What are Maintenance KPIs?
Maintenance KPIs are performance metrics that help to measure the effectiveness of the overall maintenance process. The progress of the maintenance team is tracked along with the organisation's overall performance. These KPIs estimate how well the operations are carried out in achieving the maintenance goals. They form the benchmarks for the facility and are the record of the present condition of the maintenance work, how far still it needs to go and what additions should be made to get there.
They can be defined as the quantifiable goals in an organisation that reflect the endpoints you are reaching. Common facility targets that the standard Maintenance KPIs revolve around include efficiency, costs and spending, safety and compliance, asset performance, downtime, work order management and inventory management.
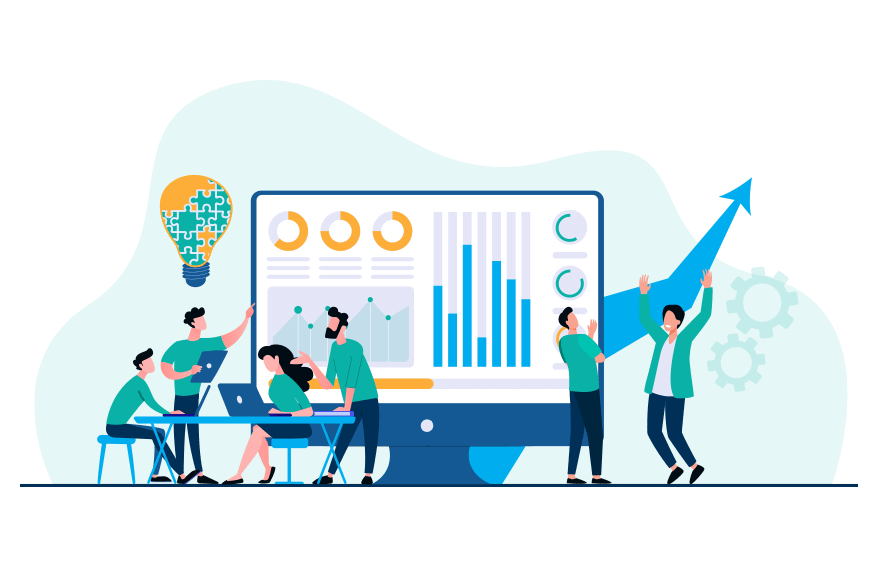
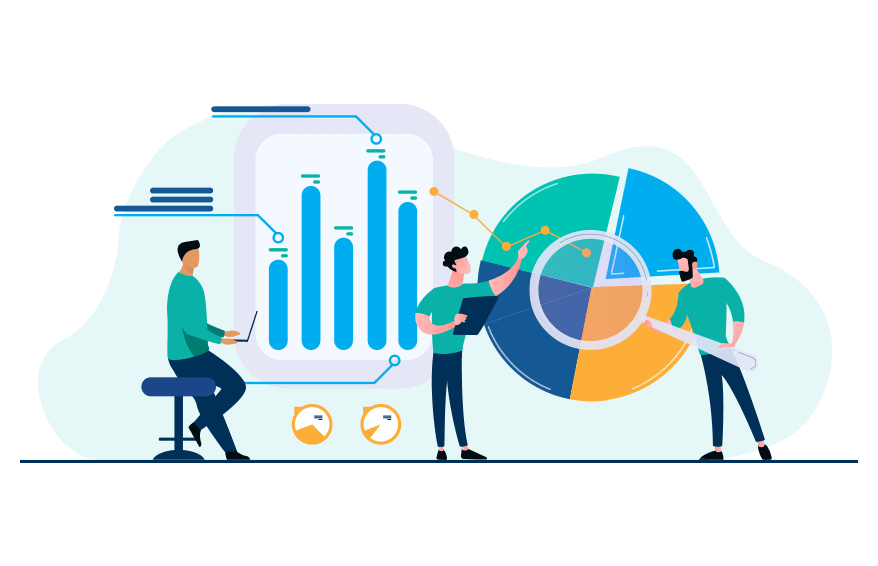
What are Maintenance Metrics?
Maintenance metrics are measurements capable of giving insights into how the operations are carried out in your facility. The daily maintenance activity is quantified, which can help track how the people and assets work. Recording these numerical later helps calculate and analyse the impact of these activities on the organisation.
Metrics help to understand how everyday tasks are affecting the bigger picture. This gives control over the maintenance operations and practical ways to improve work.
What's the difference between the Maintenance Metrics and Maintenance KPIs?
Though the Maintenance metrics and Maintenance KPIs are used interchangeably, there is a slight difference between the two.
