What is Condition-Based Maintenance?
Condition-based Maintenance (CBM) is a proactive maintenance strategy that uses real-time data from sensors and monitoring devices to assess the condition of equipment. By analysing this data, organisations can identify signs of wear, malfunction, or inefficiency, allowing for timely maintenance interventions before failures occur.
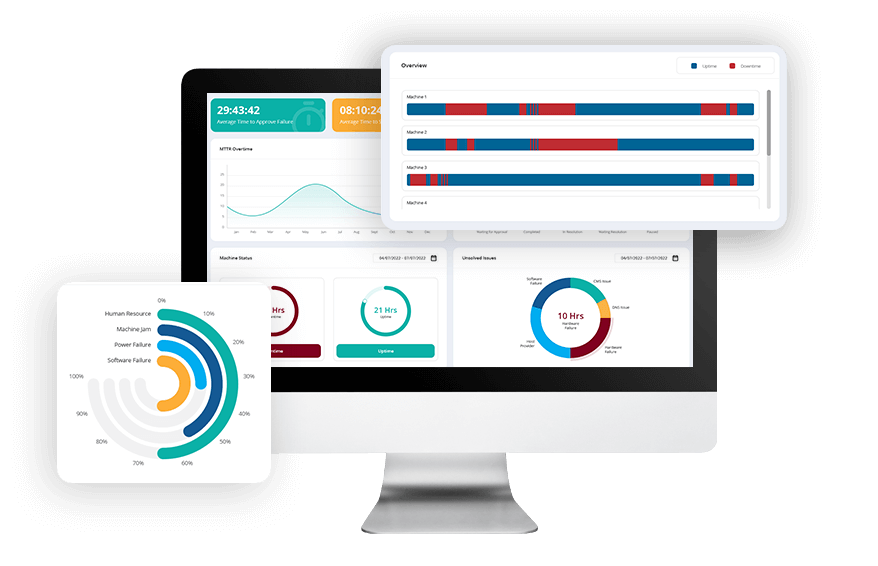
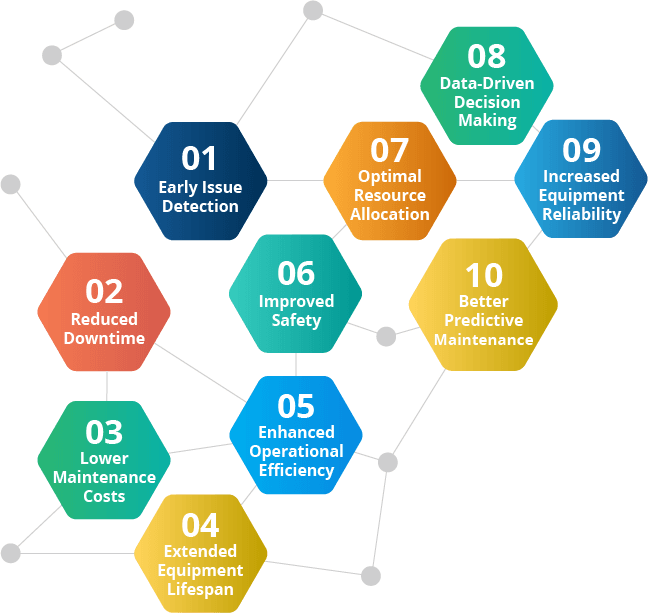
Benefits of implementing Condition-Based Maintenance
There are several advantages to implementing Condition-Based Maintenance in your industry.
- Early Issue Detection
- Reduced Downtime
- Lower Maintenance Costs
- Extended Equipment Lifespan
- Enhanced Operational Efficiency
- Improved Safety
- Optimal Resource Allocation
- Data-Driven Decision Making
- Increased Equipment Reliability
- Better Predictive Maintenance
Where is Condition-Based Monitoring used?
