What is Breakdown Maintenance?
Maintenance that is performed on equipment that is currently unusable or has broken down is known as breakdown maintenance. Though it is costly when compared to preventive maintenance a proper maintenance schedule will lower the chances of unplanned breakdowns. Generate work orders for breakdown maintenance as soon as they occur and allocate them to technicians to address the issue.
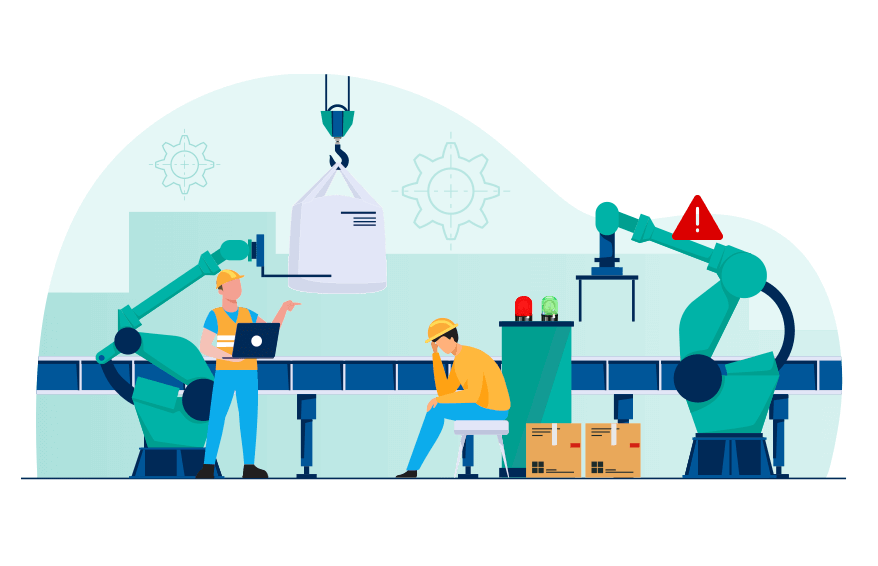
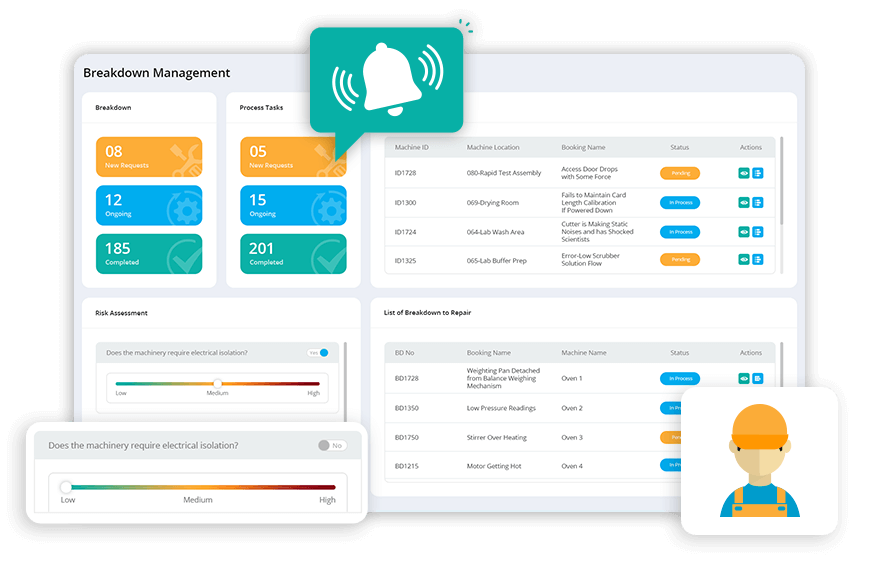
Faster Breakdown Maintenance with Real-Time Alerts
Response is critical in maintenance management. As soon as a breakdown occurs, notifications are sent to the maintenance team to address, run root cause analysis, identify and close issues. As breakdowns are mostly unplanned, we have to ensure that resources are available to address issues on time. TITAN identifies the nearest and available technician and notifies them about the assigned work order.