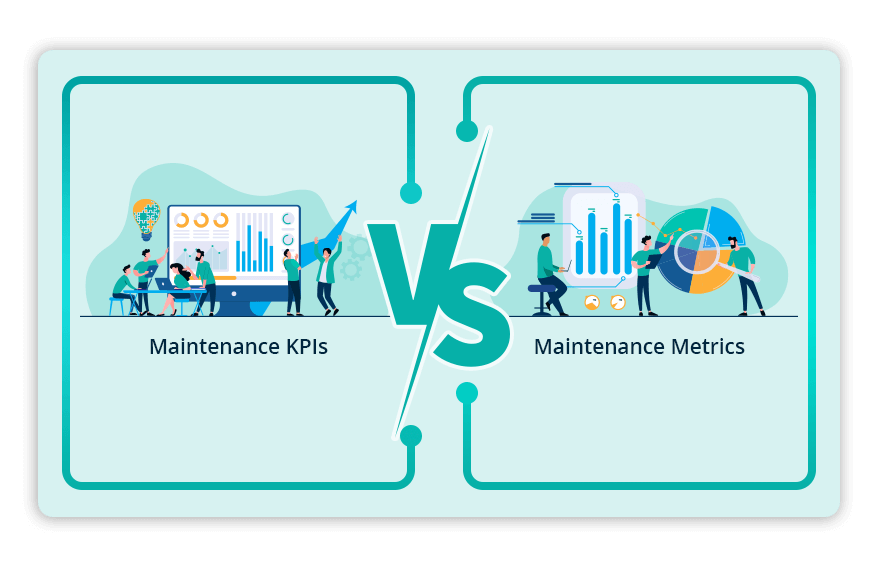
Maintenance KPIs
- KPIs are strategic.
- Connect organisational performance to maintenance performance.
- KPIs are the target that business aims at.
- KPIs refer to the target number themselves. They are measurable values that show how effective the maintenance objectives can be, unlike the metrics that track the specific process's status.
Maintenance Metrics
- Maintenance metrics are tactical.
- Relates maintenance performance to maintenance actions.
- Arrows used for firing the target.
- Maintenance metrics are the measurements that provide insights into the effectiveness of the maintenance team and system operations. These performance metrics can quantify the daily maintenance activities compared to their target numbers.
For example, if the KPI is to minimise the average maintenance costs by 10% within the next quarter, you can track the maintenance metrics to monitor the effectiveness of your efforts. Metrics like Maintenance Overtime, Planned Maintenance Percentage, and Overall Equipment Effectiveness can help reach the KPI.
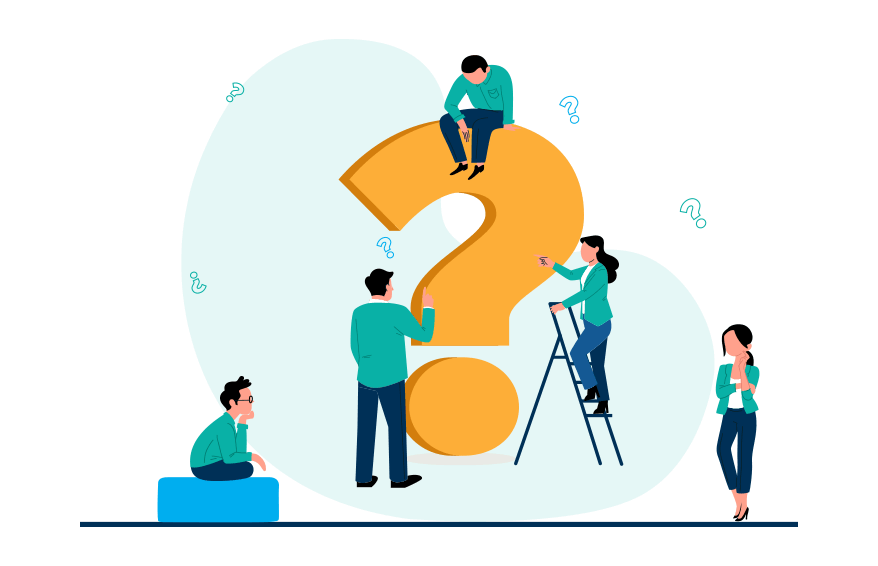
Why should you track the Maintenance Metrics?
Any company that owns many valuable assets or equipment spends a significant amount on maintenance. A single breakdown can stop or negatively affect the production cycle. To avoid this, the maintenance KPIs need to be tracked. Maintenance metrics can help keep maintenance costs low by preventing unplanned downtime.
Common Maintenance Metrics
The Maintenance Metrics are part of the more extensive process of the company's overall business goals. The goals and action plans are set for the individual units in line with the comprehensive business strategies. The maintenance managers decide which Maintenance KPIs to track and identify the significant maintenance pain points. For every industry, it varies; whichever problem prevents reaching the predefined business goals is to be given priority. Here we have listed some of the commonly used metrics that can be used to keep the maintenance operations functioning efficiently.
