What is Predictive Maintenance Software?
Predictive maintenance software monitors equipment conditions and their performance over a period of time to detect any severe issues and schedule maintenance accordingly. Using TITAN CMMS - the predictive maintenance system software, businesses can identify signs of equipment malfunction in advance and take a proactive approach to maintenance. Even the slightest variation in temperature, vibration or sound will be immediately identified and evaluated to avoid machine breakdowns.
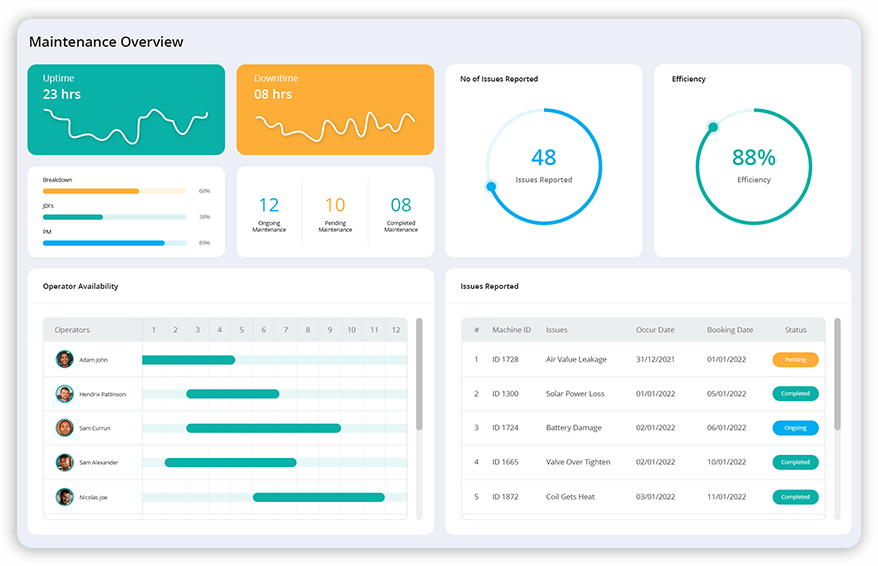
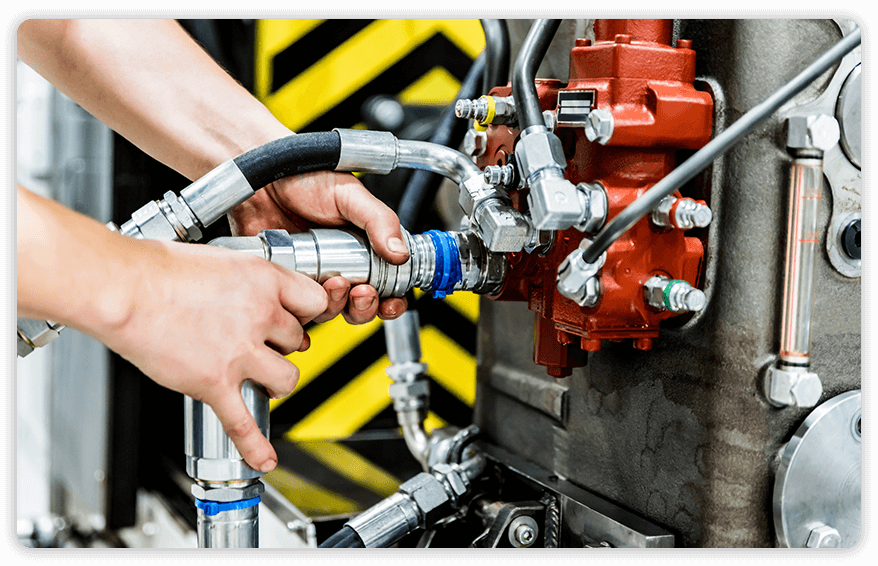
How Does Predictive Maintenance Work?