Identify & Eliminate Equipment with Frequent Breakdown History
Imagine wasting time repairing an equipment every single day, it absolute waste of money and time. Using TITAN CMMS, maintenance teams can manage and keep track of maintenance history allowing organisations to identify and replace equipments with more frequent breakdowns. Breakdown history/maintenance timeline records all maintenance activities that took place, enabling teams to make accurate decisions regarding equipment disposal.
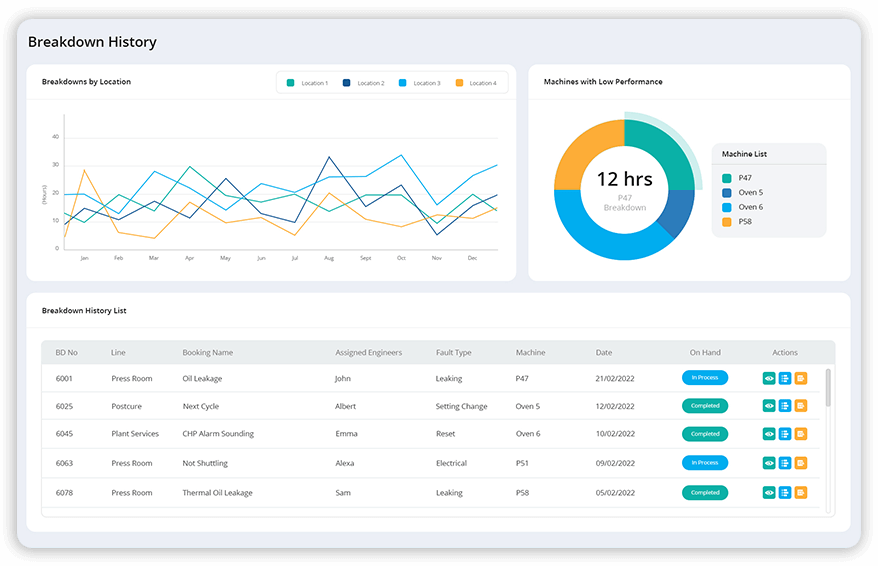
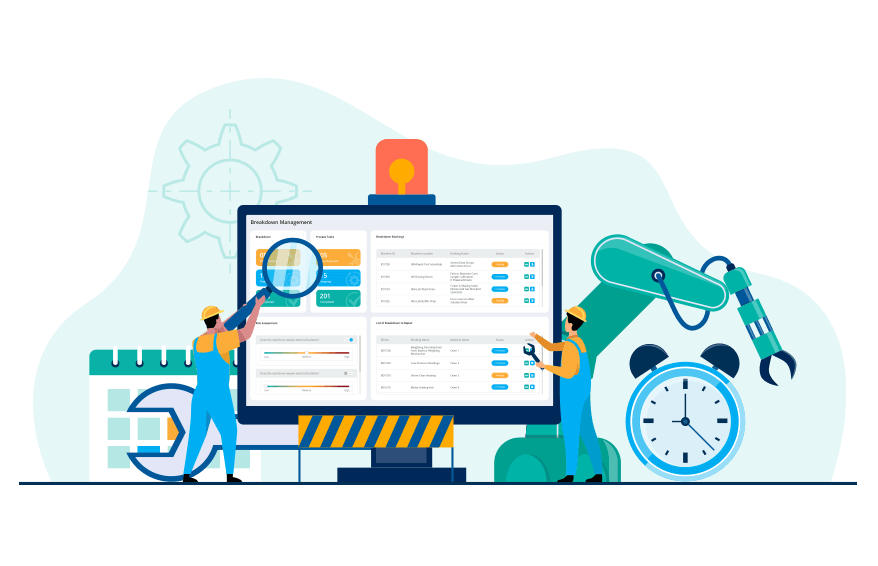
Reduce Costly Downtime
Due to Breakdowns
An innovative equipment management software is the need of the hour! A proper preventive maintenance (PM) schedule helps reduce the frequency of sudden breakdowns and reduces costly downtime. Though unexpected breakdowns will happen, preventive and predictive maintenance schedules will reduce the risk associated with equipment breakdown.