Condition-Based Maintenance (CBM) is employed in factories when continuous monitoring of equipment is essential to prevent unexpected breakdowns and optimise operational efficiency. Skilled maintenance technicians, engineers, and data analysts are typically involved in performing CBM tasks. They utilise sensors, IoT devices, and data analysis tools to monitor machinery and collect real-time data on several parameters and performance metrics. By analysing this data, they can detect early signs of wear, misalignment, or other issues. Regular analysis of equipment conditions allows for proactive maintenance interventions, ensuring the smooth functioning of machinery and minimising costly disruptions in the production process.
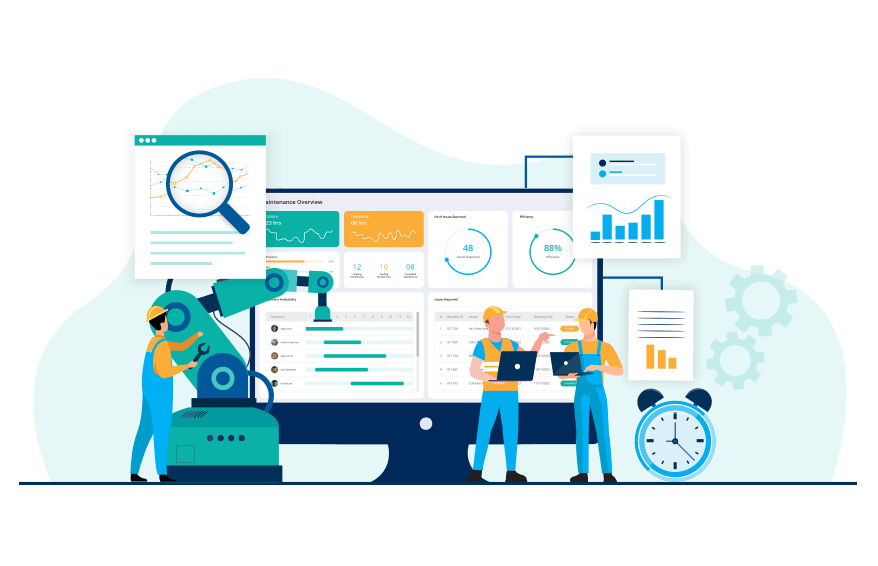
The P-F curve and Condition-Based Maintenance
The P-F curve is a critical concept in Condition-based Maintenance (CBM), representing the time interval between the detection of a Potential issue (P) and the Point of Failure (F) in equipment. CBM utilises this interval to optimise maintenance practices, aiming to perform interventions during this window to prevent failures and extend the equipment's lifespan. By closely monitoring equipment and identifying signs of deterioration within the P-F interval, CBM enables timely and proactive maintenance, ensuring operational efficiency and minimising costly downtime.
