What is Total Productive Maintenance?
What is TPM? Total Productive Maintenance is a lean manufacturing approach that drives continuous improvement and is based on the idea that not just the maintenance team rather everybody in the manufacturing facility should take part in maintenance activities. Total productive maintenance (TPM) maximise equipment effectiveness through actively involving all supporting departments and continuously monitoring their operations. The ultimate goal of TPM is to optimise equipment availability and improve overall productivity.
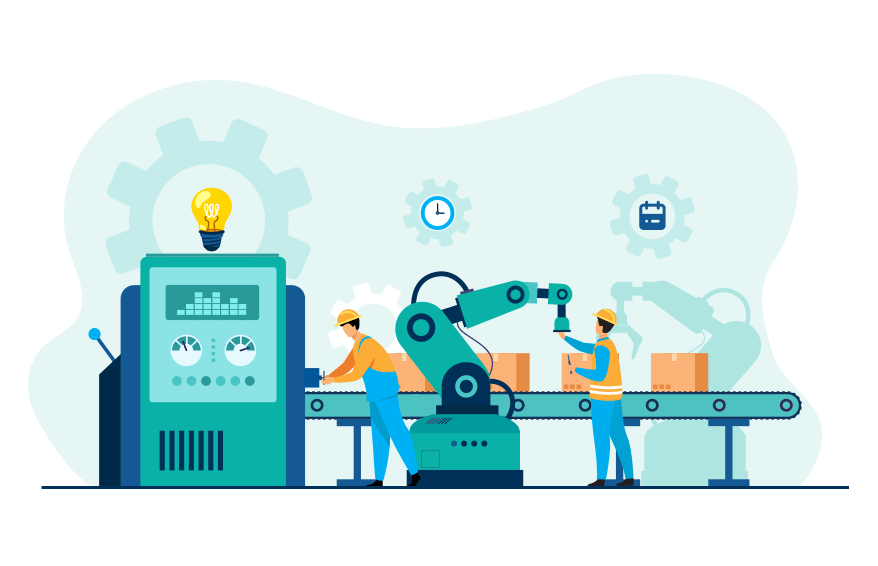
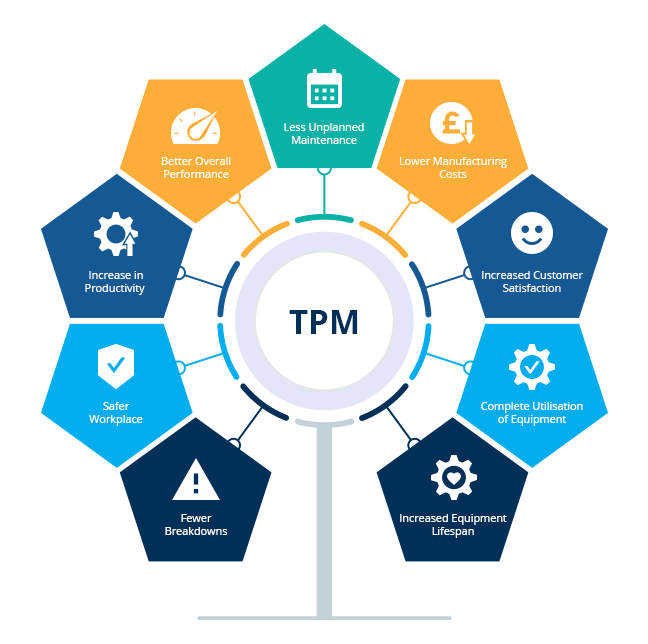
What are the advantages of TPM?