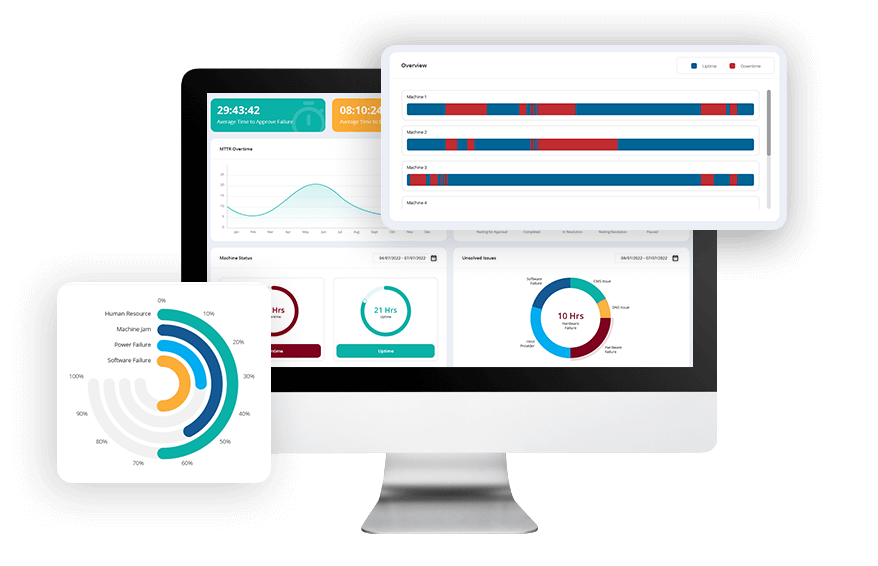
TITAN CMMS - The Key to Optimise Maintenance Operations Smart Solution
Worried about managing maintenance operations? TITAN CMMS is here to help! TITAN help organisations track and manage all maintenance-related tasks, boosts asset efficiency and performance, by creating a maintenance request, breakdown request, just do it (JDI), and tasks, at any time from anywhere.
Start Free Trial Watch Video Tell a FriendOperational Metrics
Operational Metrics measure the way people work. Measuring the team's performance makes eliminating inefficiencies, redundancies and reactive maintenance easy. Operational metrics help the team manage the people to achieve their full potential. Planned Maintenance Percentage(PMP) and Preventive Maintenance Compliance(PMC) are the two common KPIs that come under the category of operational metrics.
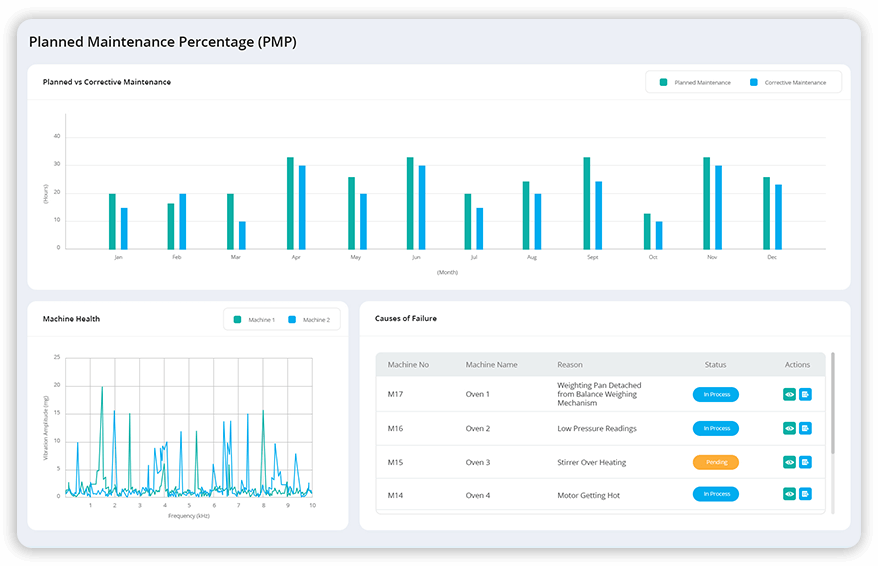
Planned Maintenance Percentage(PMP)
PMP is a diagnostic tool for identifying the underlying issues by measuring the number of planned maintenance activities compared to other maintenance tasks. PMP is the percentage of the total maintenance hours spent on the scheduled maintenance tasks in a given period. PMP KPI tracks the health of a preventive maintenance program and identifies the opportunities to reduce reactive maintenance. The cause of failures, inefficiencies and broken maintenance processes are pointed out by PMP and hence they are fixed. Regular calculations of PMP are a way to keep a tab on the overall maintenance effectiveness. A low score of PMP indicates the extra time spent on the reactive maintenance, which further leads to a thorough review of the maintenance workflows, equipment history and root cause analysis.
Benefits of using PMP
How is Planned Maintenance Percentage calculated?
Planned maintenance refers to the maintenance activities that are planned, documented and scheduled. Here a process is created for carrying out the recommended equipment upkeep from the beginning to the end. Preventive Maintenance, condition-based Maintenance and run to failure maintenance are the common kinds of PMP.
PMP is calculated as
TOTAL MAINTENANCE HOURS
The world-class standard for PMP is 85%.
Preventive Maintenance Compliance(PMC)
Preventive maintenance Compliance, otherwise Scheduled Compliance, measures the percentage of the preventive maintenance tasks completed in a specified time. The preventative maintenance program's effectiveness and the process's efficiency are tracked with this KPI. The operations & maintenance managers use the Schedule Compliance metric to determine the effectiveness of the scheduled tasks. The percentage of the completed work orders before their due dates over a given period is calculated.
Scheduled compliance is one way to illustrate how successfully the maintenance teams are completing the preventive maintenance tasks as planned.
Maintenance experts consider the world-class standard for PMC to be 90%.PMC, along with PMP and Scheduled Maintenance Critical Percent(SMCP), allows the optimisation of maintenance schedules, effective use of resources and ensuring that the assets are reliable as possible.