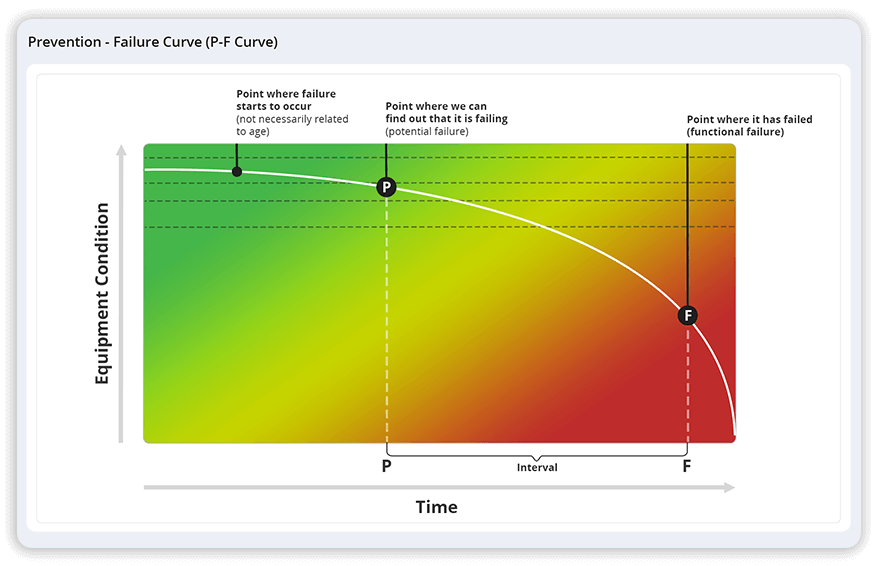
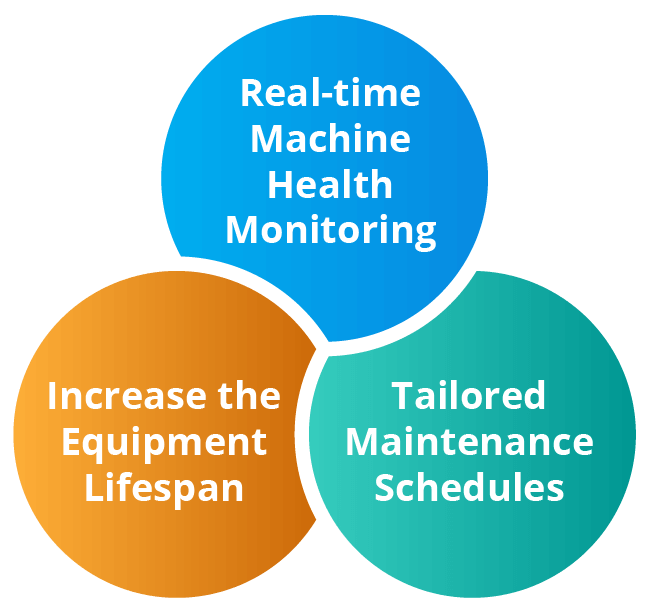
Why should you implement Condition-Based maintenance?
- Real-time Machine Health Monitoring
Utilise sensors and monitoring devices to continuously collect data from shop floor equipment. Employs data analysis to gain valuable insights into equipment health. Implement maintenance strategies by predicting equipment failures. - Increase the Equipment Lifespan
Address issues as soon as they are detected. Prevent unexpected breakdowns and minimise downtime. Reduce unnecessary maintenance activities and associated costs. - Tailored Maintenance Schedules
Customised maintenance plans designed for individual assets, ensuring precise and efficient upkeep. Ensure efficient use of resources and minimise disruptions to operations.
Trigger Condition-based Alarms
Integrate CMMS with monitoring sensors and generate alerts and alarms based on predefined thresholds. Notify maintenance teams when equipment parameters deviate from normal operations. Enable quick corrective actions, minimising downtime and preventing potential issues from escalating. Facilitate a proactive approach to maintenance, ensuring seamless and uninterrupted organisational operations.
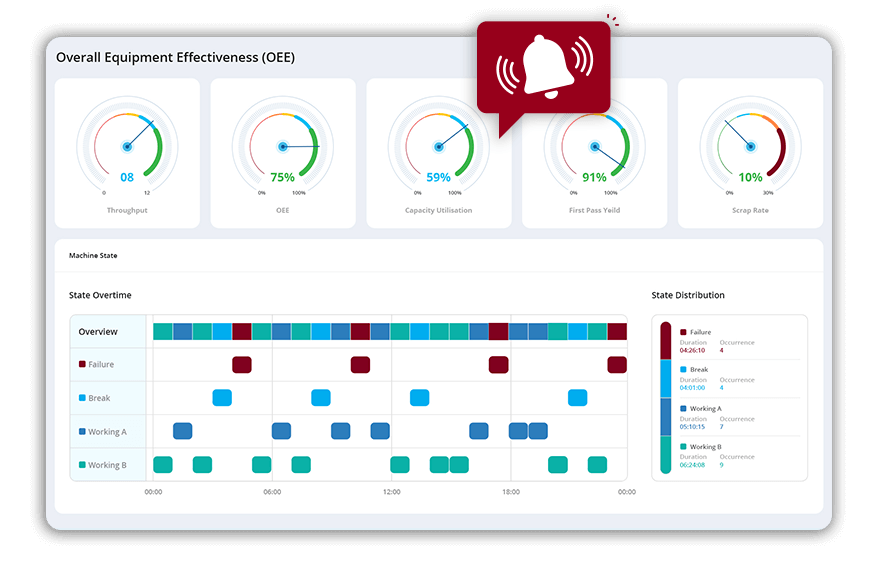
Contents
- What is the main goal of Condition-Based Maintenance?