Asset Identification and Incident Reporting
Associate breakdowns with specific equipment or assets, allowing for targeted maintenance and tracking of recurring issues. Easily report breakdowns with detailed descriptions, enabling swift identification of issues and initiation of repair processes. Integrate with inventory systems to ensure availability of required spare parts for prompt repairs.
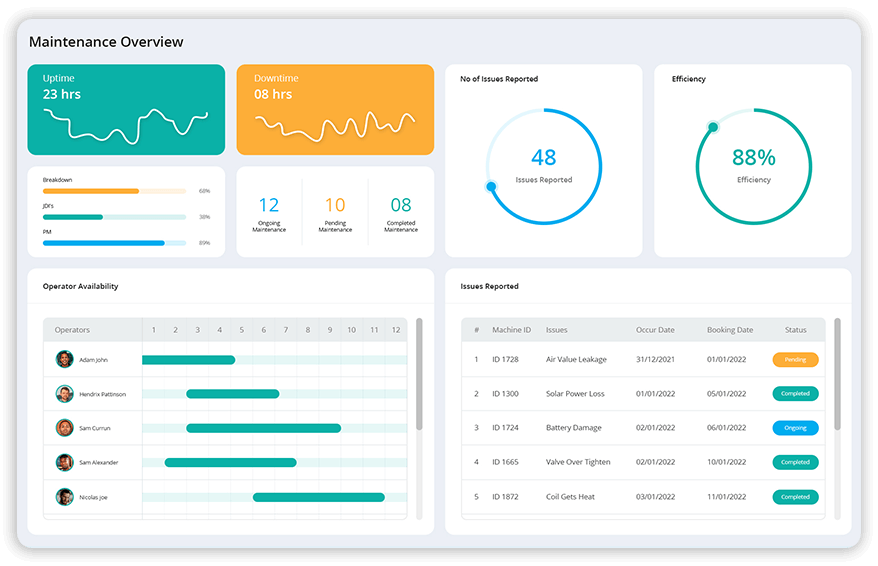
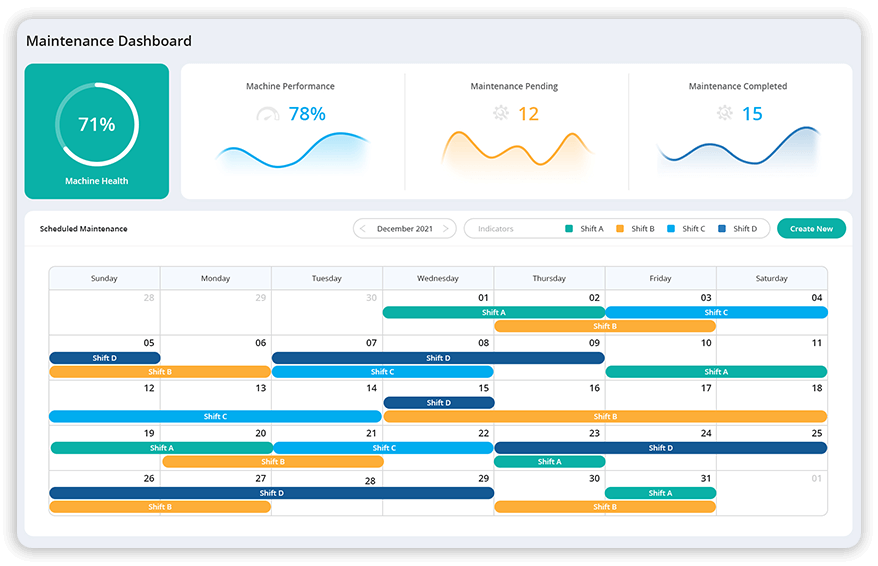
Automate Work Order Generation
Create work orders directly from breakdown reports, ensuring systematic documentation and organised workflows. Assign priority levels to breakdowns based on their impact on operational activities. Implement escalation procedures for unresolved breakdowns, ensuring critical issues receive appropriate attention on time.