TPM standardise and organise overall procedures and benefits both workplace and production quality. There are numerous benefits that the organisation experience once they deploy the TPM strategy, including and are not limited to;
- Fewer Breakdowns
- Safer Workplace
- Increase in Productivity
- Better Overall Performance
- Less Unplanned Maintenance
- Lower Manufacturing Costs
- Increased Customer Satisfaction
- Complete Utilisation of Equipment
- Increased Equipment Lifespan
5S - The Foundation of TPM
TPM is built upon the 5S foundation, a lean tool that transforms the workplace into a more stable and organised system. An organised workplace paves the way for an efficient, productive and safer environment. The five ‘S’ stands for;
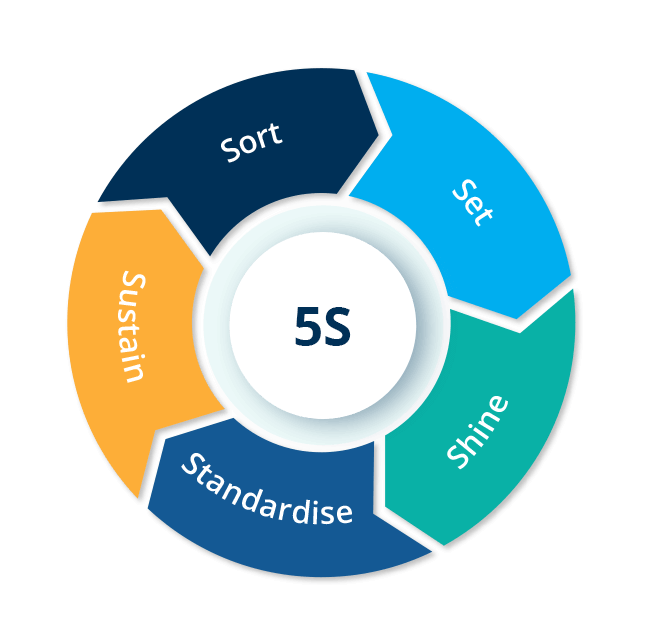
SORT
Red tag and eliminate what is not necessary at work. It identifies the redundancies and enables the team to initiate action plans for their disposal.
SET
Everything will be allotted specific storage space for easy access, creating an organised workplace where they find what they need.
SHINE
The workplace must always be kept clean as it will ease the maintenance operations that ought to occur.
STANDARDISE
Standardise the overall process at the workplace to maintain order and cleanliness.
SUSTAIN
Ensure that each step is performed regularly and with utmost care to create an environment of continuous improvement.
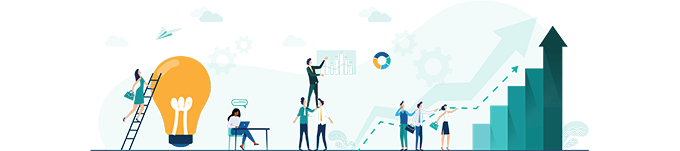
TITAN CMMS - The Key to Optimise Maintenance Operations Smart Solution
Worried about managing maintenance operations? TITAN CMMS is here to help! TITAN help organisations track and manage all maintenance-related tasks, boosts asset efficiency and performance, by creating a maintenance request, breakdown request, just do it (JDI), and tasks, at any time from anywhere.
Start Free Trial Watch Video Tell a FriendCMMS & The 8 Pillars of TPM
The pillars of Total Productive Maintenance is built upon the foundation that the 5S lean tool creates in a work environment. Let us see how CMMS plays a role in TPM deployment
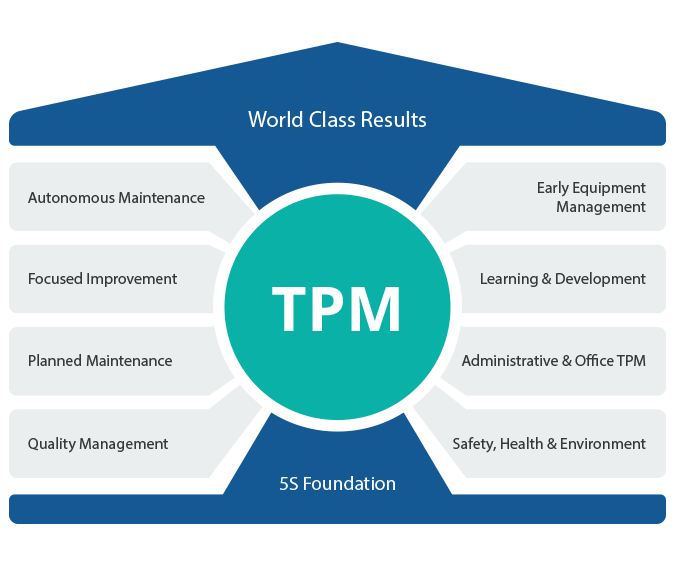
Autonomous Maintenance
In Autonomous Maintenance, the machine operators take responsibility for maintenance tasks that effectively use their skills. When maintenance-related actions like safety checks, lubrication and cleaning are done by machine operators, maintenance technicians will concentrate on more complicated maintenance tasks.