- How does Condition-Based Maintenance work?
- Example of Condition-Based Maintenance
- Types of Condition-Based Monitoring
- Various Condition-Based Monitoring Techniques used in industries
- How to make Condition-Based Maintenance more effective?
- The Condition-Based Maintenance (CBM) workflow
- How to create a Condition-Based Maintenance program?
- Is Condition-Based Maintenance a Preventive Maintenance Strategy?
- How can I check if Condition-Based Maintenance works for my organisation?
- How frequently should Condition Monitoring be performed for effective Condition-Based Maintenance?
- 5 basic tips for Implementing Maintenance using Condition Monitoring
- How can businesses maximise their Return on Investment (ROI) by implementing Condition-Based Maintenance?
What is the main goal of Condition-Based Maintenance?
The goal of Condition-Based Maintenance (CBM) is to maximise equipment reliability and minimise downtime by monitoring real-time data to identify potential issues before they lead to failures.CBM optimises maintenance schedules, reduces downtime, and lowers costs by enabling targeted repairs based on the actual condition of assets. This approach enhances equipment reliability, prolongs lifespan, and ensures efficient operations, making it a crucial technique for various industries.
At the core of Condition-Based Maintenance lies the fundamental principle that the early stages of machine deterioration can be identified by closely monitoring and assessing trends in various parameters, a practice commonly known as condition monitoring. The four key pillars of condition monitoring, which are detection, diagnosis, prognosis, and program, guide the direct implementation of this monitoring approach.
The Key Components or Elements of Condition-Based Maintenance include:
- Sensors and Monitoring Devices: Utilised to collect real-time data on equipment parameters such as temperature, vibration, and performance metrics, providing crucial insights into the machinery's condition.
- Data Analysis Tools: Advanced algorithms and data analytics software process the collected data, identifying patterns, anomalies, and trends. These tools enable accurate assessment and prediction of equipment health.
- Alert Systems: Set predefined thresholds in the data analysis tools to trigger alerts when equipment parameters deviate from the norm. Alerts ensure timely notifications, allowing for proactive maintenance actions.
- Skilled Personnel: Trained technicians and engineers proficient in interpreting data and taking appropriate actions based on the analysis. Qualified personnel are essential for effective implementation and decision-making in CBM strategies.
- Predictive Algorithms: Employ predictive algorithms to forecast potential failures and performance trends based on historical and real-time data. Predictive capabilities enable proactive interventions, preventing costly breakdowns.
How does Condition-Based Maintenance work?
CBM ensures maintenance activities are performed precisely when needed, reducing unplanned downtime and associated costs while improving overall operational efficiency through its proactive and data-driven approach.
- Continuous Sensor Monitoring for Data Collection: Unlike Time-Based Maintenance, CBM relies on sensors which continuously collect real-time data, including temperature, vibration, and performance metrics, from equipment.
- Predictive Algorithm Analysis of the data collected: Advanced algorithms and data analysis tools process the collected data, identifying patterns and anomalies that might indicate equipment issues.
- Generating Threshold-Based Alerts: Thresholds are established for various parameters. When data deviates beyond these thresholds, the system triggers alerts, notifying maintenance teams in real time.
- Comparative Condition Assessment of the Equipment Conditions: CBM compares the current condition of equipment with predefined thresholds, allowing for the detection of early signs of wear or malfunction.
- Implementing Proactive Maintenance: When deviations are identified, maintenance interventions are triggered promptly, enabling timely repairs or replacements before significant failures occur.
Example of Condition-Based Maintenance
Condition-Based Maintenance (CBM) is a versatile approach that finds application across diverse industries, including Manufacturing, Automotive, Healthcare, Plant hire, Energy, Food & Beverages, Marine Vessels, Construction, Aerospace, Oil & gas, Government, Transportation and many others. In these sectors, CBM operates as a proactive strategy, ensuring the seamless functioning of critical equipment and machinery.