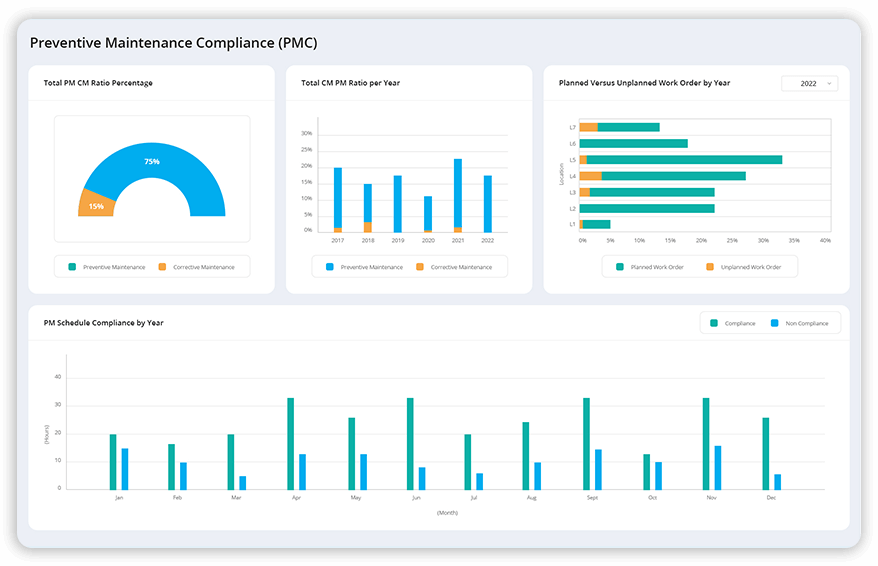
How is the PMC calculated?
PMC is the percentage of the preventive work scheduled and completed in a set time.
TOTAL SCHEDULED PMs
Asset Performance Metrics
Asset Performance metrics measure the way equipment works. Assets are the foundations on which the company is built. So the performance of the assets reliably for a long time is essential for the company. Asset metrics track how maintenance impacts the asset performance and ensure equipment always runs as it should. The asset performance metrics category includes mainly Mean Time To Repair, Mean Time To Failure,Maintenance Percentage of Replacement Asset Value and Overall Equipment Effectiveness.
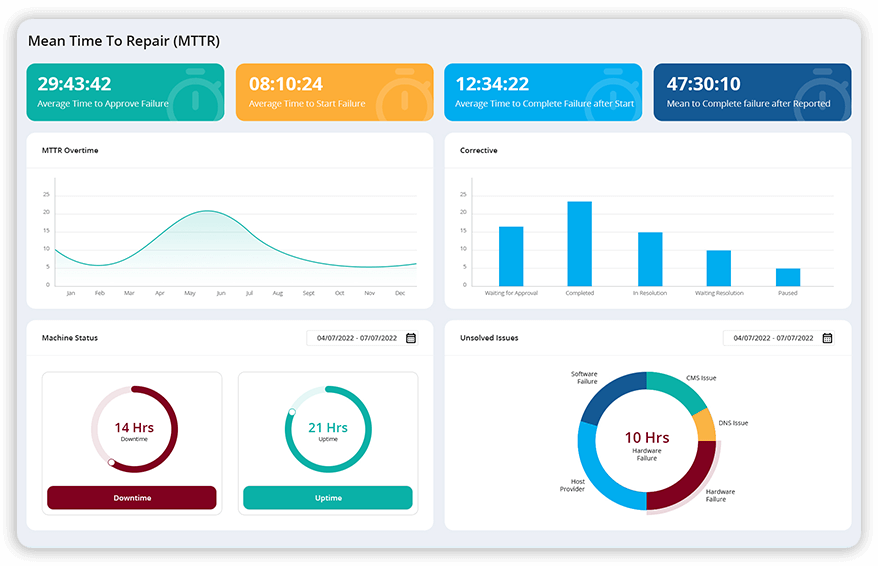
Mean Time To Repair(MTTR)
Mean Time To Repair refers to the average time the maintenance team spends on diagnosing, fixing and recovering the failed pieces of equipment. MTTR provides a useful productivity benchmark for organisations seeking to reduce prolonged repair times and their associated expenses. MTTR is a standard measure that the maintenance departments use to improve asset efficiency, minimise unplanned downtime, boost bottom lines and assess equipment value. Using the MTTR analysis, the organisations evaluate the quality and effectiveness of their maintenance strategies, processes and practices. In most industries, organisational effectiveness depends on asset reliability. Critical equipment breakdowns often beget extended repair times, technician overtime, outsourced contractor fees and lost production schedules. An ideal MTTR time is below 5 hours though the metric varies considerably based on the asset type and importance. The metric provides an understanding of the maintenance schedule, replacement parts purchases and maintenance task completion.
MTTR includes the time taken to :
How is MTTR calculated?
MTTR is equal to the average duration of each stoppage due to failure. This can be calculated by taking the total downtime that goes into the repair and recovery of the equipment divided by the number of times the same equipment has stopped its operations.
# OCCURRENCES OF STOPPAGES
MTTR is not dependent on uptime. It is only quantified by the average time each stoppage last, regardless of the period between the instances of the downtime.
How to improve MTTR?