Stay connected and in control with Mobile Accessibility
Access breakdown management on mobile devices, allowing technicians to report and address issues on the go. Schedule and manage maintenance tasks from anywhere following breakdown resolutions. Facilitate communication among maintenance teams, supervisors, and stakeholders to coordinate efforts and share updates easily.
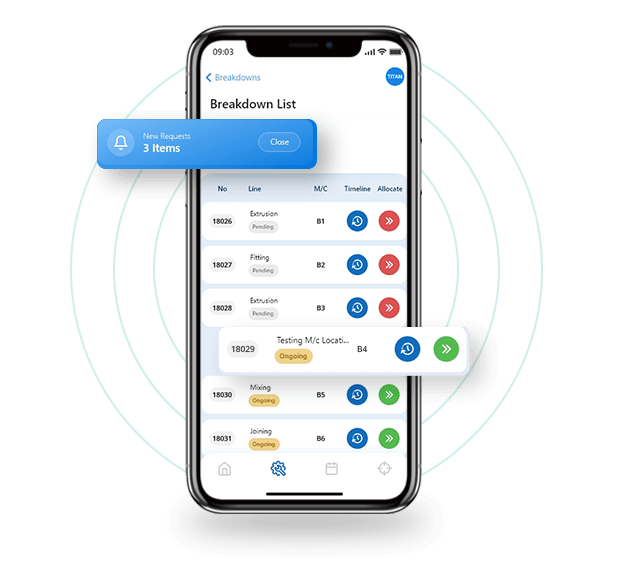

Integration with Maintenance Calendar
Ensure immediate repairs and long-term maintenance efforts. Maximise uptime and minimise operational disruptions. Synchronise breakdown management with the maintenance calendar, teams can proactively address issues, optimise asset reliability, and streamline maintenance workflows effortlessly.
TITAN CMMS - The Key to Optimise Maintenance Operations Smart Solution
Worried about managing maintenance operations? TITAN CMMS is here to help! TITAN help organisations track and manage all maintenance-related tasks, boosts asset efficiency and performance, by creating a maintenance request, breakdown request, just do it (JDI), and tasks, at any time from anywhere.
Start Free Trial Watch Video Tell a FriendRun-to-Failure &
Emergency Breakdowns
Run-to-failure maintenance are expected to happen in least important and inexpensive equipment and the orgainsation is prepared to take control of situation. On the other hand emergency maintenance takes place when an equipment stops working unexpectedly and needs to be handled with utmost care as these repairs must be completed ASAP.
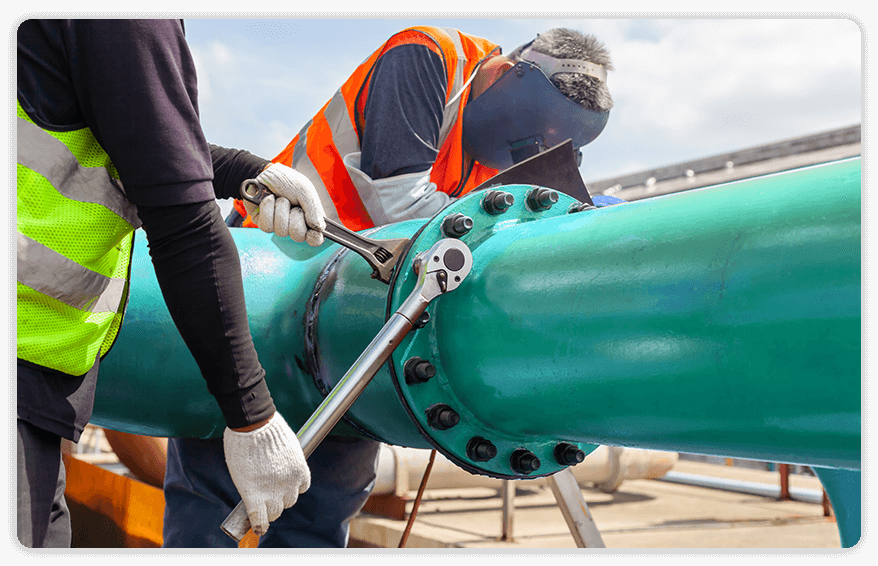
Contents
- How does the CMMS prioritise and assign urgency levels to reported breakdowns?