How does CMMS help? - CMMS classifies maintenance tasks the skills required to do the task and lists those who are eligible to execute the task and assign them.
Focused Improvement
Focused Improvement identifies and eliminates losses commonly encountered in manufacturing processes; as a result, the organisation can increase OEE and improve the efficiency and quality of its operations along with guaranteed minimal losses within the production process.
How does CMMS help? - The historical data of assets provided by CMMS software will help the maintenance department realise inefficiencies and enable them to implement improvement strategies.
Planned Maintenance
Planned or preventive maintenance is considered the best way to avoid breakdowns and machine downtime. It aims at improving the effectiveness of equipment by scheduling maintenance tasks to keep every asset up and running to its total efficiency.
How does CMMS help? - Using CMMS software, organisations can plan, schedule and track preventive maintenance activities and ensure they are executed on time. This helps in reducing unplanned and costly downtime.
Quality Management
Quality management in TPM is all about zero defective products and increased customer satisfaction. Addressing equipment quality issues and implementing countermeasures will eliminate the recurrence of defects. This will result in producing high-quality products every single time.
How does CMMS help? - A well maintained PM schedule means high-quality products, and CMMS easily track the maintenance schedule and deploy PM strategies on time.
Early/Equipment Management
The objective of Early equipment maintenance (EEM) is to reduce the Life Cycle Cost of equipment. Designing a new machine by incorporating the inputs of those who use it will increase reliability, operability, maintainability, and safety and reduce breakdowns and maintenance efforts.
How does CMMS help? - Historical data stored in CMMS software will help technicians review the overall performance of equipment by analysing the frequency of breakdown/repairs and further initiate plans to remove any kind of anomalies.
Learning & Development
Learning and development are essential in TPM as they will help technicians build basic maintenance knowledge and keep a regular check on equipment. It ensures that technicians are well aware of the new machinery and its maintenance operations.
How does CMMS help? - CMMS keeps track of the learning and development process, sends notifications to technicians on new maintenance operations, and ensures that they are updated with the latest information to address any scenario.
Administrative & Office TPM
TPM also addresses and eliminates areas of waste in administrative functions. Everyone must be focused on making improvements and reducing waste in their operations, improving overall process efficiency from top to bottom.
How does CMMS help? - CMMS acts as a unified platform for both the maintenance and administration departments. It is necessary to have a smooth workflow as both are an integral part of maintenance operations.
Safety, Health & Environment
Good maintenance management ensures that the environment is safe and secure and eliminates all unsafe conditions by identifying the root cause of accidents and taking necessary steps to prevent its re-occurrence.
How does CMMS help? - CMMS stores information on safety, health and environment and ensures that all processes are aligned with the health and safety regulations.