The four stages of MTTR include problem identification, diagnosis, repair and verification. The primary goal here is to reduce the time spent in each step. Some ways to reduce MTTR include:
Mean Time Between Failure(MTBF)
MTBF measures the standard amount of time between the expected equipment failures of an asset performing under the normal operational usage condition. MTBF is used to inform equipment design, optimise preventive maintenance scheduling and maintain reliability for the essential pieces of equipment. Being the uptime between the two failure states of a repairable system, MTBF is only used in conjunction with repairable assets.
The assumption that the tangible assets failures are inevitable makes the maintenance managers calculate the MTBF. The higher the MTBF, the more the asset is likely to operate without interruption for an extended period. The "failure" defined here is the equipment to be completely out of service operations, and minor fluctuations are not categorised under MTFB.
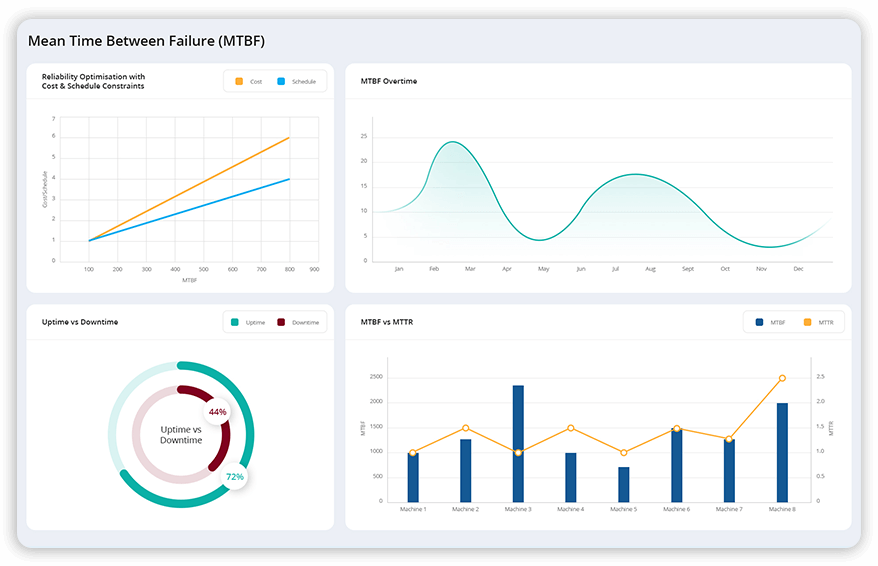
How is MTBF calculated?
MTBF is calculated by dividing a repairable asset's total uptime by the asset's number of failures within a given period.
NUMBER OF FAILURES OF ASSET WITHIN GIVEN TIME PERIOD
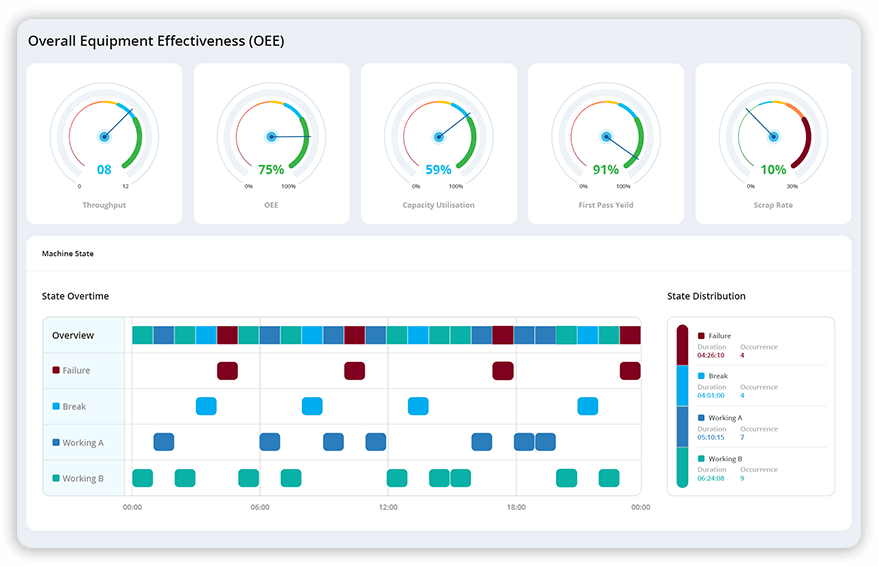
Overall Equipment Effectiveness(OEE)
Overall Equipment Effectiveness measures the asset's productivity level. OEE is the combination of three factors that determine the asset's efficiency during the manufacturing process. The asset availability factor decides how often an asset performs when needed. The asset performance factor determines how much the asset produces, and the asset quality factor determines how many high-quality items the asset produces.
An OEE score of 100% means that all the items that are produced are without any defect(quality) as fast as possible(performance), and there is zero unplanned downtime(availability).
How is OEE calculated?
OEE is calculated by combining all the factors- availability, performance and quality.
Wherein the availability is calculated by dividing the total run time of an asset by the total planned production time of an asset. It excludes the planned shutdowns for preventive maintenance.
Performance is measured by dividing the system throughout by the maximum possible throughput.
Quality is measured by the number of usable units produced divided by the total units started.
