5 ways to improve the Health and Safety of your facility with a Maintenance Management Software
February 7, 2023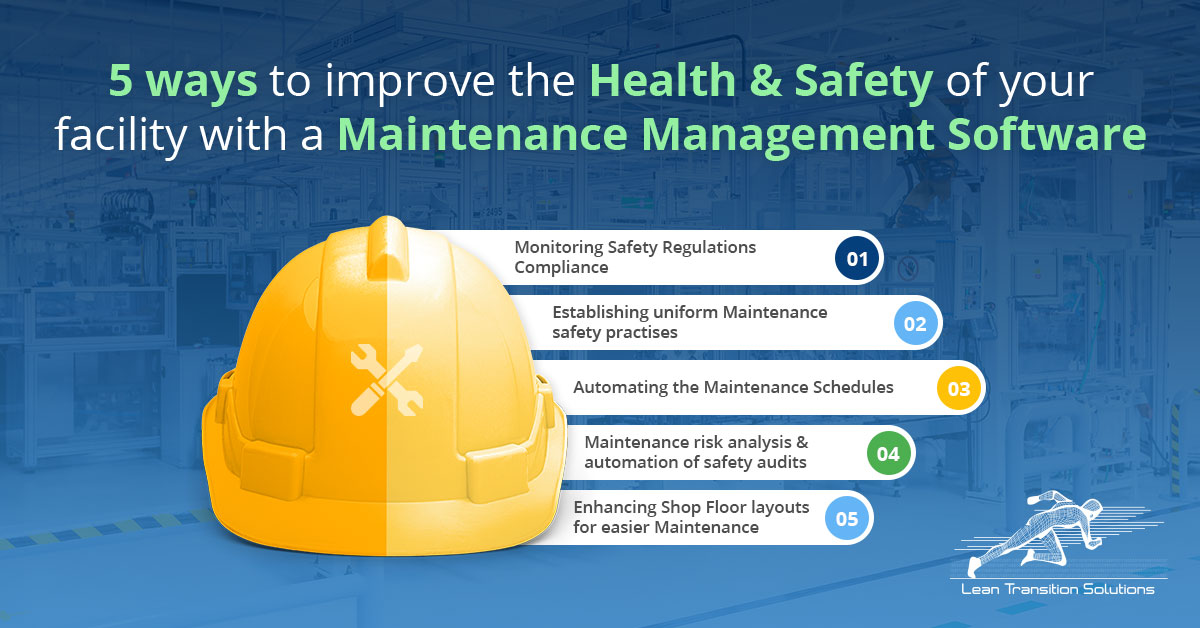
There is a very old saying that still rings true, prevention is better than cure. Even the smallest mishap can cause a profound impact on everything in your facility, your operations, or the people's lives.
The Health & Safety Act 1974, employers must be able to create and maintain a healthy and safe environment at the workplace. The possible hazards are expected to be identified and eliminated at the earliest rather than providing them with Personal Protective Equipment(PPE).
A proper maintenance strategy can help you prevent your efforts from going wasted. Breakdown maintenance is one good cause that can primarily contribute to these accidents. Always a better alternative is to have a preventive maintenance strategy, as the chances of having a casualty can be reduced by 50%.
An added responsibility, yet an essential one, right? Switching to a digital maintenance strategy will facilitate better maintenance plans that will be mindful of a safer and healthier working environment.
Monitoring Safety Regulations Compliance
Regular audits and inspections can help you ensure the safety standards defined by the statutory laws during operations. Be it governing the pollution levels or checking the security standards, establishing a proper maintenance plan is the base.
CMMS software collects and uses the data that safety professionals can use to monitor and improve a facility's adherence to environmental, health, and safety requirements. Maintenance teams can track all the necessary maintenance work to meet safety and compliance standards. Tasks for required inspection are incorporated into routine maintenance schedules by technicians. When these inspections are due, the systems produce warnings and distribute the assignments to the available technicians. The maintenance crew sends all safety reporting and inspection information to a centralised data management system for review and storage. Field technicians can report unfinished maintenance tasks, new safety issues, and insufficient inspection equipment and replacement parts.
Establishing uniform Maintenance safety practises
Each facility has different maintenance duties that range in size and complexity. Maintenance workers face daily dangers, including unprotected machinery, fires, dangerous pollutants, and electrical risks.
Maintenance workloads and exposure to these risks can be reduced with CMMS systems. Before beginning physical work, technicians must complete the checklists and sequential processes in the work instructions. Along with detailed maintenance guides that personnel can use to maintain assets, the system also stores typical technical documentation to track maintenance. Periodic assessment enables safety experts to create more efficient regulations. The CMMS software also makes it easier for safety personnel to update and distribute new safety data remotely and ensure that everyone is aware of the most current safety requirements for the organisation.
Automating the Maintenance Schedules
An improper maintenance schedule can cost you frequent asset failures and malfunctions that could cause operator injuries, the release of hazardous substances, or fires. Taking the right maintenance measure can solve this.
Asset maintenance history and data stored in the Computerised Maintenance Management System automates the maintenance schedules and allocate the tasks accordingly. Prioritisation and analysis of the maintenance schedules ensure that all assets receive the proper preventative and corrective actions and enough staff to carry out these activities by optimising maintenance schedules.
Maintenance risk analysis and automation of safety audits
The extent and nature of the dangers change according to the operations. Some may be persistent, while others might have caused due to poor work processes or bad condition of the assets. Whatever it might be, small or big, the technicians are required to report any safety-related occurrences.
A CMMS software system can assist in documenting and monitoring the safety risks throughout the plant. A detailed database of all plant maintenance hazards can also create applicable safety training programmes and automate safety audits. Safety audits, otherwise labour-intensive, can be done with the CMMS, which can help them swiftly assess the efficacy of incident-reporting systems. These technologies make it simpler for safety auditors to identify the origin, spread, and effects of various maintenance-related risks by using industry-standard safety reporting formats.
Enhancing Shop Floor layouts for easier Maintenance
Risks to maintenance safety are not limited to equipment and work procedures. A disorganised workplace or a poor design of the factory floor can also have the same impact. From providing the proper sign boards to safety warning signs, the shop floor has a role to play in this regard.
Uploading a facility layout with facility data using a CMMS solution ensures everyone is aware of the location of each asset and piece of safety gear. Specialists in workplace ergonomics can assess these layouts and identify safety hazards based on how the shop floor is set up. They can contrast the efficiency of various floor plans and how they affect the upkeep of assets. This ensures that the very improvement or addition in the factory floor does not disturb the balance between the safety guidelines and the operational efficiency.