How can TPM work in Industry 4.0 environment?
March 24, 2022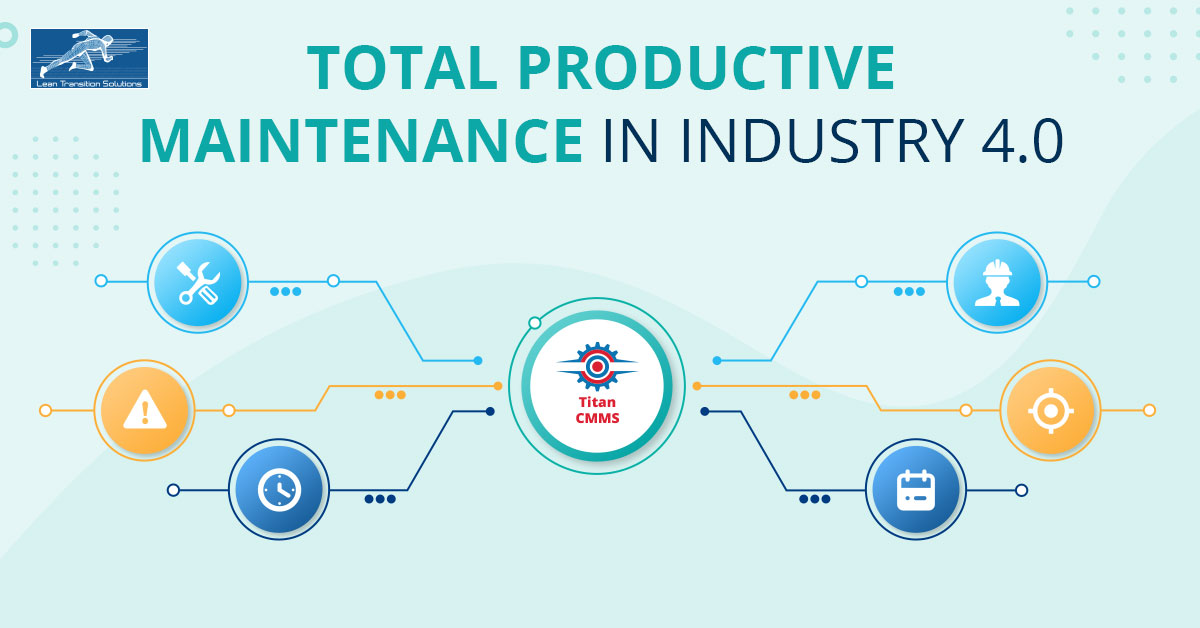
As we know, Industry 4.0 is all about integrating current technological trends such as the combination of cyber-physical systems, Internet of systems and Internet of Things in manufacturing. Though the previous revolution promoted the implementation of computers in manufacturing, this transition is more about the smart interrelation of systems, their communication and the ability to make decisions without human intervention. Industry 4.0 alters the current mechanism of manufacturing and its services. A question that the manufacturers ask is whether they should commit to this revolution considering the investment and its outcomes.
How does Industry 4.0 influence lean?
Manufacturers and operators have followed the concept of lean to improve outcomes and decrease complexity. Lean is always about achieving the maximum output with the minimum input. People are the building blocks of lean and not gadgets; hence Industry 4.0 will be a part of lean. Lean principles will enable a smooth transition and makes an organisation smart. Studies suggest that Industry 4.0 technologies are exactly what we need to create a lean supply chain and networks. The digitisation of machinery directs toward the automation of lean and can be achieved with the current technological innovations. The foundational principles will not be affected while new add-ons such as data collection, better communication mechanisms, process tracking & management are made, but will give the current methodologies a new face. This is the most effective way to reach the utmost level of operational excellence.