Let's take a closer look at a real-world application of Condition-Based Maintenance within an Automotive industry.
In a Car manufacturing industry, a critical robotic arm responsible for welding car components starts showing irregular vibrations detected through sensors. These vibrations indicate a potential misalignment or wear in the arm's components. Condition- Based Maintenance takes the following actions to solve this problem.
- Continuous Monitoring: CBM strategy uses IoT sensors to continuously monitor machine health and identify deviations, such as excessive vibrations.
- Alert System: When vibrations exceed predefined thresholds, an alert is triggered, notifying the maintenance team.
- Targeted Inspection: The maintenance team conducts a focused inspection of the robotic arm based on the alert.
- Identified Issue: Inspection reveals a worn-out bearing as the cause of the vibrations.
- Proactive Intervention: Instead of waiting for scheduled maintenance, the team immediately replaces the worn bearing.
- Preventing Breakdown: This proactive approach prevents potential breakdowns during production, avoiding costly delays.
- Enhanced Efficiency: By employing CBM, the automotive industry optimises maintenance, reduces operational disruptions, and ultimately enhances productivity and cost-efficiency.
Types of Condition-Based Monitoring
Condition-Based Monitoring (CBM) encompasses various techniques, including Internal Monitoring (Spot Testing) and Continuous Monitoring (Sensor Alerts), both of which play crucial roles in equipment maintenance.
- Internal Monitoring (Spot Testing)
Spot testing involves periodic assessments of equipment using manual inspection techniques. Maintenance technicians conduct targeted examinations at specific intervals to identify potential issues. This method is particularly useful for certain components that don't require constant monitoring. - Continuous Monitoring (Sensor Alerts)
Continuous monitoring or Sensor monitoring relies on sensors and data analysis tools to track equipment parameters in real-time. Sensors detect anomalies and trigger alerts when parameters deviate from the norm, allowing for immediate intervention and preventive actions. Continuous monitoring is vital for critical machinery where real-time data is essential. - Sensor Monitoring Techniques
- Mechanical Faults: Sensors detect variations in vibration patterns, allowing early identification of mechanical issues like misalignments or imbalances.
- Electrical Faults: Monitoring electrical parameters such as voltage, current, and resistance helps detect faults like short circuits or insulation breakdowns.
- Slow-Rotating Machinery: Sensors monitor slow-rotating components, ensuring they operate within the specified parameters to prevent wear and tear.
- Noisy or Vibrating Machinery: Sensors pick up unusual noises or vibrations, indicating potential problems in bearings, gears, or other moving parts.
Various Condition-Based Monitoring Techniques used in industries
- Vibration Analysis: Monitors equipment vibrations to detect imbalances, misalignments, or wear in rotating machinery. Unusual vibrations indicate potential issues, prompting timely maintenance.
- Oil Analysis: Examines lubricating oils to identify contaminants, wear particles, or chemical changes. Analysing oil samples helps evaluate the condition of gears, bearings, and hydraulic systems, guiding maintenance actions.
- Thermography (Infrared Imaging): Uses thermal cameras to identify abnormal heat patterns in electrical components or mechanical parts. Hotspots indicate potential faults, allowing preemptive repairs before failures occur.
- Ultrasonic Monitoring: Listens to ultrasonic emissions from equipment to detect leaks, electrical discharges, or bearing issues. Anomalies in ultrasonic signals indicate potential failures, enabling timely repairs.
- Motor Current Signature Analysis (MCSA): Focuses on motor currents to detect abnormalities such as rotor imbalances or mechanical issues. MCSA helps in diagnosing problems in electric motors, ensuring their smooth operation.
- Radiography: Utilises X-rays or gamma rays to inspect internal structures of components, revealing hidden flaws or defects, especially in welds and castings.
- Laser Interferometry: Measures tiny displacements with laser beams, aiding in precision alignment checks, vibration analysis, and detecting minute surface deformations.
- Electrical Monitoring: Involves tracking electrical parameters like voltage, current, and resistance to identify faults, short circuits, or irregularities, ensuring electrical system integrity.
