Top 5 mistakes in Maintenance Planning
August 9, 2023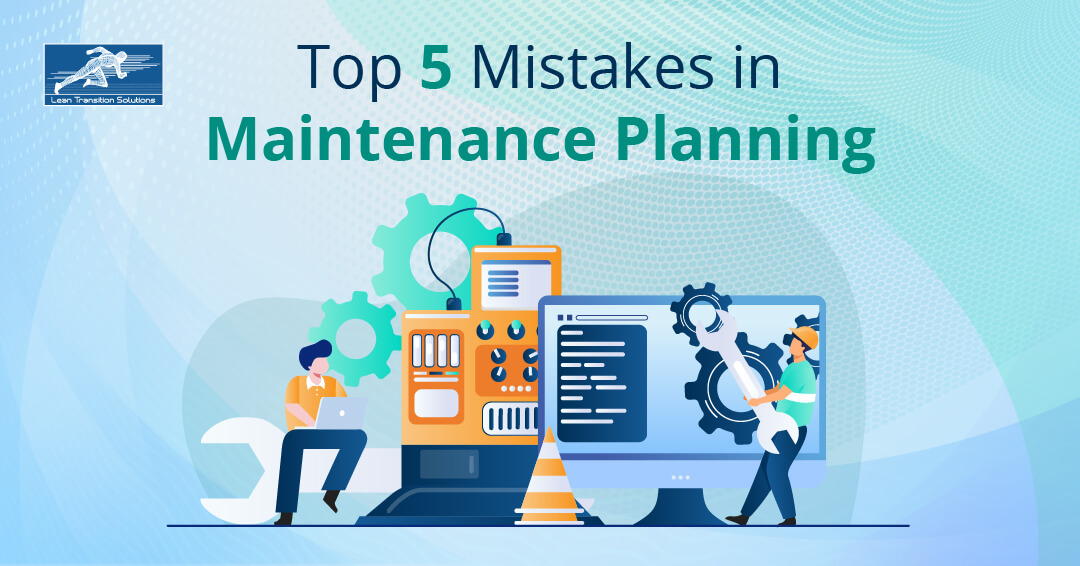
Effective maintenance planning plays a pivotal role in optimising operations and enhancing equipment performance. Effective maintenance strategies facilitate smooth execution and provide tangible advantages. In addition to cost reduction, well-planned maintenance can reduce downtime and increase efficiency.
However, even with the best intentions, common mistakes can undermine maintenance planning. Let's have a closer look at the top five mistakes in maintenance planning and solutions to avoid them. Maintenance teams can improve their performance, streamline operations, and promote a proactive maintenance culture by avoiding these common pitfalls.
What is Maintenance Planning?
Maintenance planning is strategically organising and preparing all necessary resources, activities, and schedules required to ensure the smooth and efficient execution of maintenance tasks. It involves carefully analysing and assessing the maintenance needs of assets, equipment, or systems and developing a comprehensive plan to address them effectively.
Maintenance planning encompasses defining maintenance objectives, setting schedules, estimating resource requirements, prioritising tasks, and identifying potential risks and challenges. The primary goal of maintenance planning is to maximise equipment reliability, minimise downtime, reduce maintenance costs, and ultimately optimise the overall performance of an organisation's assets.
In order to effectively reach your maintenance objectives, it is crucial to possess thorough maintenance management software like CMMS (Computerised Maintenance Management System). CMMS simplifies the process of maintenance planning, scheduling, and meeting preventive maintenance requirements. Managing maintenance tasks and improving asset performance is crucial for organisations. CMMS plays a key role in achieving these goals by completing maintenance tasks promptly, optimising resource allocation, and automating work orders.
Key aspects of Maintenance Planning
- Asset management: Asset management is a vital aspect of maintenance planning. It involves analysing and checking equipment specifications, criticality, service history, and maintenance requirements.
- Preventive Maintenance: A significant part of maintenance planning involves developing a preventive maintenance program. This program outlines scheduled maintenance tasks, inspections, and servicing required to prevent potential breakdowns, equipment failures, and safety hazards.
