11 Common causes of Equipment failure & ways to prevent them
July 5, 2023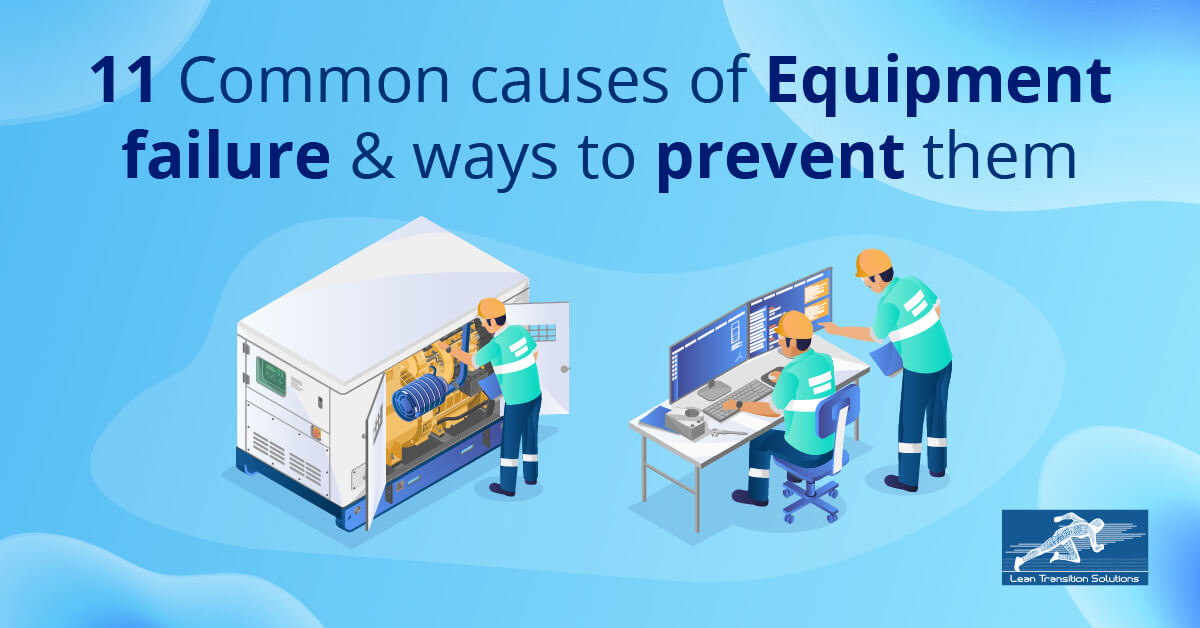
Equipment failure can be a major setback for any business, leading to downtime, increased costs, and potential safety hazards. Understanding the common causes of equipment failure and implementing preventive measures is essential to maintain operational efficiency and protect valuable assets. In this blog, we will explore 11 common causes of equipment failure and effective strategies to prevent them. By taking necessary precautions, businesses can minimise the risk of equipment failure, optimise productivity, and ensure smooth operations.
What is Equipment Failure?
Equipment failure refers to the malfunction, breakdown, or inability of machinery, tools, or devices to perform their intended function. It occurs when a part of equipment ceases to operate efficiently, disrupting the normal functioning of system operations. Equipment breakdown, mechanical failure, system outage, technical malfunction and equipment downtime are terms used instead of equipment failure.
These occurrences can result from wear and tear, lack of maintenance, component defects, power surges, software glitches, or environmental conditions. Effective maintenance practices, regular inspections, and prompt repairs are essential to prevent and mitigate equipment failures, ensuring smooth and uninterrupted functioning of critical systems.
Importance of addressing Equipment Breakdown
Equipment failure is a significant concern in various industries, as it can result in costly downtime, production delays, and safety hazards. Organisations rely on Computerised Maintenance Management Systems (CMMS) to effectively mitigate and address equipment failures. CMMS plays a vital role by streamlining maintenance processes, scheduling regular inspections and preventive maintenance, tracking equipment performance, and managing spare parts inventory.
By utilising CMMS, companies can proactively identify and address potential issues, reduce unplanned downtime, extend equipment lifespan, and optimise maintenance costs. Through real-time monitoring, data analysis, and predictive maintenance capabilities, CMMS empowers organisations to enhance equipment reliability, minimise failures, and ensure efficient operations.
Types of Equipment Failure which affects Operational Performance
1. Mechanical Failure
- Breakdown of moving parts: When the moving components of machinery or equipment fail, it can lead to unexpected stoppages, decreased productivity, and potential damage to other parts.
- Misalignments and Imbalances: Misalignments or imbalances in machinery can cause excessive wear and tear, reduced performance, increased energy consumption, and potential safety risks.
2. Electrical Failure
- Power surges and electrical issues: Power surges or electrical issues can damage sensitive equipment, disrupt operations, cause data loss, and pose safety hazards to workers.