- Electromagnetic Measurement (Eddy-Current Testing - ECT): ECT employs electromagnetic fields to detect surface cracks, variations in material conductivity, or thickness changes in conductive materials, making it valuable for non-destructive testing.
How to make Condition-Based Maintenance more effective?
- Implement Comprehensive Sensor Networks: Deploy a wide array of sensors across equipment to capture diverse data points, enabling a holistic view of machine health and allowing for early anomaly detection.
- Utilise Advanced Data Analytics: Utilise machine learning and predictive analytics to process data, identifying patterns and enhancing prediction accuracy.
- Establish Clear Thresholds and Alerts: Set precise parameters and alert thresholds based on historical data and equipment specifications. Well-defined thresholds ensure timely alerts for deviations, allowing proactive maintenance actions.
- Integrate with Maintenance Management Systems: Seamlessly integrate Condition-Based Maintenance data with Computerised Maintenance Management Systems (CMMS) to streamline work order generation, maintenance scheduling, and resource allocation for swift responses.
- Regularly Update Maintenance Protocols: Continuously refine maintenance procedures based on data-driven insights. Regularly updating protocols ensures that the maintenance team is equipped to address evolving equipment needs effectively.
- Train Personnel Effectively: Provide comprehensive training to maintenance technicians and engineers on utilising CBM tools, interpreting data, and taking appropriate actions. Well-trained personnel are essential for maximising the effectiveness of CBM initiatives.
- Implement Predictive Maintenance: Move beyond reactive strategies by embracing predictive maintenance. Predictive algorithms forecast potential failures, allowing for timely interventions and minimising disruptions to operations.
- Focus on Root Cause Analysis: Investigate the underlying causes of identified issues rather than just addressing symptoms. Understanding root causes helps implement preventive measures, reducing recurrent problems and enhancing overall effectiveness.
The Condition-Based Maintenance (CBM) workflow
- Real-time Equipment Data Collection: Sensors continuously gather live data on various equipment parameters, ensuring a constant flow of information regarding the machinery's performance and health.
- Data is Transmitted for Analysis: Collected data is swiftly transmitted to the Computerised Maintenance Management System (CMMS) for facilitating in-depth assessments and predictive analysis to identify patterns, trends, and potential issues.
- Processing Transmitted Data using CMMS: The transmitted data is processed using Computerised Maintenance Management System (CMMS) software, where advanced algorithms and tools analyse the information, offering valuable insights into equipment conditions to generate alerts.
- Triggering Alerts based on Deviations: Deviations from established norms prompt automatic alerts, signalling potential concerns. These alerts serve as early warnings, ensuring immediate attention and preventive measures.
- Skilled Technicians Identifies Root Causes: Proficient technicians analyse the data to identify underlying causes of anomalies, distinguishing between symptoms and potential equipment failures. Their expertise ensures accurate diagnosis.
- Maintenance Team Makes Informed Decisions: Informed by data analysis, the maintenance team makes strategic decisions, considering factors like equipment health, historical performance, and predictive insights. These decisions guide the maintenance approach.
- Maintenance Interventions are Executed: Proactive interventions, based on data-driven decisions, are promptly executed. These interventions include targeted repairs, adjustments, or replacements, preventing potential breakdowns and ensuring seamless operations.
- Data Management in the CMMS: The Post-Maintenance monitoring data is fed back to CMMS to manage and enrich the database, enhancing the system's predictive capabilities and refining future maintenance strategies for ongoing improvement.
How to create a Condition-Based Maintenance program?
Let's discuss the 6 Steps to start implementing a Condition-Based maintenance plan in your industry.
- Assessment of Assets: Begin by identifying critical equipment or machines that are essential to your operations and are most susceptible to wear, damage, or failures. Any deviations from standard operating thresholds can be identified by IoT sensors attached to the equipment. The sensor data can be transmitted to CMMS for analysis.
- Sensor Selection and Installation: Choose appropriate sensors like heat monitoring sensors or acoustic emission analysing sensors, based on the parameters relevant to your equipment, such as temperature, vibration, or pressure. Install these sensors strategically on the identified components to collect real-time data.