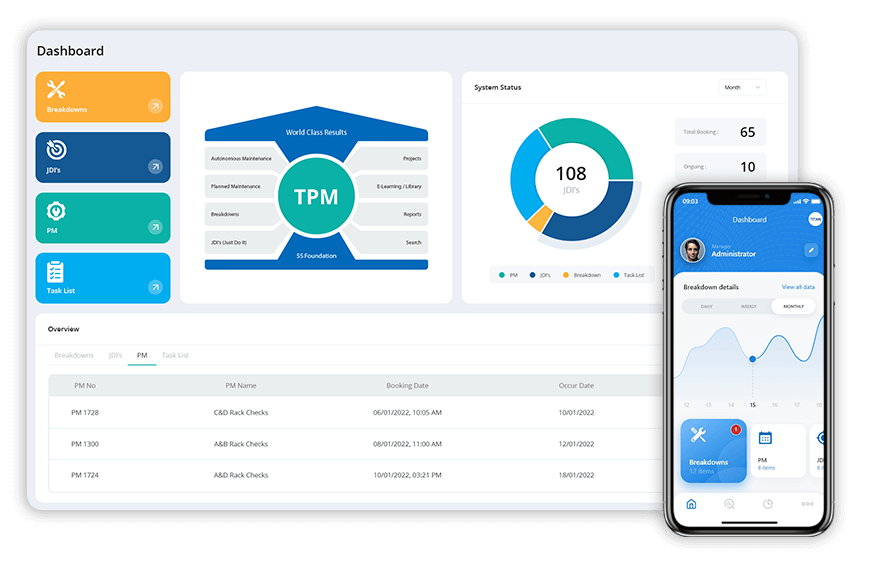
CMMS & TPM Mobile App
The combination of CMMS and TPM mobile app provides; faster execution systems, reduced error rates, improved efficiency, an enhanced lifetime of machinery, failure prediction, zero downtime and increased quality output. Gain full control of maintenance activities, work orders and other operations from wherever you are through your smartphones and analyse trends and reports to make data-driven decisions.
Contents
- What are the benefits of implementing TPM in an organisation?
- How can your organisation get started with TPM implementation?
- How does TPM differ from other maintenance practices?
- What are the tools and techniques commonly used in TPM activities?
- What is the role of autonomous maintenance in TPM?
- What is planned maintenance, and how does it fit into the TPM framework?
- How does TPM support the concept of Early Equipment Management (EEM)?
- What are the key objectives of TPM?
- How can you overcome the challenges while implementing TPM in your organisation?
- How do you measure the effectiveness of TPM in your plant?
- Examples of successful TPM implementation in real world industries
- What is the significance of focused improvement (Kaizen) in TPM?
- Can TPM be implemented in a wide range of industries?
- What is Total Productive Maintenance (TPM) in the service industry?
What are the benefits of implementing TPM in an organisation?
Implementing Total Productive Maintenance (TPM) in an organisation offers several advantages.
- Optimised Maintenance Practices
- Shifts from reactive to proactive maintenance strategies.
- Focuses on planned maintenance activities and predictive maintenance.
- Improved Equipment Reliability and Availability
- Reduces breakdowns and unplanned downtime.
- Enhances equipment performance
- Prolongs the life of machinery and assets.
- Prevents costly replacements.
- Increased Productivity
- Maximises equipment efficiency and utilisation.
- Reduces cycle times and production bottlenecks.
- Enhanced Product Quality
- Minimises defects and variations in output.
- Ensures consistent product quality and customer satisfaction.
- Prevents loss of Valuable Resources.
- Decreases scrap, rework, and resource wastage.
- Aligns with lean manufacturing principles.
- Cost Reduction
- Lowering maintenance costs through preventive measures.
- Reduces the need for emergency repairs and spare parts inventory.
- Increased Safety
- Identifies and addresses safety hazards proactively.
- Creates a safer work environment for employees.
- Better Communication and Collaboration
- Improves cross-functional collaboration between maintenance and production teams.
- Facilitates knowledge sharing and problem-solving.
- Employee Engagement
- Empowers and involves employees in equipment maintenance.
- Fosters a culture of ownership and continuous improvement.
How can your organisation get started with TPM implementation?
To initiate TPM implementation, encourage employee commitment to proactive maintenance and continuous improvement. Establish cross-functional teams and provide comprehensive training on TPM principles and methodologies. Integrate a Computerised Maintenance Management System (CMMS) to monitor equipment health, track maintenance activities, and analyse data for informed decision-making. Conduct a thorough assessment of existing processes to identify improvement areas and set clear goals that align with TPM objectives, such as maximising equipment effectiveness and reducing downtime. Encourage employee involvement and empowerment, fostering a culture of ownership and responsibility for equipment care. Regularly review progress, celebrate achievements, and refine strategies based on performance data, ensuring a sustainable and effective TPM implementation within the organisation.