- Circuit overload and short circuits: Circuit overloads or short circuits can result in equipment malfunctions, production interruptions, electrical fires, and costly repairs.
3. Software or Firmware Failure
- Bugs and Glitches: Software or firmware failures can lead to system crashes, errors, and malfunctions, impacting the accuracy, efficiency, and reliability of automated processes.
- Incompatibility issues and Data Corruption: Incompatibility issues or data corruption in software or firmware can hinder communication between equipment, cause data loss, compromise product quality, and disrupt shop floor operations.
Consequences of Equipment Failure
- Downtime and reduced Productivity: Equipment failure often results in downtime as repairs or replacements are needed. This leads to reduced productivity and delays in completing tasks or projects.
- Increased Costs for Repairs or Replacements: Repairing or replacing faulty equipment can be costly. The expenses may include the cost of replacements, hiring technicians or experts, or even purchasing new equipment altogether. These unexpected costs can strain a company's budget.
- Safety Hazards and Potential Accidents: Equipment failure can pose safety hazards to employees. Malfunctioning equipment may lead to accidents, injuries, or even fatalities. For example, if a machine fails to shut down properly or malfunctions during operation, it can cause harm to workers or damage to the surrounding environment.
- Negative impact on Customer Satisfaction and Business Reputation: When equipment failure disrupts operations or delays the delivery of products or services, it can result in dissatisfied customers. Unreliable equipment may lead to delays, poor quality output, or inconsistent performance, which can damage the reputation of a business. Negative word-of-mouth and reviews can impact future customer acquisition and retention.
11 Common Causes of Equipment Failure & ways to prevent them
In any industry, equipment failure can result in costly downtime, reduced productivity, and compromised efficiency. To minimise these risks, it is crucial to understand the common causes of equipment failure and implement preventive measures. By taking proactive steps and adopting effective maintenance strategies, businesses can enhance equipment performance, reduce downtime, and optimise overall operations. Let’s explore 11 common causes of equipment failure and how to prevent them.
- Lack of Preventive Maintenance: Failure to conduct regular Preventive Maintenance (PM) is one of the leading causes of equipment failure. Equipment may suffer from wear and tear without a structured maintenance schedule, leading to breakdowns and decreased performance. Implementing a preventive maintenance program ensures timely inspections, lubrication, calibration, and repair or replacement of worn-out parts, which can significantly reduce the risk of unexpected failures.
- Reactive Maintenance Approach: Relying solely on Reactive maintenance, also known as "Breakdown maintenance," is a risky strategy. Reactive maintenance involves addressing issues only after equipment failure occurs. This approach often leads to extended downtime, increased repair costs, and compromised product quality. By shifting towards proactive maintenance methods, such as preventive and predictive maintenance, businesses can identify and resolve potential problems before they escalate.
- Inadequate Inventory Management: Poor Inventory management can contribute to equipment failure. An insufficient stock of critical spare parts and components can delay repairs, extend downtime, and hinder production. Implementing an efficient inventory management system ensures the availability of necessary spare parts, minimising the impact of equipment failures and reducing repair time.
- Neglecting Asset Management: Lack of proper Asset management practices can result in equipment failure. Failing to track equipment usage, monitor performance, and assess lifespan can lead to premature failure and unnecessary downtime. Adopting asset management systems allows businesses to monitor equipment health, plan maintenance schedules, and optimise asset utilisation, extending equipment life and preventing failures.
- Ignoring Standard Operating Procedures (SOP): Deviation from established standard operating procedures (SOP) can significantly increase the risk of equipment failure. SOPs provide safe and effective equipment operation, maintenance, and troubleshooting guidelines. By strictly adhering to SOPs, employees can minimise errors, prevent accidents, and ensure equipment functions optimally.
- Inefficient Maintenance Downtime Management: Inefficient management of maintenance downtime can negatively impact production schedules and overall efficiency. Effective planning and coordination of maintenance activities are essential to minimise the duration of downtime. Implementing Scheduled maintenance and optimising the allocation of resources ensures that maintenance tasks are completed efficiently, reducing the impact on production.
- Lack of Predictive Maintenance (PdM): Failing to employ Predictive Maintenance techniques can lead to unexpected equipment failures. Predictive maintenance (PdM) utilises real-time monitoring, data analysis, and condition-based indicators to identify potential issues before they cause equipment breakdowns. By proactively detecting abnormalities, businesses can schedule maintenance activities during planned downtime and avoid costly unplanned downtime.
- Ignoring Failure Mode and Effects Analysis (FMEA): Neglecting Failure Mode and Effects Analysis (FMEA) can result in unforeseen equipment failures. FMEA involves analysing potential failure modes, their causes, and their impact on equipment performance. By conducting comprehensive FMEA analysis, businesses can identify critical failure modes, develop appropriate preventive measures, and reduce the likelihood of equipment failures.