- What benefits are gained from synchronising breakdown management with the CMMS Maintenance Calendar?
- How does CMMS utilise performance analytics to track breakdown frequency?
- Can you assess the performance of the maintenance team with CMMS insights?
- In what ways does the CMMS empower technicians to report breakdowns?
- How does the CMMS streamline communication?
- Can the CMMS automate escalation procedures for unresolved breakdowns?
- How does CMMS facilitate Root Cause Analysis (RCA) to identify patterns and trends in equipment failures?
- What mechanisms does the breakdown management feature offer for real-time notifications and alerts?
- What documentation and attachments can be associated with breakdown reports to facilitate efficient repairs?
- How does the breakdown management feature contribute to improving Overall Equipment Reliability?
- How can the integration of CMMS with other inventory systems ensure the availability of spare parts for repairs?
- Can CMMS collaborate with multiple users on data capture tasks simultaneously?
- How can I customise the CMMS software to match my specific data collection needs?
- Is there a way to track and audit user actions and changes made to the captured data in CMMS?
- How does the CMMS software handle data validation and ensure the accuracy of captured information?
How does the CMMS prioritise and assign urgency levels to reported breakdowns?
The CMMS employs an intelligent algorithm to analyse and assign urgency levels to reported breakdowns swiftly. By evaluating factors such as the impact on operations, potential safety risks, and criticality of the affected equipment, the system ensures that maintenance teams focus their efforts on addressing the most pressing issues first. This prioritisation mechanism optimises resource allocation and minimises downtime, effectively enhancing Overall Equipment Efficiency (OEE).
What benefits are gained from synchronising breakdown management with the CMMS Maintenance Calendar?
Synchronising breakdown management with the maintenance calendar in CMMS provides numerous benefits for streamlined operations and improved maintenance strategies. This integration ensures immediate breakdown resolutions align with planned maintenance tasks, promoting a proactive approach that minimises equipment downtime and operational disruptions. By harmonising these processes, maintenance teams can identify recurring issues, implement preventive maintenance measures, and optimise resource allocation effectively. This synergy fosters a cohesive maintenance ecosystem, where insights from breakdown analytics inform the creation of a well-coordinated maintenance calendar, ultimately enhancing asset reliability, prolonging equipment lifespan, and elevating Overall Operational Efficiency.
How does CMMS utilise performance analytics to track breakdown frequency?
The CMMS harnesses the power of performance analytics to efficiently track breakdown frequency, enabling a comprehensive understanding of equipment reliability. The CMMS uncovers patterns and trends that shed light on recurring breakdown incidents by systematically analysing historical data. This invaluable insight empowers maintenance teams to proactively address underlying issues, implement targeted preventive measures, and ultimately reduce downtime. The CMMS enables organisations to optimise equipment performance, increase operational efficiency, and promote a proactive maintenance culture through precise breakdown monitoring.
Can you assess the performance of the maintenance team with CMMS insights?