- Implement CMMS: Implement advanced data analytics software such as CMMS (Computerised Maintenance Management System) for processing and interpreting the data collected by sensors. CMMS software can track asset performance, identify maintenance issues, and predict potential breakdowns.
- Threshold Setting and Alert Configuration: Define specific thresholds for each parameter monitored. When the data deviates beyond these thresholds, configure alert systems to notify maintenance teams in real-time. Alerts ensure timely interventions and prevent potential failures.
- Develop Maintenance Protocols: Develop detailed maintenance protocols for different types of maintenance needs. These protocols should include specific actions to be taken, responsible personnel, tools and resources required, and timelines for completion. Protocols can range from minor adjustments to complete overhauls, depending on the trigger severity.
- Training and Implementation: Train maintenance teams to analyse data, interpret alerts, and take appropriate actions. Implement the CBM plan across the identified assets, ensuring continuous monitoring and proactive maintenance interventions. Regularly review and refine the CBM strategy based on feedback and outcomes to enhance its effectiveness.
Is Condition-Based Maintenance a Preventive Maintenance Strategy?
Condition-Based Maintenance (CBM) is not a traditional preventive maintenance strategy. While preventive maintenance relies on fixed schedules for maintenance activities, CBM is proactive, focusing on real-time data and the actual condition of equipment. CBM utilises continuous monitoring and data analysis to trigger maintenance actions when deviations from normal parameters are detected, ensuring that maintenance is performed precisely when necessary, not at predetermined intervals.
How can I check if Condition-Based Maintenance works for my organisation?
To determine if Condition-Based Maintenance (CBM) is suitable for your organisation, start by assessing your equipment's complexity and criticality. Consider implementing CBM inspections using sensor data and predictive algorithms to monitor key parameters. Utilise a Condition-Based Maintenance checklist to guide inspections, ensuring a systematic evaluation of equipment health. Analyse the effectiveness of these inspections by evaluating the accuracy of predictions, reduction in downtime, and overall cost savings. If CBM interventions lead to proactive maintenance, minimised disruptions, and extended equipment lifespan, it indicates the approach benefits your organisation. Regularly reviewing the outcomes of CBM inspections and checklist utilisation will further affirm its suitability and effectiveness for your specific needs.
How frequently should Condition Monitoring be performed for effective Condition-Based Maintenance?
The frequency of condition monitoring depends on the criticality of the equipment, its usage patterns, and the manufacturer's recommendations. Some equipment might be monitored continuously, while others may require periodic assessments, ranging from daily to monthly, to ensure early detection of issues.
5 basic tips for Implementing Maintenance using Condition Monitoring
- Ensure clear communication: Foster open communication channels between teams to ensure everyone understands the goals, benefits, and processes associated with CBM implementation.
- Provide proper training: Invest in comprehensive training programs for technicians and staff involved in CBM to enhance their skills and understanding of the monitoring tools and data interpretation.
- Ensure data integration: Integrate CBM data seamlessly with existing systems, such as Computerised Maintenance Management Systems (CMMS), for streamlined workflows, efficient work order generation, and improved decision-making.
- Use high-quality sensors: Invest in high-quality sensors and monitoring equipment that are accurate and reliable. Choosing the right sensors is crucial for obtaining precise data and minimising false alerts.
- Implement regular system audits: Conduct periodic audits of the CBM system to identify potential gaps, update technologies, and ensure the system aligns with the evolving needs of the organisation.
How can businesses maximise their Return on Investment (ROI) by implementing Condition-Based Maintenance?
Businesses can optimise their Return on Investment (ROI) by adopting Condition-Based Maintenance (CBM), leveraging real-time sensor data to enhance operational efficiency. By proactively addressing equipment issues, CBM minimises downtime, reduces maintenance costs, and extends asset lifespan. This approach ensures targeted interventions, preventing costly breakdowns and unnecessary repairs. Ultimately, CBM maximises ROI by improving productivity, minimising disruptions, and reliability of critical assets, leading to significant cost savings and enhanced overall efficiency for businesses.