11 ways CMMS help cut Maintenance Costs and boost Revenue
April 17, 2023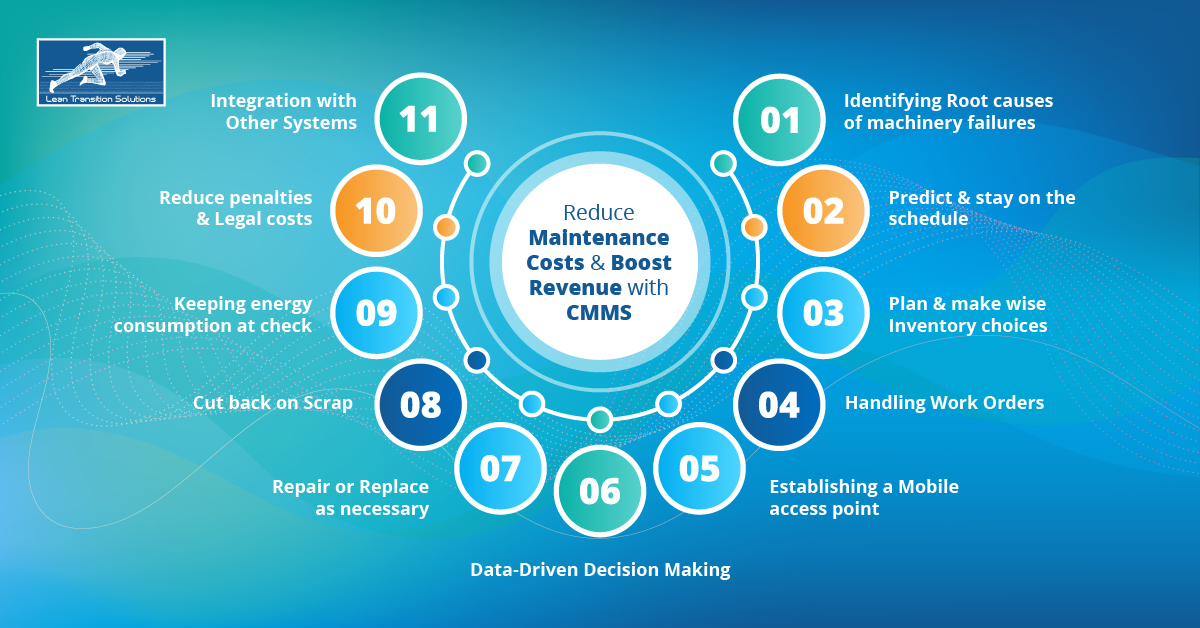
Maintenance is integral to any business, whether manufacturing, healthcare, hospitality, or any other industry. The optimal use of equipment can be achieved through proper asset management and maintenance. It is where maintenance software comes in handy. The Computerised Maintenance Management System (CMMS) is a software application designed to help companies streamline their maintenance processes, reduce downtime, and cut maintenance costs. The system is used to manage, monitor, and organise the maintenance processes of a company. CMMS is critical in managing assets and equipment, inventory, scheduling maintenance activities, and managing work orders.
Now let's discuss ways to cut maintenance costs and boost revenue with effective maintenance softwares like CMMS.
Identifying Root Causes of machinery failures
In order to prevent severe damage to equipment or facilities, preventive maintenance focuses on identifying and addressing potential issues. A Computerised Maintenance Management System (CMMS) allows businesses to schedule preventive maintenance activities based on equipment usage, performance, and condition. This approach helps maintenance by reducing unexpected downtime and costly repairs and extending the equipment's lifespan.
CMMS aids in regularly scheduled inspections, cleaning, lubrication, and other activities that help with Root Cause Analysis (RCA) and manage processes before they cause downtime. CMMS can create preventive maintenance schedules, set reminders for reviews and activities, and track maintenance history to maintain equipment properly. Preventive maintenance using CMMS reduces maintenance costs and boosts revenue for businesses.
Predict and stay on the Schedule
Predictive maintenance is a proactive maintenance strategy that monitors equipment performance in day-to-day operations to identify and prevent any possible failures. By analysing data such as vibration, temperature, and usage patterns, CMMS aids in Root Cause Analysis (RCA), allowing companies to take corrective action before equipment fails. Predictive maintenance can reduce downtime, increase equipment reliability, and cut maintenance costs. CMMS helps companies collect and analyse data, set up alerts for potential issues, and create maintenance schedules based on predicted failure rates.
Plan and make wise Inventory choices
Improper management of inventory can be time-consuming and costly. The system allows businesses to track inventory levels, reorder parts and equipment when necessary, and manage the supply chain. Using CMMS, businesses can avoid overstocking, reduce inventory carrying costs, and prevent stock-outs, leading to expensive downtime. Businesses can increase revenue and reduce costs by optimising inventory management using CMMS.