Leveraging the advanced capabilities of our CMMS, you can seamlessly assess and elevate the performance of your maintenance team through valuable insights. By analysing data gathered from breakdown management, you gain a comprehensive understanding of key metrics such as response times, downtime duration, and frequency of incidents. These CMMS insights empower you to identify patterns, allocate resources more effectively, and implement targeted training initiatives. With the ability to evaluate the team's efficiency and make data-driven adjustments, you can drive continuous improvement, enhance equipment reliability, and ensure that your maintenance operations operate at peak performance.
In what ways does the CMMS empower technicians to report breakdowns?
The CMMS empowers technicians to swiftly and effectively report breakdowns through a user-friendly interface, enhancing their ability to communicate and initiate timely resolutions. With intuitive mobile accessibility, technicians can conveniently input critical information about equipment failures directly from the shop floor, ensuring accurate incident reporting. This streamlined process reduces downtime and integrates seamlessly with performance analytics, allowing maintenance teams to track breakdown frequency, response times, and other key maintenance metrics. By utilising the power of the CMMS, technicians can proactively address breakdowns, optimising equipment reliability and Overall Operational Efficiency.
How does the CMMS streamline communication?
The CMMS revolutionises communication within your maintenance operations by providing a seamless platform for collaboration and information sharing. CMMS ensures that maintenance teams, supervisors, and stakeholders remain interconnected and well-informed through real-time updates, instant notifications, and centralised documentation. The CMMS enhances operational efficiency and promotes proactive decision-making by facilitating transparent communication channels, task assignments, and progress tracking. This streamlined communication empowers your team to swiftly address breakdowns, allocate resources effectively, and maintain a synchronised approach to maintenance activities, ultimately leading to optimised equipment performance and minimising downtime.
Can the CMMS automate escalation procedures for unresolved breakdowns?
CMMS goes beyond just managing breakdowns; it empowers your maintenance operations with advanced automation. With the ability to automate escalation procedures for unresolved breakdowns, you can rest assured that critical issues receive the attention they deserve. When a breakdown remains unresolved, CMMS software automatically triggers predefined escalation protocols, ensuring the right personnel are alerted and engaged to address the situation swiftly. This feature minimises downtime, enhances your team's responsiveness, and ensures no breakdown goes unnoticed or unattended. CMMS takes proactive steps to keep your operations running smoothly, even in challenging situations.
How does CMMS facilitate Root Cause Analysis (RCA) to identify patterns and trends in equipment failures?
The CMMS (Computerised Maintenance Management System) plays a prominent role in enabling effective Root Cause Analysis (RCA) to identify recurring patterns and trends in equipment failures. The CMMS provides a rich repository for in-depth investigation by capturing comprehensive data on breakdown incidents. Through advanced analytics and reporting functionalities, maintenance teams can delve into historical breakdown data, pinpoint commonalities, and uncover underlying factors contributing to failures. This systematic approach empowers businesses to implement targeted corrective actions, proactively address root causes, and elevate equipment reliability. With the CMMS as a robust tool for RCA, organisations can fine-tune maintenance strategies, minimise downtime, and optimise Overall Equipment Efficiency (OEE) .
What mechanisms does the breakdown management feature offer for real-time notifications and alerts?
The breakdown management feature within CMMS introduces a robust framework for real-time notifications and alerts, ensuring swift and proactive responses to equipment failures. Through seamless integration of advanced alert mechanisms, this feature promptly notifies designated personnel and stakeholders when breakdown incidents are reported. These notifications encompass a range of customisable parameters, including priority levels, asset identification, and specific technical details. With real-time alerts, maintenance teams can rapidly mobilise, assess the situation, and initiate timely repairs, ultimately minimising downtime and maximising operational efficiency. This proactive approach prevents prolonged disruptions and empowers businesses to maintain peak equipment performance, safeguarding their production processes.
What documentation and attachments can be associated with breakdown reports to facilitate efficient repairs?
