A Roadmap to World Class Maintenance
February 20, 2024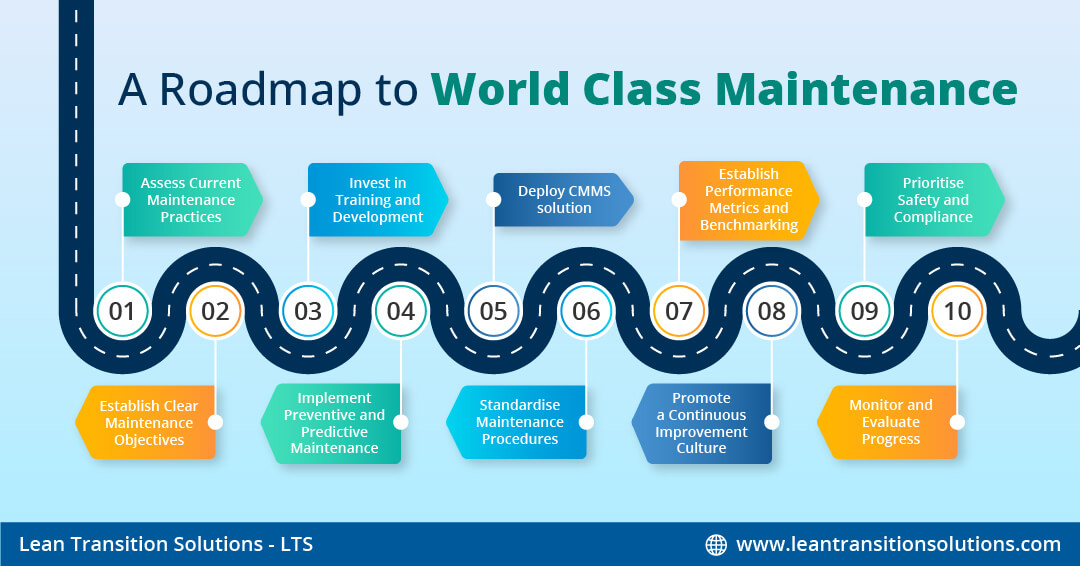
Manufacturers prioritising asset management, product quality, and lead time recognise maintenance as an essential pathway for operational excellence. World Class Maintenance is a global cornerstone for manufacturers, raising shop floor efficiency and quality. It's not just a goal; it's a complete approach integrating Kaizen, Total Quality Management, and Lean Manufacturing. These principles help businesses achieve excellence.
Businesses must change how they work to reach and keep up with world-class standards. They must optimise processes, embrace change, cut waste, and stay flexible. Let's understand how and why manufacturers strive to achieve standards in manufacturing processes through World-class maintenance practices.
What is World Class Maintenance?
World-class maintenance is a strategic approach that transcends traditional asset management, focusing on seamlessly integrating data, people, and assets within an organisation. For maintenance practices to be considered 'world-class,' they must adhere to the highest standards, minimising Key Performance Indicators like downtime and ensuring high work order completion rates, typically within the top 5% of industrial benchmarks. World-class maintenance extends beyond being a buzzword, emphasising the adoption of IIoT (Industrial Internet of Things) to achieve operational excellence. By implementing IIoT in day-to-day operations, organisations position themselves at the forefront of the Industry 4.0 revolution, ensuring optimal efficiency and reliability in their maintenance practices.
Importance of establishing World Class Maintenance
World-class Maintenance practices are crucial, and it offer several organisational benefits like:
- Cost Efficiency: Minimises downtime and reduces maintenance costs, optimising resources and improving cost-effectiveness.
- Improved Equipment Reliability: Focuses on preventive and predictive maintenance, enhancing equipment reliability and availability for increased productivity.
- Enhanced Safety: Identifies and addresses hazards, ensuring a safer environment through regular inspections and compliance with safety regulations.
- Quality Assurance: Maintains optimal equipment performance, improving product quality and consistency to meet customer expectations.
- Sustainability: Extends equipment lifespan, reduces energy consumption, and minimises waste generation, promoting sustainable operations.
- Competitive Advantage: Enables faster response times and greater flexibility, positioning the organisation as a preferred choice among competitors.
- Data-Driven Decision Making: Utilises data analytics and predictive technologies to optimise maintenance schedules and resource allocation for continuous improvement.
Key Principles of World-Class Maintenance
- Employee Empowerment: Encouraging staff to take ownership and responsibility for maintenance tasks, fostering a culture of accountability and continuous improvement.