Handling Work Orders
Work order management involves creating work orders, assigning tasks to technicians, and tracking progress. Work order management can be complex and time-consuming, but with maintenance software like CMMS, companies can automate much of the process. CMMS simplifies work order management by allowing businesses to schedule maintenance tasks, track work orders, and manage resources effectively. The system will enable technicians to receive notifications of work orders and update them in real-time. CMMS also provides insights into work order performance and helps businesses optimise resources and reduce downtime. CMMS helps businesses reduce costs and improve efficiency by streamlining the work order management process.
Establishing a Mobile Access point
CMMS provides businesses with remote access and mobile capabilities, allowing technicians to access maintenance information and complete work orders using mobile devices. This capability improves communication, reduces paperwork, and streamlines maintenance activities. Technicians can access maintenance data in real-time, hence helping them in making more informed decisions and respond to issues quickly. CMMS helps businesses reduce response times to maintenance issues, improve technician productivity, and minimise downtime.
Data-Driven Decision making
CMMS can generate reports and analytics on maintenance activities, equipment performance, and other metrics. These reports can help companies identify trends, track equipment performance, track Key Performance Indicators (KPIs), and make data-driven decisions about maintenance activities. Analysis of equipment performance, maintenance activities, and inventory data can help businesses identify inefficiencies, optimise resources, and reduce maintenance costs. CMMS also allows companies to track KPIs such as maintenance costs, work order completion rates, and equipment downtime. Analytics and reporting in businesses can help organisations to make informed decisions to cut down expenses.
Repair or Replace as necessary
CMMS helps businesses manage their assets and equipment by providing real-time visibility into their performance, utilisation, and maintenance needs. Data collected from equipment maintenance can help businesses plan maintenance and replacements, allocate resources effectively, and minimise downtime. CMMS also gives businesses insights into the total cost of ownership of their equipment and assets. Businesses can reduce maintenance costs, extend asset lifespans, and increase revenue by managing assets and equipment effectively. Mean Time To Repair (MTTR), for instance, provides data on the average time gap between recent repairs, supporting maintenance teams in making wise purchases.
Cut back on Scrap
When production systems fail, rework and scrap occur. It can lead to delays in product delivery, lower customer satisfaction and decreased profits. A reliable manufacturing system must be in place to reduce these losses. CMMS can identify potential sources of failure before they occur, allowing maintenance teams to take proactive measures. These measures can reduce the cost of rework and hence manage scrap, and also improve the efficiency of the workplace. CMMS systems also provide insight into maintenance and production trends, enabling teams to identify areas of improvement and increase efficiency.
Keeping Energy Consumption at check
Organisations may get real-time data on their energy usage with a CMMS. By analysing this data, businesses can see trends and areas for improvement, which helps guide strategic decisions on minimising energy usage. When equipment efficiency decreases, it leads to increased energy consumption. Poor lubrication and worn parts generate heat, increase friction, and need more power. CMMS uses Condition-based predictive maintenance that prevents machines from using additional energy, thus reducing energy consumption expenses.
Reduce Penalties and Legal Costs
Compliance management is critical for businesses operating in regulated industries. CMMS allows businesses to manage compliance requirements and documentation, such as inspection reports and maintenance logs. CMMS can help organisations comply with regulations, reducing penalties, and minimising legal costs. Compliance management using CMMS can help businesses avoid costly penalties and legal costs, boosting their revenue.
Integration with Other Systems
CMMS can integrate with other systems, such as Enterprise Resource Planning (ERP) and other Asset Management systems. This integration can help companies streamline maintenance processes, reduce paperwork, and improve communication between departments. Integrating CMMS with ERP systems can automate inventory management and purchasing processes. While integrating CMMS with asset management systems can help improve equipment tracking and maintenance activities. With maintenance software integration, companies can improve maintenance efficiency and maximise revenue generation.
When preventive maintenance is implemented, inventory management is optimised, work orders are streamlined, and assets are managed, businesses can achieve significant revenue growth. CMMS also eliminates paperwork and time-consuming tasks, allowing employees to concentrate on more critical initiatives and increasing their productivity and responsiveness. It is essential to choose the right CMMS software for your business needs. Continuous evaluation and optimisation ensure that the CMMS software works effectively and efficiently. Maintenance teams use a CMMS to organise information, ensure work is finished, and evaluate the results of that work in industrial, asset-intensive organisations. CMMS helps increase machine uptime, resulting in fewer delays and disruptions to production. It also helps businesses track and forecast maintenance costs, enabling them to plan and budget accordingly. Finally, it helps businesses reduce equipment failure risk and ensures better safety regulations compliance. By implementing CMMS, businesses can optimise their maintenance processes, reduce costs, and increase revenue, which helps them stay competitive.