Predictive maintenance, often abbreviated as ‘PM’ or ‘PdM’, is a maintenance activity that monitors equipment performance in day-to-day operations to identify and prevent any failures that might occur. TITAN CMMS helps organisations take measures to avoid equipment downtime by monitoring real-time equipment data. Along with a predictive maintenance strategy, a powerful CMMS is much needed in asset-intensive organisations to boost productivity and increase the lifespan of their assets.
Automate Maintenance Scheduling & Tracking Process
Do not worry about maintenance schedules; automate the entire maintenance scheduling and tracking process using the right preventive maintenance system in place. TITAN CMMS allows organisations to analyse the real-time data fed into the CMMS system and automatically create and run the PM program and other maintenance activities planned. By automating the entire process of maintenance scheduling and tracking, organisations can see a visible drop in machine downtime.
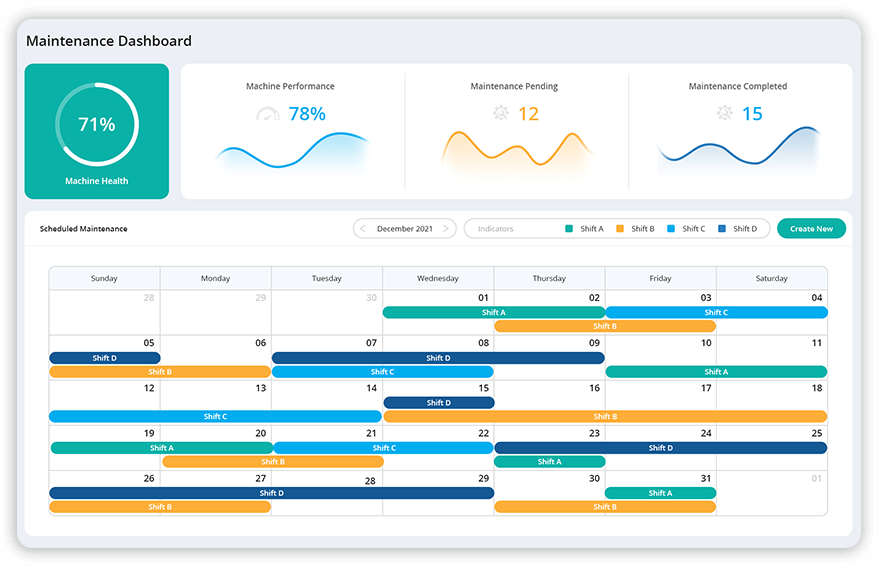
Impact of Predictive Maintenance in the Facility
CMMS combined with predictive maintenance strategies will significantly impact the facility. CMMS will help optimise the overall maintenance operations in various ways such as:
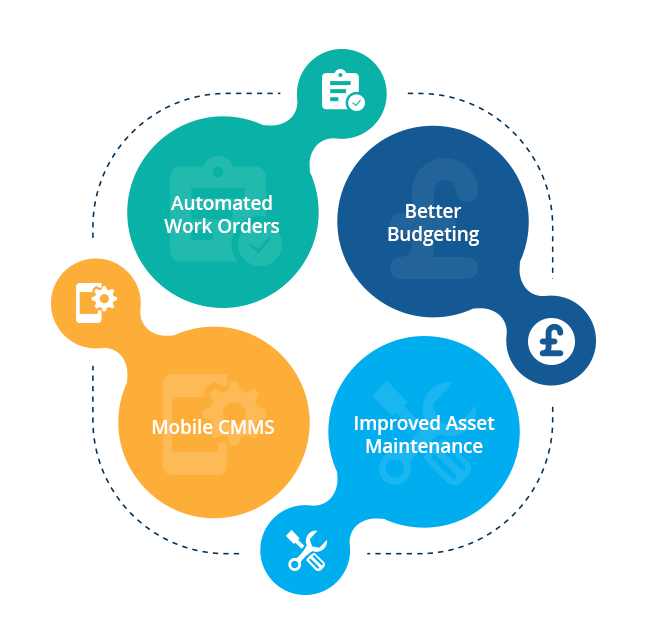
Automated Work Orders
TITAN CMMS is available 24/7 and automatically creates work orders and sends alerts to the facility managers upon a new service request or other emergencies.