- Minimising Costs: Implementing cost-effective maintenance strategies to optimise resource allocation, reduce wastage, and maximise efficiency in operations.
- Increasing Asset Availability: Utilising asset management and optimisation techniques, employing asset lifecycle management principles, monitoring and analysing asset performance, and continuously improving asset reliability to ensure equipment availability meets operational needs.
- Improving Safety and Quality: Prioritising safety through rigorous safety protocols, training, and adherence to regulations while enhancing product quality through consistent maintenance and quality control measures.
8 Pillars of World Class Maintenance
- Maintenance Organisation: The maintenance department should feature a flat structure with fewer hierarchical levels and clearly defined duties and responsibilities, fostering efficiency and accountability.
- Maintenance Information System: Implementing a robust maintenance information system like CMMS to centralise data, streamline processes, and facilitate informed decision-making, enhancing operational effectiveness.
- Maintenance Training & Development: Prioritising ongoing training and development programs to equip maintenance personnel with the necessary skills and knowledge, ensuring competence and adaptability in handling evolving maintenance challenges.
- Maintenance Scheduling, Planning & Control: Employing maintenance planning and scheduling techniques, managing work orders efficiently, allocating resources effectively, addressing maintenance backlog, optimising maintenance operations and resource utilisation.
- Overall Equipment Effectiveness and Benchmarking: Monitoring Overall Equipment Effectiveness (OEE) and benchmarking performance metrics against industry standards to identify improvement areas, driving continuous enhancement of maintenance practices.
- Maintenance Prevention and Maintainability Improvement: Adopting condition monitoring techniques and predictive maintenance strategies to anticipate equipment failures, enhancing maintainability and minimising downtime.
- Autonomous Maintenance: Encouraging frontline operators to take ownership of equipment care and conduct routine maintenance tasks, fostering a proactive maintenance culture and reducing reliance on centralised maintenance teams.
- Maintenance Cost Reduction: Implementing cost-effective maintenance strategies, optimising resource allocation, and leveraging efficiency measures to reduce maintenance costs without compromising quality or reliability.
Strategies for implementing World Class Maintenance
- Ensure Leadership and Management Commitment: Secure commitment from leadership and management to prioritise and support the implementation of world-class maintenance practices, ensuring alignment with organisational goals and objectives.
- Utilise Tools and Technologies: Implement modern tools and technologies such as Computerised Maintenance Management Systems (CMMS) to streamline maintenance processes, improve efficiency, and enhance data-driven decision-making.
- Establish SOPs for Maintenance Programs: Develop Standardised Operating Procedures (SOPs) to ensure consistency, reliability, and safety in maintenance operations, enhancing effectiveness and minimising errors.
- Create a Maintenance Policy with an improvement plan: Formulate a comprehensive maintenance policy outlining goals, objectives, and improvement plans to guide maintenance activities, foster accountability, and drive continuous improvement in maintenance processes and outcomes.
- Secure 100% execution of your maintenance task: Strive for 100% compliance with maintenance tasks by the "10% rule," ensuring that all scheduled maintenance activities are completed promptly and accurately to maintain equipment reliability and operational efficiency.
Steps to achieve World-Class Maintenance
- Assess Current Maintenance Practices: Evaluate existing maintenance processes to identify strengths, weaknesses, and improvement areas to lay the foundation for transformation.
- Establish Clear Maintenance Objectives: Define specific, measurable objectives aligned with organisational goals, ensuring clarity and direction in achieving world-class maintenance practices.
- Invest in Training and Development: Provide comprehensive training programs for maintenance personnel to enhance skills, knowledge, and proficiency in modern maintenance techniques and technologies.
- Implement Preventive and Predictive Maintenance: Integrate predictive and preventive maintenance strategies to proactively identify and address equipment issues, minimising downtime and maximising asset reliability.
- Deploy CMMS solution: Embrace technological advancements such as CMMS software to automate processes, optimise resource allocation, and facilitate data-driven decision-making in maintenance operations.
- Standardise Maintenance Procedures: Develop Standardised Operating Procedures (SOPs) to ensure consistency, reliability, and safety in maintenance activities, enhancing efficiency and reducing errors.
- Establish Performance Metrics and Benchmarking: Define Maintenance KPIs and benchmarks to measure maintenance effectiveness, identify improvement areas, and drive continuous enhancement for maintenance practices.
- Promote a Continuous Improvement Culture: Foster a culture of continuous learning, innovation, and improvement among maintenance teams, encouraging collaboration, feedback, and knowledge sharing.