How does TPM differ from other maintenance practices?
Total Productive Maintenance (TPM) stands out from other maintenance practices due to its proactive and holistic approach. Unlike traditional maintenance methods, which often focus solely on fixing breakdowns, TPM emphasises preventive and autonomous maintenance, involving operators in the process. It fosters a cultural shift, empowering employees to take ownership of equipment care ensuring machines operate at peak efficiency. TPM also focuses on improving Overall Equipment Effectiveness (OEE), addressing the root causes of issues, and eliminating defects. This comprehensive approach distinguishes TPM from reactive maintenance practices, leading to reduced downtime, enhanced productivity, and a culture of continuous improvement within the organisation.
What are the tools and techniques commonly used in TPM activities?
Total Productive Maintenance (TPM) relies on various tools and techniques to optimise manufacturing processes and improve equipment efficiency. Key tools include Overall Equipment Effectiveness (OEE) calculations, Failure Mode and Effect Analysis (FMEA), Root Cause Analysis (RCA), 5S (Sort, Set in order, Shine, Standardise, Sustain), autonomous maintenance, planned maintenance, and kaizen events. OEE helps measure equipment performance, while FMEA and RCA identify and address potential issues. 5S fosters workplace organisation and autonomous maintenance empowers operators to handle routine tasks. Planned maintenance ensures timely equipment servicing, and kaizen events involve continuous improvement efforts. When used together, these tools enhance production efficiency and minimise downtime, promoting a proactive maintenance and process improvement approach.
What is the role of autonomous maintenance in TPM?
Autonomous maintenance in Total Productive Maintenance (TPM) empowers frontline operators and production staff to take responsibility for the daily care and maintenance activities of their shop floor equipment. It involves routine inspections, cleaning, and minor adjustments to prevent equipment deterioration and breakdowns. Autonomous maintenance improves equipment reliability by fostering a sense of ownership and involving employees in maintenance tasks. It contributes to a culture of continuous improvement, making TPM a holistic approach to maximising Overall Equipment Effectiveness (OEE) and operational excellence.
What is planned maintenance, and how does it fit into the TPM framework?
Planned maintenance is a crucial part of the Total Productive Maintenance (TPM) framework. It involves scheduled activities carried out systematically to prevent equipment failures and optimise performance. These activities include routine inspections, lubrication, parts replacement, and calibration, performed at specific intervals based on the equipment's condition and manufacturer recommendations. The purpose of planned maintenance is to minimise unplanned downtime and ensure that the equipment remains in optimal working condition, thereby maximising Overall Equipment Effectiveness (OEE). This, in turn, contributes to the organisation's productivity and quality objectives.
How does TPM support the concept of Early Equipment Management (EEM)?
The TPM approach supports Early Equipment Management (EEM) by incorporating proactive maintenance strategies starting from the initial stages of equipment design, procurement, and installation. EEM emphasises the importance of considering maintenance requirements and equipment reliability throughout the equipment's life cycle. TPM helps achieve this goal by promoting a preventive and predictive maintenance culture, encouraging collaboration between maintenance and engineering teams. By integrating EEM principles, TPM ensures that equipment is efficient during production and easier to maintain, which leads to improved equipment reliability, reduced downtime, and lower lifecycle costs.
What are the key objectives of TPM?
TPM objectives aim to maximise equipment effectiveness, minimise breakdowns, reduce production losses, and eliminate defects. TPM empowers employees to take proactive ownership of equipment maintenance, ensuring that machines operate efficiently. By focusing on preventive and autonomous maintenance, TPM minimises unplanned downtime, improves Overall Equipment Effectiveness (OEE), enhances product quality, and reduces costs. It fosters a culture of continuous improvement by involving all employees in the maintenance process and aligning with lean manufacturing principles by optimising production processes.
How can you overcome the challenges while implementing TPM in your organisation?