And finally,
Maintenance Percentage of Replacement Asset Value(MPRAV)
Maintenance Percentage of Replacement Asset Value(MPRAV) is the amount spent on maintenance compared to the asset's value. It measures how well a cost-effective maintenance strategy is being carried out.
MPRAV takes two factors into consideration, the cost of maintenance and the replacement value of the asset. It avoids the other expenses for production, disposal etc.
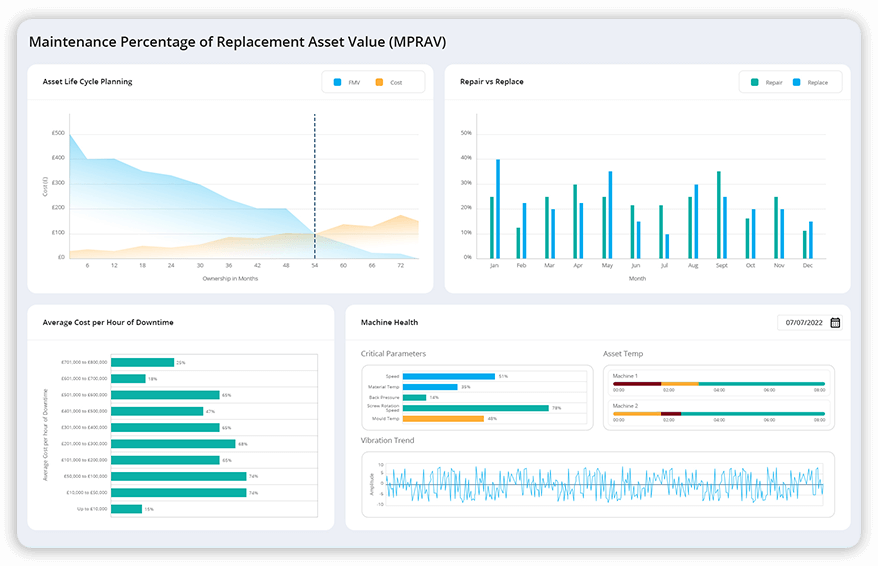
How is MPRAV calculated?
The MPRAV calculation includes two parts, one for the maintenance costs and one for replacement value.
Maintenance costs are calculated by summing up the costs of parts, labour and the other expenses of all closed work orders in a given period for a particular asset.
Replacement asset value is the cost to replace the existing asset with a new identical asset.
REPLACEMENT ASSET VALUE
Inventory Metrics
Inventory Metrics measure the way parts work. Good inventory management brings about good maintenance. Tasks are carried out quickly when the correct part is placed in the right location. Inventory metrics give the maintenance team the information needed to make better decisions about spare parts and maintenance operations.
Turn Over Ratio, and Slow-moving & Obsolete parts percentage are the commonly used inventory maintenance KPIs.
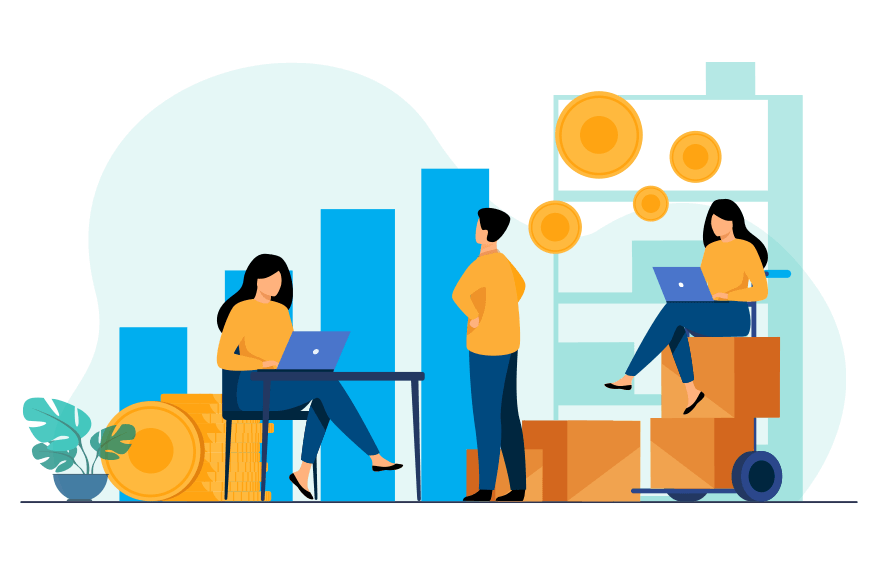
Turn Over Ratio
Turn Over Ratio, otherwise known as Stock Turn Ratio, measures the effectiveness of spare parts management. It calculates whether the amount of money spent on the inventory is adequately utilised and whether it is making the necessary impact on the facilities.STR indicates whether the right mix of inventory is being used and the right amount of money is invested in the inventory. It specifies the replenishment rate of the stocks.
How is Turn Over Ratio calculated?
Inventory Turns is the ratio of the value of the stock purchased over a specified period to the value of stocks in hand currently.
Value of stock in hand
A higher value indicates fast-moving inventory and vice versa. A low value can also indicate that the materials could be overstocked, and still, there is an inflow of the materials despite holding massive quantities. The ideal number of Inventory Turns varies not only in industries or companies but also with the type of stocks.