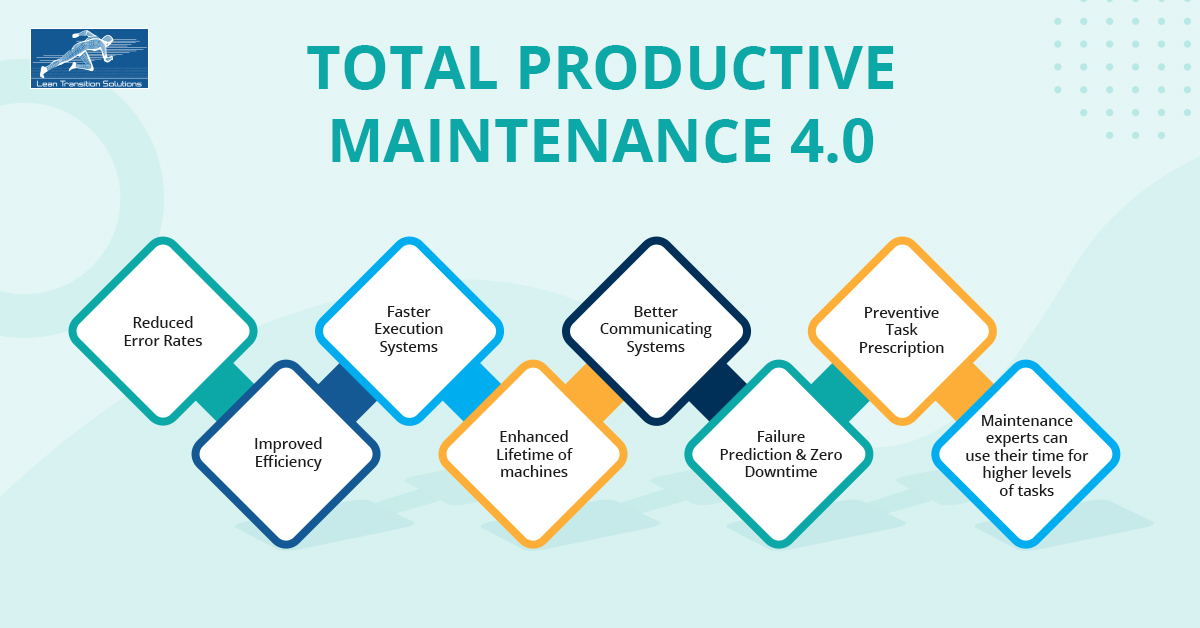
Total Productive Maintenance in Industry 4.0.
As we know, CMMS is a software used to achieve Total Productive Maintenance and Overall Equipment Efficiency. The next-generation maintenance systems are all about digital transformations such as advanced robotics, adaptive manufacturing, big data and analytics, augmented reality, cloud computing, horizontal and vertical system integration, cybersecurity, the industrial internet, and simulation. Computerised Maintenance Management Systems can be easily integrated with cyber-physical systems.
The integration of Industry 4.0 with lean makes it possible for the maintenance systems to connect to each other and transmit information to other systems across departments, locations etc. The data thus collected and analysed help professionals make decisions during real business-critical situations. The right analysis will enable the system to predict failure, reconfigure itself, and adapt to change. Operators can handle maintenance and unpredicted breakdowns well in such an atmosphere. Moreover, these digital systems do not require much human intervention and can be accessed anytime from anywhere. 4th level predictive maintenance will analyse big data by continuous real-time monitoring of assets that send alerts based on predictive techniques such as regression analysis.
How Industry 4.0 can improve Total Productive Maintenance (TPM)?
Reduced Error Rates
Improved Efficiency
Faster Execution Systems
Enhanced Lifetime of machines
Better Communicating Systems
Failure prediction and zero downtime
Maintenance experts can use their time for higher levels of tasks
Preventive task prescription
Industry 4.0 will not only optimise the equipment’s overall performance but also improves human and machine interaction. With Industry 4.0, manufacturers can boost the business output, help synchronise assets and facilitate self-managing factory operations.