- Resource Allocation: Efficient maintenance planning involves allocating appropriate resources, such as manpower, materials, and tools, to carry out maintenance activities effectively and on time.
- Maintenance Scheduling: Maintenance tasks are scheduled strategically to minimise disruptions to regular operations and optimise resource utilisation. Scheduling ensures that maintenance is conducted during planned downtime or scheduled maintenance windows.
- Documentation of Maintenance activities: Proper maintenance planning involves detailed documentation of maintenance procedures, work orders, equipment history, and any changes made during the maintenance process. Documentation helps track progress, analyse historical data, and make informed decisions.
- Analysing Historical Maintenance Data: Maintenance planning involves the analysis of historical maintenance data to identify patterns, trends, and areas for improvement. Data analysis helps in refining maintenance strategies and decision-making.
- Collaboration and Communication with Maintenance Team: Effective maintenance planning requires collaboration and communication between maintenance teams, operators, and other relevant stakeholders. Transparent communication ensures that everyone involved is informed about maintenance activities and their impact on operations.
- Setting Maintenance KPIs: Maintenance planning involves setting maintenance KPIs to measure the effectiveness of maintenance activities. KPIs help evaluate maintenance efforts' performance and identify areas for continuous improvement.
5 Common mistakes in Maintenance Planning
Maintenance Planning mistakes can significantly affect an organisation's operations, equipment reliability, and maintenance costs. Organisations can avoid these mistakes by improving their maintenance planning, equipment performance, and operational efficiency. To do so, they should implement robust maintenance planning processes and use technological tools like Computerised Maintenance Management Systems (CMMS). By doing this, they can prevent errors and continuously improve their maintenance practices.
1. Overlooking Historical Maintenance Data
Emphasising the value of historical maintenance data is paramount in optimising maintenance planning. Historical data provides valuable insights into past maintenance activities, allowing organisations to identify patterns, trends, and recurring issues. By analysing historical data, maintenance teams can make informed decisions, anticipate potential problems, and develop more effective maintenance strategies.
Neglecting historical data in favour of reactive planning can lead to missed opportunities for improvement and increased downtime. Organisations may fall into a cycle of reacting to problems as they occur, resulting in higher maintenance costs and decreased equipment reliability.
Maintenance teams should implement a structured data collection and analysis approach to leverage historical data effectively. Organisations can proactively address maintenance needs, optimise resource allocation, and enhance overall maintenance performance by integrating historical data into their planning processes.
2. Underestimating Time and Resource Requirements
Underestimating the time and resource requirements for maintenance tasks can lead to significant risks and challenges in an organisation's maintenance operations. Rushed or inadequately planned maintenance activities may result in incomplete tasks and compromised equipment reliability. It can also lead to increased downtime, extended maintenance periods, and potential safety hazards.
Accurately estimating time and resource needs is essential to avoid this pitfall. Maintenance managers should conduct thorough assessments, consider the complexity of tasks and historical data, and involve relevant stakeholders in the planning process.Implementing a Computerised Maintenance Management System (CMMS) can assist in tracking maintenance histories and data analysis, enabling better forecasting and ensuring precise planning. By adequately estimating time and resources, organisations can execute maintenance tasks efficiently, improve equipment reliability, and enhance overall maintenance performance.
3. Ignoring Preventive Maintenance
Ignoring preventive maintenance is a critical mistake that can have severe consequences on an organisation's equipment reliability and maintenance costs. Preventive maintenance plays a crucial role in preventing breakdowns and costly repairs by addressing potential issues before they escalate into major problems. Organisations can proactively conduct regular inspections, servicing, and calibrations to identify and address equipment wear and tear, minimising the risk of unexpected failures and production disruptions.
Failing to prioritise preventive maintenance and relying solely on reactive maintenance approaches can lead to increased downtime, higher repair expenses, and decreased overall equipment lifespan.
To integrate preventive maintenance effectively into the planning process, organisations should develop a well-structured preventive maintenance program, schedule tasks based on equipment criticality, set up reminders for timely inspections, and allocate necessary resources for efficient execution. Organisations can significantly enhance equipment performance, reduce downtime, and optimise maintenance operations by making preventive maintenance a cornerstone of their planning strategy.