The breakdown management feature in CMMS allows you to associate various documentation and attachments with breakdown reports, facilitating a streamlined and efficient repair process. Attach relevant documents, such as equipment manuals, schematics, or troubleshooting guides, to provide technicians with essential resources at their fingertips. Images and photos can be added to visually highlight the issue, aiding in accurate diagnosis and swift resolution. Furthermore, you can include notes, observations, and repair history records, creating a comprehensive reference for current and future maintenance efforts. This documentation-rich approach ensures that your maintenance teams have all the information they need to address breakdowns effectively, minimising downtime and optimising equipment performance.
How does the breakdown management feature contribute to improving Overall Equipment Reliability?
CMMS ecosystem includes a breakdown management feature that prevents the recurrence of similar issues by promptly identifying, addressing, and analysing breakdown incidents. Root cause analysis reveals underlying factors contributing to breakdowns, enabling informed decision-making for targeted preventive actions. This proactive approach reduces downtime, enhances equipment longevity, and minimises operational disruptions. By integrating breakdown resolutions with scheduled maintenance tasks, the feature ensures a coordinated approach to upkeep, ultimately elevating the reliability of critical assets and optimising the efficiency of your maintenance operations.
How can the integration of CMMS with other inventory systems ensure the availability of spare parts for repairs?
The seamless integration of CMMS software with other inventory systems ensures the availability of crucial spare parts for efficient and timely equipment repairs. The CMMS enables real-time tracking of spare part stock levels, usage patterns, and procurement schedules by establishing a cohesive connection between these systems. When a breakdown occurs, the CMMS automatically cross-references the required spare parts against the inventory database, promptly identifying their availability. This integration streamlines the procurement process, triggering automatic alerts for replenishment or purchase orders when stock levels are low. Ultimately, this synergy between CMMS and inventory systems eliminates delays in acquiring necessary components, minimising downtime, and expediting repairs to optimise Overall Operational Efficiency (OOE) and equipment reliability.
Can CMMS collaborate with multiple users on data capture tasks simultaneously?
Within a comprehensive CMMS solution, multiple users' ability to collaborate seamlessly enhances efficiency and accuracy by enabling various team members to contribute, review, and update information in real-time. This feature encourages teamwork and keeps records of operational activities, including equipment maintenance data, inspection results, and breakdown incidents. As maintenance teams work in tandem to capture essential data, the CMMS fosters a collaborative environment that promotes effective decision-making, streamlines processes, and enhances overall productivity.
How can I customise the CMMS software to match my specific data collection needs?
Customising a CMMS solution to align with your distinct data collection requirements ensures seamless integration with your existing processes. This flexibility empowers you to tailor fields, forms, and workflows to match your shop floor operations precisely. By incorporating your specific terminology, data points, and reporting structures, the CMMS becomes a tailored tool, optimising data collection efficiency, accuracy, and analysis. This adaptable approach ensures that your CMMS solution enhances data management and becomes a genuinely cohesive extension of your operational framework.
Is there a way to track and audit user actions and changes made to the captured data in CMMS?
CMMS solutions facilitate tracking and auditing user actions and alterations to captured data, assuring data integrity and accountability. Having the ability to monitor changes made by users throughout the data lifecycle fosters transparency and compliance with regulatory standards. This feature empowers administrators to maintain a comprehensive audit trail, facilitating the identification of discrepancies, user-specific modifications, and historical data revisions. CMMS solutions provide an audit mechanism to maintain accurate and reliable data records and support decision-making processes. This reinforces a culture of efficient data management across various industries.
How does the CMMS software handle data validation and ensure the accuracy of captured information?
Data validation is a fundamental aspect of any robust CMMS solution, ensuring the integrity and reliability of captured information. The software employs a range of validation mechanisms to authenticate the accuracy of data input into the system. Through predefined rules, formats, and logical checks, the CMMS verifies that the entered data aligns with established parameters, eliminating errors and inconsistencies. This meticulous validation process not only upholds the quality of data but also enhances the overall effectiveness of the CMMS by enabling users to base their decisions on trustworthy and precise information.