- Neglecting Overall Equipment Effectiveness (OEE): Failure to monitor and optimise Overall Equipment Effectiveness (OEE) can lead to reduced productivity and increased downtime. OEE measures equipment performance, availability, and quality to identify areas for improvement. By regularly assessing OEE metrics and implementing targeted enhancements, businesses can increase equipment reliability, minimise downtime, and optimise operational efficiency.
- Lack of Condition-Based Maintenance: Condition-based maintenance involves monitoring equipment conditions through sensor data, performance indicators, and real-time monitoring systems. By analysing equipment health in real-time, organisations can identify signs of deterioration, schedule maintenance based on actual equipment condition, and avoid unnecessary downtime.
- Lack of Training and Skill Development: Insufficient training and skill development among maintenance personnel can contribute to equipment failure. Properly trained technicians are essential for effective Preventive Maintenance, timely repairs or replacement and accurate troubleshooting. Businesses can effectively implement Maintenance team management and reduce equipment failure risks by investing in training programs and providing ongoing skill development opportunities.
It is essential for organisations to proactively address failures by implementing preventive maintenance strategies, utilising advanced monitoring systems, and employing robust maintenance management solutions like CMMS to minimise the impacts of equipment failures and ensure smooth shop floor operations.
Enhancing equipment reliability and uptime through Maintenance Strategies
In order to ensure the effective and reliable usage of equipment, it is essential to implement appropriate maintenance strategies. Different types of maintenance can be employed based on the equipment's criticality, usage patterns, and manufacturer recommendations.
Preventive Maintenance (PM)
Regularly scheduled inspections and maintenance activities to prevent equipment failure.
Proactive replacement of worn-out parts or components before they cause breakdowns.
Lubrication, cleaning, and calibration of equipment according to manufacturer guidelines.
Documentation of maintenance activities and tracking equipment performance over time.
Predictive Maintenance
Utilising advanced technologies, such as sensors and data analytics, to predict equipment failures.
Continuous monitoring of equipment parameters to detect any signs of abnormal behaviour or deterioration.
Conducting condition-based maintenance when specific indicators reach predefined thresholds
Corrective Maintenance
Addressing equipment failures and breakdowns promptly to minimise downtime.
Timely repairs or replacements of components as needed.
Performing Root Cause Analysis(RCA) to prevent similar incidents in the future.
Having a reliable system for reporting and responding to equipment malfunctions.
Reactive Maintenance
Responding to equipment failures and malfunctions as they occur.
Performing repairs and fixes to restore equipment to working order.
Addressing unexpected breakdowns and failures promptly.
Planned Maintenance
Scheduled maintenance activities are conducted at predetermined intervals.
Performing routine inspections, servicing, and upkeep of equipment.
Replacing parts or components based on manufacturer recommendations or maintenance schedules.
Unplanned Maintenance
Emergency maintenance is performed in response to unforeseen circumstances.
Handling urgent repairs due to unexpected equipment failures or malfunctions.
Addressing immediate issues to minimise downtime and disruptions.
What are the factors affecting Equipment Reliability?
Adequate design and engineering of the equipment
Proper installation and setup
Regular and effective maintenance practices
Environmental conditions (temperature, humidity, vibration, etc.)
Operational load and stress on the equipment
Frequency of use and duration of operation
Training and competency of operators and maintenance personnel
Age and lifecycle of the equipment
Availability of spare parts and timely repairs
Compliance with industry standards and regulations.
Mitigating the Impact of Equipment Failure
- Emergency response plans and contingencies: Develop plans to respond effectively to equipment failures and establish contingency measures to minimise downtime and mitigate the impact on operations.
- Insurance coverage and risk management: Ensure adequate insurance coverage and implement risk management strategies to protect against financial losses resulting from equipment failures.
- Learning from past failures and corrective actions: Analyse previous failures, identify root causes and implement corrective actions to prevent similar incidents from occurring in the future.
- Collaborating with manufacturers and suppliers: Foster strong partnerships with equipment manufacturers and suppliers to access technical support, maintenance services, and expertise in resolving equipment failure issues.
Equipment failure poses significant business risks, including downtime, increased costs, and safety hazards. However, implementing a robust maintenance solution like CMMS (Computerised Maintenance Management System) can greatly mitigate these risks. CMMS enables manufacturers to streamline maintenance processes, schedule preventive maintenance, and track equipment performance. By leveraging CMMS, manufacturers can proactively identify and address potential failures, reducing downtime, optimising maintenance resources, and improving overall operational efficiency. Businesses must recognise the importance of CMMS and invest in this technology to enhance equipment reliability, minimise disruptions, and ensure long-term success in today's competitive landscape.