Slow Moving Parts Percentage and Obsolete Parts Percentage
These KPIs help point out the inventory items that are rarely used or too old to be used for repairs and replacements. A slow-moving part is any inventory placed idly in the storeroom for an extended period with little or no usage. On the other hand, an obsolete part can be defined as one that cant be used any longer because its age makes it deficient or unable to fit with the new equipment. These two metrics allow effective management of the inventories and their maintenance in a faster and better way.
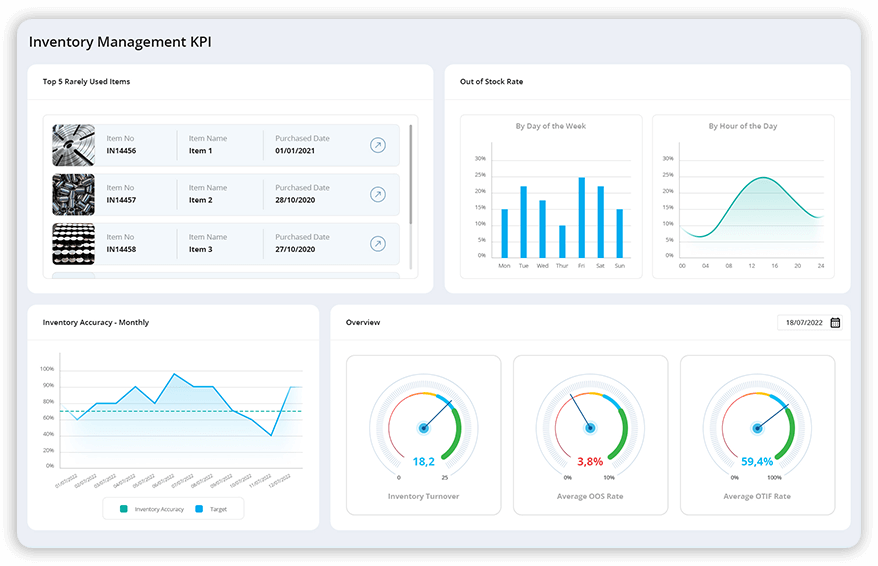
How are Slow Moving Parts Percentage and Obsolete Parts Percentage measured?
The slow-moving parts percentage is calculated by multiplying the total number of slow-moving parts by 100 and then dividing the result by the total number of spare parts. Each facility has a different version of what is slow or not; hence, the slow-moving parts are difficult to define. Typically the slow-moving parts are the parts that cost more to store and maintain between the users than if they were ordered only when needed.
# of spare parts
# of spare parts
Lets have a look into other common categories of Maintenance KPIs also.
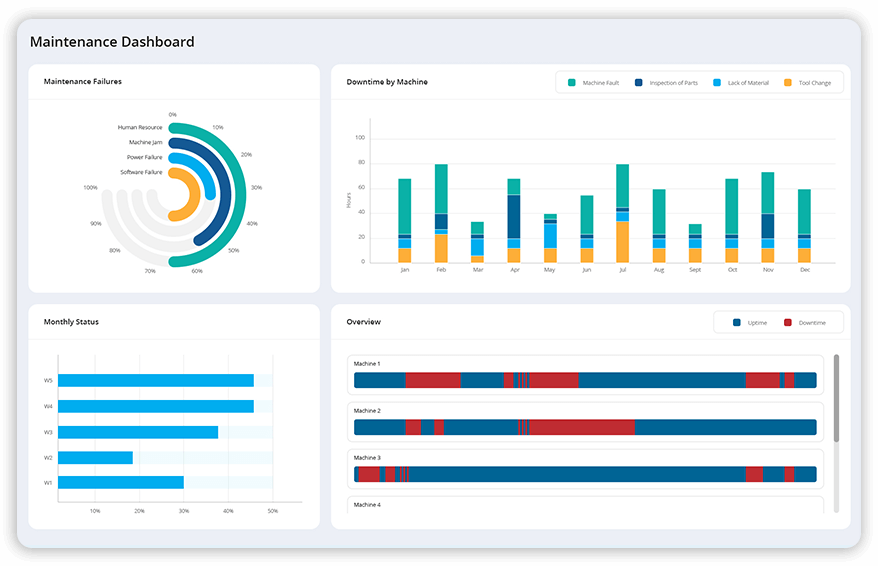
Equipment Downtime
Equipment Downtime or Unscheduled Downtime is costly for asset-intensive industries. Periodic tracking of downtime is crucial in establishing a baseline for the effectiveness of all maintenance activities. One way to reduce the downtime is to place the critical equipment in the Preventive Maintenance schedules under the guidelines. A routine maintenance schedule not only reduces costly breakdowns but will extend the asset life cycle. Tracking the equipment downtime is very important for having a good idea of the facility's uptime works which acts as the diagnostic tool for the facility's maintenance and production efforts. A high equipment downtime indicates that the preventive maintenance is not being performed properly or there are problems with how the production is set up. Low equipment downtime is a sign of a generally healthy production environment. A 10% or less unscheduled downtime is to be aimed as it is an indication that the equipment is running at 90% availability or greater.