Better Budgeting
Knowing when equipment might fail will help teams plan maintenance activity in advance retaining its life span and lowering expenses due to unplanned maintenance.
Improved Asset Maintenance
TITAN CMMS gives real-time updates on machine/asset health and helps teams make data-driven decisions to maximise uptime and machine life cycle losses and reduce costs.
Mobile CMMS
Track and manage PdM at one’s convenience using mobile maintenance app. The maintenance team can log work order information and status and upload images straight from their devices.
TITAN CMMS - The Key to Optimise Maintenance Operations Smart Solution
Worried about managing maintenance operations? TITAN CMMS is here to help! TITAN help organisations track and manage all maintenance-related tasks, boosts asset efficiency and performance, by creating a maintenance request, breakdown request, just do it (JDI), and tasks, at any time from anywhere.
Start Free Trial Watch Video Tell a FriendCMMS App for
Predictive Maintenance
Get alerts instantly regarding the Predictive Maintenance Schedule through TITAN CMMS App. Deploy any other maintenance activities along with the scheduled PM in just one click! Once the maintenance activities are carried out, users will get auto-generated reports to make data-driven decisions. Track, monitor, and analyse work orders, PM schedules, their status, and progress from wherever you are!
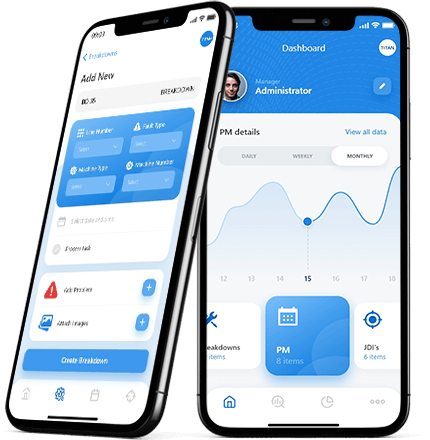
Boost the efficiency of your organisation with Predictive Maintenance
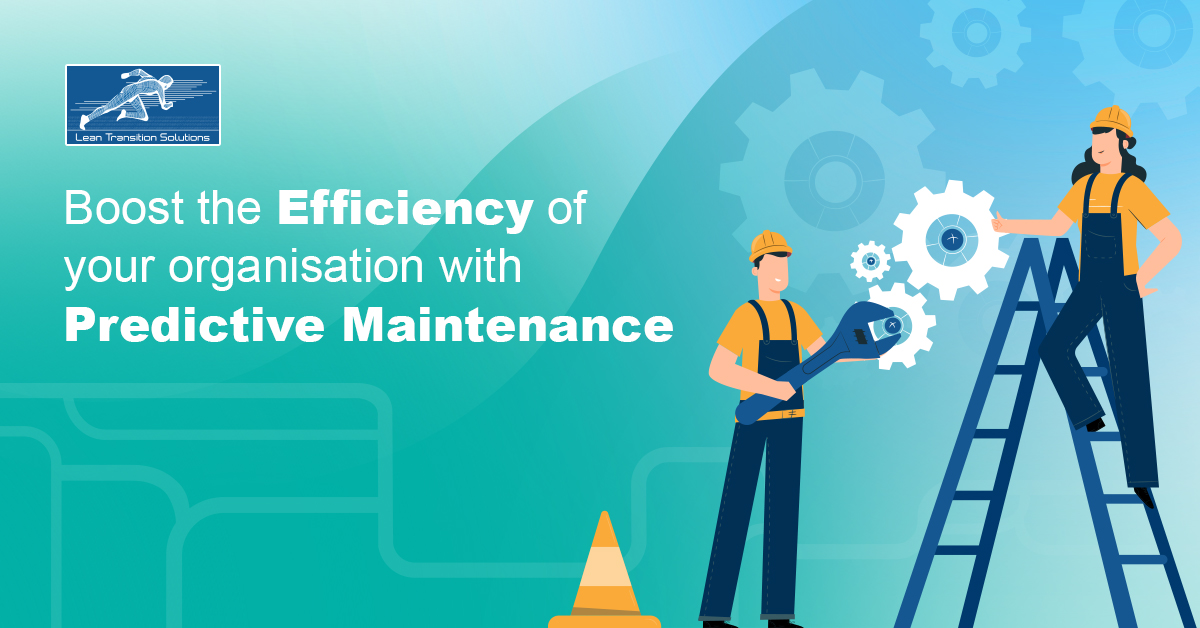
Contents
- How does Predictive Maintenance work?