- Prioritise Safety and Compliance: Prioritise safety protocols and regulatory compliance in maintenance operations, ensuring a safe work environment and adherence to industry standards and regulations.
- Monitor and Evaluate Progress: Regularly monitor and evaluate progress towards achieving world-class maintenance practices. Adjust strategies as needed, and celebrate milestones to sustain continuous improvement and enhance motivation.
Best Practices for Achieving World-Class Maintenance
- Proactive Maintenance Approaches: Prioritising preventive, predictive, and reliability-centred maintenance strategies over reactive maintenance to prevent equipment failures, optimising asset performance, and minimising downtime ensures operational efficiency and longevity of assets. Achieving world-class preventive maintenance involves maintaining approximately 80% through preventive measures and addressing 20% through reactive responses.
- Continuous Equipment Monitoring: Utilising data analytics and machine learning to monitor equipment health, identify issues promptly, and schedule maintenance, maximising uptime and reducing costs.
- CMMS Software Integration: CMMS software (Computerised Maintenance Management System), along with IoT and AI technologies, can centralise maintenance data, automate workflows, and track asset performance, facilitating streamlined operations and informed decision-making.
- Safety and Compliance: Establishing robust safety protocols, conducting regular inspections, and ensuring compliance with industry standards to safeguard employees, mitigate risks, and maintain a secure work environment, fostering accountability and organisational integrity.
- Continuous Improvement: Encouraging innovation and learning from past experiences to optimise maintenance processes, enhance efficiency, and stay ahead of industry trends, fostering adaptability and agility in a dynamic business environment.
World Class Maintenance Examples
Manufacturers strive for world-class maintenance practices, including the effective management of wrench time (also known as tool time, which refers to the duration technicians spend actively engaged in repairing or maintaining equipment during a job), to ensure optimal performance, reliability, and efficiency of their equipment and assets. These examples serve as benchmarks for manufacturers to assess and continuously improve their maintenance practices, striving towards world-class standards in equipment reliability, operational efficiency, and organisational performance.
- Maintenance Schedule Compliance: Exceeding 90% adherence to maintenance schedules ensures that planned maintenance tasks are completed on time, minimising downtime and optimising asset performance.
- Maintenance Overtime: Maintaining overtime below 5% indicates effective planning and resource allocation, reducing unnecessary labour costs and enhancing productivity.
- Maintenance Direct Work: Achieving over 75% direct work in maintenance activities indicates efficient utilisation of maintenance resources, maximising the time spent on value-added tasks.
- Planned Maintenance Work: Ensuring that over 90 % of maintenance work is planned allows for proactive maintenance strategies, minimising reactive interventions and improving overall equipment reliability.
- Preventive Maintenance Schedule Compliance: Achieving 100% compliance with preventive maintenance schedules helps prevent equipment failures and prolongs asset lifespan, ensuring consistent performance.
- Work Order Coverage: Having 100% of maintenance work covered by a work order promotes accountability, visibility, and proper documentation of maintenance activities.
- Work Order Actual Hours vs Planned Hours: Maintaining a 90 to 110% ratio between actual and planned work order hours reflects effective planning and execution of maintenance tasks, optimising resource utilisation.
- Equipment Availability: Maintaining equipment availability at a minimum of 90% ensures that assets are operational when needed, supporting uninterrupted production and minimising revenue loss.
- Equipment Productivity: Achieving equipment productivity levels of at least 95% indicates efficient utilisation of assets, maximising output while minimising resource consumption.
- Overall Equipment Effectiveness (OEE): Sustaining OEE levels of at least 77% reflects the overall efficiency of equipment, encompassing availability, performance, and quality metrics to drive continuous improvement and operational excellence.
For maintenance operations, embracing innovation is the golden ticket to untapped excellence. Proactive maintenance strategies like predictive, preventive and reliability-centred maintenance can pave the way for remarkable efficiency and reliability for your shop floor assets.
Think of maintenance not just as a reactive measure but as a proactive strategy that can identify and address challenges. Manufacturers can transcend conventional boundaries and redefine the essence of World-Class Maintenance through constant adaptation and a keen eye for emerging trends.
CMMS is this transformative solution chosen by manufacturers as it supports the maintenance needs of every industry, irrespective of its sector. Why lag behind without a CMMS solution for your manufacturing operations? Implementing CMMS can propel you towards the world-class standards you have always aspired to achieve.