Maintenance Backlogs and Overtime
Maintenance backlog is usually measured in work days or weeks. The time required for a specified number of workers to complete the pending maintenance tasks is calculated here. All the activities related to preventive Maintenance and other outstanding Maintenance, such as required corrective maintenance, are taken into consideration while calculating.
Not every task in the backlog will be equally urgent, and sometimes backlogs can also be the indicator of optimised staffing. But the problem arises when the maintenance schedules are delayed by the emergency work and inefficient prioritisation models. Neglected tasks in the backlog can become delayed maintenance which inevitably can cause more severe breakdowns and downtime.
The maintenance backlog aims to have around six weeks' worth of tasks per technician. Though the ideal amount of backlog varies for each business, measuring the amount of pending work can be a helpful metric in maintenance management.
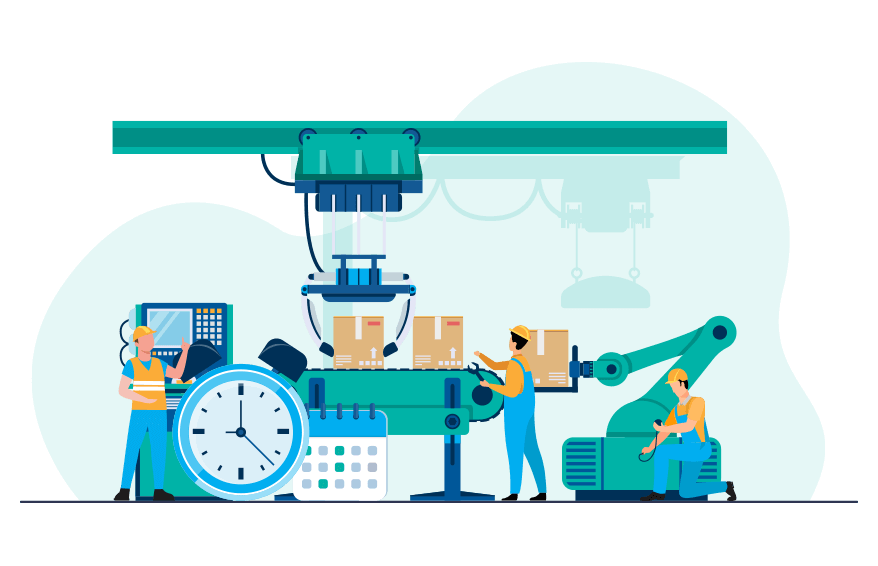
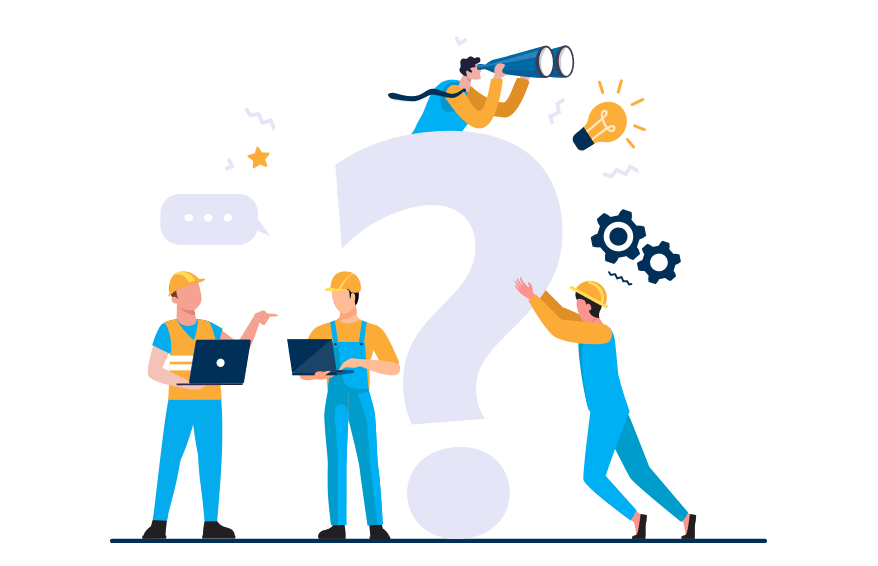
What Maintenance KPI should you be measuring?
Maintenance KPIs can only bring out the desired output when used relevantly without blindly adopting it. While choosing the metrics, the following steps can help you understand what metric is best for the organisation.
- What are the objectives of your organisation?
- Creating a big picture of the goals of the organisation to be achieved
- Linking these objectives to the KPIs to understand the desired outcome.
- Deciding how the plan is to be implemented and how the progress is to be measured.
- Getting the feedback from the various technicians and operators and analysing which KPI to be attached to the particular process.
How do you use metrics to improve maintenance operations?
When used correctly, maintenance metrics help bring real change to the organisation.
Reduce Downtime:
Maintenance metrics determine where the downtime is caused and why. For example, MTBF and MTTR help identify whether a weak work order process causes the fundamental issue.
Improve health and safety
Maintenance metrics like the PMP and PMC can help prevent accidents and pass audits.
Cut costs:
The unnecessary money spent is identified with the help of the KPIs. The Stock Turn Ratio is one example that can locate the overstocking and understocking of inventory.
Increase efficiency
Efficient assets are linked to efficient maintenance.OEE is a tool that can evaluate people, processes and tools that impact production.