- Why should you invest in Predictive Maintenance?
- Where is Predictive Maintenance used?
- How can CMMS support your Predictive Maintenance?
- How to establish a predictive maintenance program?
- What are the benefits of predictive maintenance?
- What are the six pillars of the predictive maintenance program?
How does Predictive Maintenance work?
Anticipating a problem even before it occurs is challenging. Both past and real- time data from various parts of the operations can help solve this. Maintenance plans are always scheduled based on the present condition of the asset. Predictive maintenance tracks the asset condition and forewarns impending equipment failures. The main elements that allow the PdM to do this are:
- Installed condition monitoring sensors capable of monitoring the real- time performance of the assets.
- The IoT technology performing the collection and evaluation of the work order data by which the communication between the machines, software solutions and cloud technology is enabled.
- Predictive data models possessing the process data that can foresee the breakdowns and failures Before installing sensors, it is good observe the conditional asset baseline and organise your data. By collecting the conditional data, you get to control the abnormalities. The sensor activates the predictive maintenance protocol when the equipment functions outside the normal parameters. After this, a CMMS system generates a work order assigned to the technicians who perform the repairs needed.
Why should you invest in Predictive Maintenance?
Asking yourself as to why you should invest in a predictive maintenance strategy. Predictive maintenance can let you bypass these costly issues.
- Reactive maintenance after a machine breakdown
- Equipment downtime that affects your production returns.
- Overdoing preventive maintenance causing wastage of time and productivity.
A proper diagnosis of the breakdown or the failures within an asset’s infrastructure without shutting down the system or compromising the other parts is another reason you should look at predictive maintenance. With the right resources, you can finish the corrective maintenance actions even before the work orders appear.
Where is Predictive Maintenance used?
Depending upon the requirements, Predictive maintenance has varied scopes in almost every industry.
- Manufacturing: One of the most significant users of predictive maintenance is the manufacturing industry. Since it cannot afford to slow down or stop production lines, predictive maintenance has everyday applications in the manufacturing sector. It ranges from using vibration sensors to identify the patterns of the fragile spindles in the milling machines to measuring the temperature of the differential upstream and downstream of the heat exchanger to identify the first signs of clogging.
- Transportation: Vehicles with sensors that gather information about the machine's performance provide this data to fleet managers, who can proactively plan vehicle maintenance. Fewer unplanned downtime, lower fuel consumption and maintenance costs and shorter service time are some other features that predictive maintenance can offer in transportation companies.
- Aviation : If the maintenance of the aircraft is not correct and at the right time, it can lead to catastrophic crashes. Even the origin of predictive maintenance can be traced to aircraft maintenance. Aviation companies find PdM effective in reducing the costly effects of maintenance-related flight delays and cancellations. Another application is to help the airlines monitor engine health and performance during flights by measuring the various temperature and vibration levels.
- Automobile Industry: Predictive maintenance makes it effortless to forewarn the engine components failing and regularly monitor the engine temperature, vibration, or fluid levels. Along with the master data from the vehicles, this information can give the correct prediction of when the components tend to fail and initiate the repair before they become a problem.
