potential failure modes through proactive maintenance. Reliability-Centred Maintenance analyses failure consequences and selects maintenance strategies based on functional criticality. While Risk-Based Maintenance assesses risks comprehensively, Reliability-Centred Maintenance is more function-specific, prioritising critical functions over overall risk. Both strategies optimise maintenance efforts, but Risk-Based Maintenance is broader in scope, encompassing various risks, while Reliability-Centred Maintenance is more function-centric, concentrating on ensuring key system functions.
What software tools are recommended for Reliability-Centred Maintenance analysis and documentation?
- CMMS (Computerised Maintenance Management System): CMMS software is essential for organising and managing maintenance activities related to Reliability-Centred Maintenance (RCM). It is a comprehensive maintenance solution that helps track asset information, schedule maintenance tasks, and record maintenance history, facilitating an efficient RCM process.
- RCM Software Solutions: Dedicated RCM software provides specialised tools for conducting RCM analyses, documenting findings, and managing maintenance strategies.
- FMEA Software: FMEA software can be employed for Failure Modes and Effects Analysis (FMEA), a crucial component of RCM.
- Asset Management Software: These solutions help in managing the entire lifecycle of assets, including RCM analysis, documentation, and performance tracking.
- Root Cause Analysis (RCA) Tools: Root Cause Analysis tools help to identify root causes during RCM analysis, ensuring a thorough understanding of failure modes.
- Documentation and Collaboration Tools: These tools support collaborative documentation of RCM findings, making information easily accessible to relevant stakeholders.
How can Reliability-Centred Maintenance optimise Maintenance costs and increase ROI?
Reliability-Centred Maintenance (RCM) can significantly optimise maintenance costs and enhance Return on Investment (ROI) by focusing on critical assets and prioritising maintenance activities based on their impact on overall system reliability. Through a systematic analysis, RCM helps identify each asset's most cost-effective maintenance strategies, ensuring that resources are allocated where they are most needed. By proactively addressing potential failures and adopting a condition-based maintenance approach, Reliability-Centred Maintenance minimises downtime, reduces unnecessary maintenance tasks, and extends the lifespan of equipment. This precision in maintenance planning and execution directly translates into lower operational costs and increased ROI as assets operate at peak efficiency, requiring fewer resources for upkeep and repair.
What training is required for personnel involved in Reliability-Centred Maintenance Implementation?
Personnel involved in Reliability-Centred Maintenance (RCM) implementation require comprehensive training in RCM methodologies, analysis techniques, and relevant software tools. Training should cover understanding asset criticality, identifying failure modes, and developing effective maintenance strategies. Additionally, personnel need proficiency in data collection and analysis and the ability to conduct collaborative decision-making processes. Familiarity with risk assessment, root cause analysis, and preventive and predictive maintenance principles is essential. Ongoing training ensures that personnel stay up-to-date with evolving technologies and industry best practices, enabling them to effectively contribute to RCM's success in optimising maintenance processes and asset reliability.
How frequently should Reliability-Centred Maintenance analysis be conducted for optimal results?
For optimal results, Reliability-Centred Maintenance (RCM) analysis should be conducted periodically, typically at intervals aligned with the lifecycle stages of critical assets or systems. RCM is not a one-time activity but a continuous process that adapts to equipment, operations, or external changes. Conducting RCM analysis at key milestones, such as during asset acquisition, modifications, or significant changes in operating conditions, ensures that maintenance strategies remain effective and aligned with evolving requirements. This periodicity allows organisations to proactively address emerging risks, optimise maintenance efforts, and sustain the reliability and performance of critical assets over their lifecycle.
What are the potential pitfalls to avoid while Implementing Reliability-Centred Maintenance?
- Insufficient Data Collection: Prioritise thorough data gathering through equipment history, maintenance records, and expert input to comprehensively understand asset performance and potential risks.
- Overemphasis on Cost Reduction: Strike a balance between cost considerations and the overarching goal of ensuring asset reliability, prioritising maintenance strategies that align with both objectives.
- Failure to Adapt to Changing Conditions: Establish a continuous improvement process, regularly reviewing and updating RCM analyses to reflect changes in equipment, processes, and business objectives.
- Inadequate Training and Awareness: Invest in comprehensive training programs to ensure all stakeholders are well-versed in RCM principles, methodologies, and tools.