4. Lack of Communication and Collaboration
Lack of communication and collaboration among maintenance teams and other departments can harm an organisation's maintenance planning. Poor communication can lead to delays in task execution, duplicated efforts, and reduced overall efficiency. When teams fail to communicate effectively, critical information may not reach the right people at the right time, resulting in missed deadlines and inadequate resource allocation. Misunderstandings and misaligned priorities can exacerbate the situation, leading to costly errors and preventable breakdowns.
To foster better communication and collaboration, organisations should establish clear channels for information sharing, encourage regular meetings between maintenance teams and other stakeholders, and implement a unified communication platform. Training on effective communication and emphasising the importance of cross-departmental collaboration can enhance teamwork and ensure that maintenance planning aligns seamlessly with organisational goals.
5. Poorly Trained and Selected Maintenance Team
Having inadequately trained or poorly selected maintenance teams can severely affect an organisation's maintenance operations. Unqualified teams can lead to inefficient performance, compromised safety, and reduced equipment reliability. Inexperienced personnel may struggle to identify and address maintenance issues effectively, leading to prolonged downtime and increased maintenance costs.
Moreover, improper equipment handling can result in safety hazards for the maintenance team and other employees. Organisations must prioritise selecting skilled personnel with relevant technical expertise to mitigate these risks.
Regularly evaluating and updating the skill sets of the maintenance team through continuous training and development programs is essential. Offering opportunities for further industry certifications empowers the team to stay up-to-date with the latest maintenance practices and technologies, ensuring higher efficiency, safety, and equipment reliability in maintenance operations.
Four steps for aligning maintenance goals with business goals
Aligning maintenance goals with business goals ensures maintenance efforts contribute to the organisation's overall success.
- Understanding Business Objectives: Start by thoroughly understanding the organisation's business objectives and priorities. This involves engaging with key stakeholders, such as senior management, department heads, and operations teams. Identify the critical success factors the business aims to achieve, such as increased productivity, reduced downtime, improved safety, or enhanced customer satisfaction.
- Identifying Maintenance Requirements: Assess the maintenance requirements necessary to support the business objectives. Analyse the equipment, assets, and processes crucial for achieving the desired outcomes. This step involves conducting risk assessments, reliability analyses, and maintenance history reviews to identify areas that require attention and improvement.
- Defining Maintenance Goals: With a clear understanding of business objectives and maintenance requirements, establish specific maintenance goals that align with the broader business goals. These maintenance goals should be SMART: Specific, Measurable, Achievable, Relevant, and Time-bound. For example, if the business aims to increase production output by 10% over the next year, the maintenance goal could be to reduce equipment downtime by 20% to support the production target.
- Establishing Key Performance Indicators (KPIs): Develop a set of Key Performance Indicators (KPIs) that measure the progress and success of the maintenance efforts with the business goals. KPIs can include metrics such as Mean Time Between Failures (MTBF), Mean Time to Repair (MTTR), Overall Equipment Effectiveness (OEE), maintenance cost as a percentage of production cost, and more. Regularly track and review these KPIs to ensure maintenance activities contribute positively to the organisation's performance.
Maintenance planning ensures that maintenance activities are carried out in a systematic, timely, and cost-effective manner. It facilitates the achievement of operational excellence, asset reliability, and overall business goals. By proactively addressing potential issues and adhering to planned maintenance schedules, organisations can maximise the lifespan of their assets, reduce unexpected breakdowns, and optimise maintenance expenditures.
By acknowledging the importance of thorough data analysis and historical maintenance records, we can move away from reactive maintenance approaches and into proactive maintenance strategies. Modern maintenance management software like CMMS can streamline processes, enhance communication, and improve decision-making.
Failing to align maintenance goals with overarching business objectives can lead to wasted resources and missed opportunities to boost productivity and profitability. It is essential to prioritise collaboration and communication across departments to ensure everyone understands the impact of their role in achieving shared organisational goals.