- Mechanical Engineering: The earlier the detection is, the easier it is to make advancements in your plant. The cost-intensive inspections and associated downtimes are no longer a question. In the long run, your machine’s lifespan is extended.
How can CMMS support your Predictive Maintenance?
Over time, CMMS shifted manual processes and reactive maintenance to more proactive preventive and predictive maintenance strategies. CMMS has become the core of the Pdm applications, and here are a few reasons to substantiate it.
- Delivering the primary data CMMS furnishes the asset performance data that forms the initial dataset for the PdM implementation. CMMS can provide the most comprehensive and easily accessible source of historical data.
- Generate automatic tasks When the sensor detects an asset functioning outside the predefined parameters, the CMMS can create alerts and generate work orders. These alerts can initiate the maintenance teams to take preventive actions before the machine fails. For this, proper integration of both PdM and CMMS is needed as both are interdependent. The highly accurate data that the PdM yields will find its adequate application only when combined with CMMS, and CMMS without PdM cannot measure or predict the machine’s health.
- Facilitate Data interpretation The valuable asset condition data that the PdM provides, like the vibration, lubricant, heat or oil analysis, will be too large for people to manage manually. A proper maintenance management system lets the user manage data efficiently.
- CMMS as a central organisational tool A CMMS forms an integrated asset information database and delivers a comprehensive equipment report. For instance, PdM can give raw data about the machines, but CMMS take it to the next step by incorporating information from other modules like asset history, inventory, spare parts management, workforce management, repair schedules and more and thereby helping the maintenance departments to make more informed decisions.
How to establish a Predictive Maintenance Program?
A solid foundational base is paramount for establishing the predictive maintenance strategy on your production floor. Relevant training should be provided to the staff and the machine operators on how to carry out the PdM technologies. Let’s look at the measures to set PdM strategy in your organisation.
- Spot the critical assets: Identifying the assets is the first step. The one with higher repair or replacement costs makes it to the top of the list. You can also take a Reliability Centred Maintenance analysis to diagnose whether the asset is worth the PdM.
- Establishing a database: Once you have identified the assets, you now get adequate information that can contribute to actionable insights into the machine’s behaviour. The historical data for each piece of equipment can be obtained from the sources like CMMS, other maintenance records or the technician’s personal experience working on the assets. This information is vital in establishing the failure modes and developing the first versions of the predictive algorithms.
- Analyse and establish failure modes: After reviewing the previously identified assets, the failure modes can be established. This can help you decide which failures bring in more dangers and have the highest chance of occurrence.
- Implementing condition monitoring sensors and equipment: Once decided on failure modes they need to watch out for, the organisation can buy appropriate sensors and technology to monitor the parts that are most likely to fail. Various condition monitoring techniques and equipment find the application here. Be cautious and double-check your old assets, as they can cause trouble retrofitting them with modern sensors.
- Develop predictive algorithms: Devise the right modelling approach that can form the base for failure predictions. Set the predictive maintenance algorithms based on the sensor measurements and other data received.
-
Deploy to the pilot equipment:
The final stage of the implementation is testing and validating the predictive
modelling by deploying the technology to a specified set of pilot equipment.
When executed correctly, the company’s operations can witness significant
improvements.
Organising your organisation to implement a predictive maintenance program, you can jumpstart the predictive maintenance with TITAN CMMS.
What are the benefits of Predictive Maintenance?
Streamline your facility management operations with predictive maintenance! Organisations risk performing too much maintenance and wasting resources or having to deal with mechanical failures if they rely solely on preventive maintenance strategies. Reactive maintenance, on the other hand, is performed only when needed causing a high cost of unscheduled downtime. Predictive maintenance operations address these concerns as the maintenance work is scheduled exclusively when the specific conditions are met and before the assets break down. Listing the benefits down can give you a better idea.
- Lesser equipment failures As equipment failures can bring serious outcomes, regular monitoring of the equipment and process system’s conditions stands inevitable. Condition monitoring maintenance techniques allow facility managers to get real-time data about asset health and take necessary actions beforehand.