Overcoming challenges during TPM implementation involves proactive strategies. Provide comprehensive training to employees to enhance their skills and understanding of TPM principles. Foster strong leadership and employee engagement, ensuring everyone aligns with the TPM goals. Establish clear communication channels to address concerns promptly. Utilise change management techniques to mitigate resistance and foster a positive attitude towards TPM. Implement regular performance monitoring using tools like CMMS to track progress and identify bottlenecks. Encourage collaboration and continuous learning where employees can share insights and best practices. Lastly, celebrate small victories to boost morale and sustain motivation, ensuring a smoother TPM implementation process within the organisation.
How do you measure the effectiveness of TPM in your plant?
When measuring the effectiveness of Total Productive Maintenance (TPM) in a plant, Key Performance Indicators (KPIs) such as Overall Equipment Effectiveness (OEE), Mean Time Between Failures (MTBF), and Mean Time To Repair (MTTR) are analysed. OEE assesses equipment efficiency by considering availability, performance, and quality rates. A reduction in MTBF indicates improved reliability, while decreased MTTR signifies quicker issue resolution. Regular reviews, operator feedback, and continuous data analysis are crucial to assessing TPM's impact on maintenance costs, defect rates, and employee engagement. These metrics help gauge improvements in equipment uptime, productivity, and Overall Operational Efficiency (OOE), providing a comprehensive evaluation of TPM effectiveness in the plant.
Examples of successful TPM implementation in real world industries
Several organisations have successfully implemented Total Productive Maintenance (TPM) to improve manufacturing processes and achieve significant results. One notable example is Toyota, where TPM played a crucial role in the company's lean manufacturing journey. Toyota focused on empowering employees to take ownership of equipment maintenance, ensuring that machines were well-maintained and operated optimally. This approach reduced downtime, improved Overall Equipment Effectiveness (OEE), and increased productivity. Another example is Procter & Gamble (P&G), which implemented TPM across its global manufacturing facilities. By involving employees at all levels and emphasising preventive maintenance, P&G significantly reduced breakdowns, enhanced product quality, and lowered maintenance costs. These success stories highlight the effectiveness of TPM in enhancing operational efficiency and achieving sustainable improvements in various industries.
What is the significance of focused improvement (Kaizen) in TPM?
Focused Improvement, known as Kaizen in the context of TPM, holds immense significance as it promotes continuous small-scale improvements in the manufacturing process. Kaizen encourages employees at all levels to identify and address inefficiencies, leading to enhanced productivity, quality, and equipment performance enhancements. In the TPM framework, these continuous improvements contribute to Overall Equipment Effectiveness (OEE) by systematically eliminating minor stoppages, reducing setup times, and enhancing operating speeds. Kaizen ensures that the organisation adapts to changing demands, minimises waste, and maintains high levels of efficiency. Hence, it aligns perfectly with TPM's goal of maximising equipment effectiveness and operational excellence.
Can TPM be implemented in a wide range of industries?
Yes, TPM can be implemented across a wide range of industries, including manufacturing, healthcare, logistics, and services. Its principles of proactive maintenance, employee involvement, and continuous improvement are adaptable to various sectors. Whether in automotive production, hospital operations, or supply chain management, TPM enhances efficiency, reduces downtime, and improves overall productivity. By fostering a culture of ownership and continuous refinement, TPM proves beneficial in diverse industries, ensuring equipment reliability and operational excellence.
What is Total Productive Maintenance (TPM) in the service industry?
In the service industry, Total Productive Maintenance (TPM) refers to a systematic approach that ensures the continuous functioning of equipment and facilities to provide uninterrupted services. While equipment in the service industry might differ from manufacturing, TPM principles, such as preventive maintenance, employee involvement, and minimising downtime, remain crucial. In services like healthcare, hospitality, or transportation, TPM aims to maximise the reliability and manages your critical assets, ensuring seamless operations. TPM in the service industry enhances service quality, reduces disruptions, and improves customer satisfaction and operational efficiency.
Frequently Asked Questions
- Unplanned Stops
- Planned Stops
- Small Stops
- Slow Cycles
- Production Defects
- Startup Defects