- Reduced MTTR (Mean time to Repair) By lowering machine failures and breakdowns, predictive maintenance can also lessen the time required to repair or recondition plant equipment. As soon as the sensors indicate something is wrong with the equipment and it might break down soon, technicians have the advantage of fixing it then and there before the damage gets larger.
- Increased asset lifetime Detecting machine and system problems at the earliest can increase the service life of the facility machinery by an average of 30%. The implementation of the predictive maintenance strategy can reduce not only the severity of damage but also decrease the propagation of defects. Every issue, even in an inexpensive part, can damage any crucial part, reducing the asset lifecycle.
- Precise asset data Predictive maintenance uses sensor data to predict the Mean Time Between Failures (MTFB). Having access to this data can allow the facility manager to determine the most cost-effective time to replace the machinery rather than scheduling costly maintenance tasks that won’t maintain the equipment in optimal condition in the long run. CMMS software allows viewing the maintenance and continuing operations costs that exceed the replacement costs.
- Verification of the repair effectiveness Predictive maintenance sensors conduct various actions like vibration analysis, oil analysis, thermal imaging, equipment observation, etc., verifying whether the repair was successful before the machine starts again.The need for a second shutdown to adjust the inadequate or incomplete repairs is not a question anymore.
- Improved Workplace safety Do not worry about your risk management or workplace safety anymore! Accidents in the workplace, especially the ones related to machine failures, are not only dangerous but cause substantial financial impacts. Early detection of the problem can reduce the risk of catastrophic failures and avoid injuries.
- Increased Returns Maintenance teams invest fewer resources in maintenance tools and services by avoiding complex machine breakdowns. Maintenance technicians and managers can increase work productivity by having more time to focus on vital maintenance tasks. Also, optimising the equipment conditions can reduce machine downtime, directly affecting the bottom line.
What are the six pillars of the predictive maintenance program?
Technology is only one among the many factors that contribute to the predictive maintenance program. Let’s probe the six pillars that strongly impact a strong predictive maintenance program and how they can contribute to achieving the preferred outcomes.
- PEOPLE: The predictive maintenance journey starts with the people. Every other pillar of the predictive maintenance program needs the people to build and maintain them. Data needs interpretation. Technology needs to be set up and managed. This is why everyone in the organisation needs to understand how a PdM works and why it is essential.
- DATA: A lot of information is required for a predictive maintenance program. Without accurate data from the shop floor, your efforts in identifying or predicting anomalies are wasted, and your decisions go wrong. Only data can establish the essential link between the existing asset performance and the future state of the asset. That’s why everything about the assets needs to be constantly updated.
- PROCESS: The plans and the ideas the maintenance team put forth, and it is executed, form the processes. It can either be people-driven or equipment driven. People process can be how your maintenance team do their work, which outlines how the staff interact with the machines, data, and everything else. On the other hand, equipment processes are vital as they incorporate what operations your equipment completes, how to capture asset data and how the data maps to future performance.
- TOOLS & PARTS: Tools are the instruments needed to measure the asset’s conditions and those required to inspect and repair equipment. Parts are the different elements of the equipment. Both these play an inevitable role in the predictive maintenance strategy.
- EQUIPMENT: It is essential to know which of your equipment allows you to anticipate failure on it while setting up a predictive maintenance program. The assets that fit into the predictive maintenance programs are the ones that provide good condition data with enough lead time to catch the problems before the failure occurs. Apply your predictive maintenance strategies to the most critical assets with the most observable failure modes.
- TECHNOLOGY: Technology binds all the other ingredients together and helps you manage, facilitate and optimise the other pillars of predictive maintenance. To understand how to carry out the maintenance strategy, you need to have a lot of data from various sources. What products are being run, when, the cost of all activities, and when was the last maintenance done? All these data are captured, stored and analysed with the help of several technologies like ERP, MES or CMMS software systems.