Essential World-Class Maintenance Metrics Every CMMS Should Measure
November 18, 2024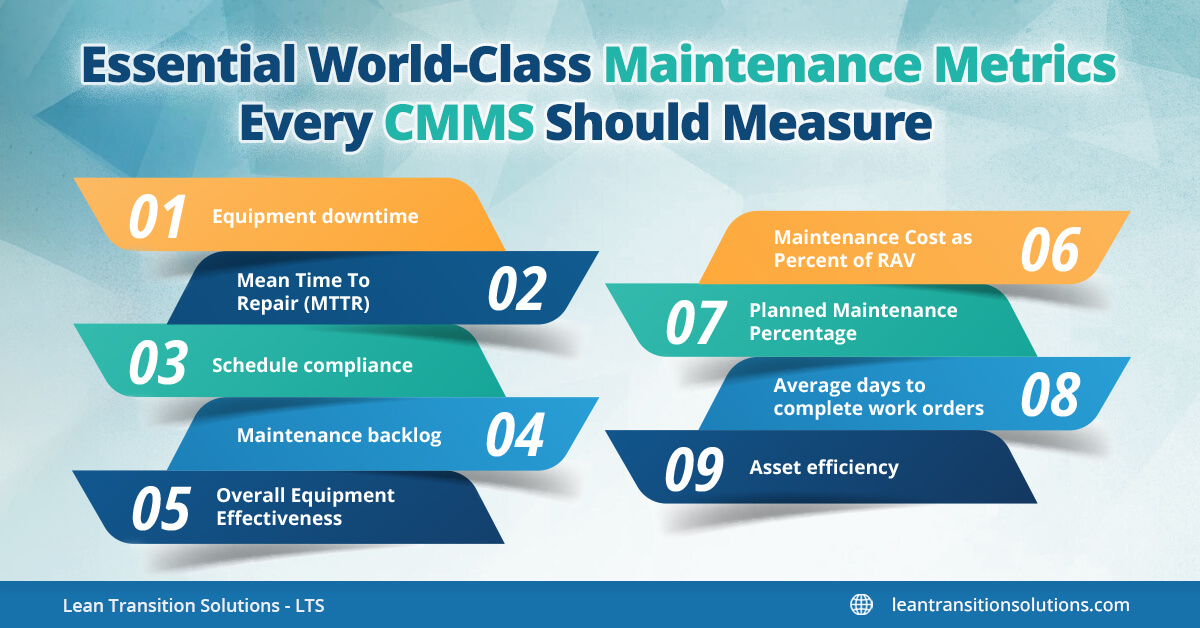
World-Class Maintenance for Industry 4.0. is not just about managing the assets or the funds involved but about creating and fostering assets, people and data. An advanced level of maintenance is crucial in the current market for manufacturers who desire to thrive. In order to gain results in the maintenance world, businesses must follow a progressive hierarchy which measures World-class maintenance metrics.
World-class maintenance is a proactive and data-driven maintenance method which can be achieved by integrating a powerhouse tool that actively drives improvements. Computerised Maintenance Management System (CMMS) is the robust tool here that helps manufacturers achieve a world-class level of excellence by transforming maintenance from a burden into a powerful asset.
Why CMMS is essential for Metric Mastery?
Maintenance metrics are the Key Performance Indicators (KPIs) necessary to measure the efficiency, reliability and effectiveness of an organisation's maintenance efforts. Everything in maintenance depends upon machines and humans. For maintenance success, it is vital to optimise the performance of assets and people. Proper tracking of maintenance metrics provides room for improvement by monitoring everything from equipment uptime to repair speed.
Have you ever thought about why organisations never compromise when choosing a CMMS software for the effective running of their maintenance strategy?
The absence of CMMS leads to a lack of real-time analysis of performance that results in generating preventive rather than reactive maintenance decisions.
Key challenges of not having a CMMS to track Maintenance metrics
Limited Visibility into Performance
Difficulties in Compliance and Reporting
Inconsistent Maintenance Schedules
Inefficient Resource Allocation
Higher Costs and Downtime
Manual maintenance processes are limited and often incapable of tracking maintenance metrics because they are constrained, time-consuming, imprecise, and not scalable when compared to what CMMS offers. Hence, to connect your performance to progress, an efficient CMMS software that tracks your necessary metrics is inevitable. Tracking the right metrics turns data into information and information into strategies.
Let's understand the important metrics that a CMMS should measure to deploy a world-class maintenance strategy.
World-Class Maintenance: Metrics that define Maintenance Quality
Equipment Downtime
Automatically generate reports regarding equipment downtime
Forecast equipment failures by providing predictive maintenance strategies
Reduce downtime by planning preventive maintenance operations
Manage corrective maintenance
Identify which equipment needs more maintenance and track maintenance costs
Provide Mean Time Between Failures (MTBF) calculation based on how frequently the machine stopped working down
Mean Time to Repair (MTTR)
Provide real-time tracking of maintenance tasks
Give easy access to repair data and automated alerts that are easily accessible to technicians
Organises repair workflow and resolves issues faster
Lower MTTR by managing the process
Schedule Compliance
Automate maintenance schedule and provide timely reminders
Provide real-time visibility into working progress, which eases the monitoring of compliance
Prioritise urgent tasks along with preventing overlap
Adjust the schedules as needed for timely completion
Maintenance Backlog
Ensure critical operations are not delayed by understanding the urgency
Include predictive, preventive and corrective maintenance tasks in the maintenance backlog
Shows available tools, technicians and parts to assign resources accurately
Overall Equipment Effectiveness
Schedule routine inspections and repairs to make equipment stay in operational condition
Track and analyse cycle time, delays and aids in eliminating faults
Identify which equipment needs replacement
Ensure measures operate with optimal conditions
Identify the fluctuations that affect the product quality
Maintenance Cost as Percent of RAV (Replacement Asset Value)
Better insights into maintenance spending
Real-time cost tracking
Preventive Maintenance Scheduling to Reduce High-Cost Repairs
Manage spare parts and inventory levels
Report maintenance trends, including recurring costs on specific assets
Planned Maintenance Percentage
Tracks each maintenance job as planned or unplanned
Create detailed word order with specific instructions
Minimise unplanned maintenance
Average days to complete Work Orders
Prioritise the work order process
Helps managers to assign tasks
Minimise the time spends on each job in the maintenance queue through real-time updates
Provide instant alerts related to estimated completion times, standards procedures and parts required
Monitor the technician performance and track their time spend
Asset Efficiency
Make proactive asset monitoring and preventive maintenance schedules
Make regular checks on minor part replacement and lubrication
Give alerts of wear and tear indicators
Assign repair technician for minor issues
The non-operating time of equipment can be called equipment downtime. There are two types of equipment downtime: planned and unplanned. The planned equipment downtime includes the necessary downtime for preventive maintenance. It is the intended time to shut down the equipment. On the other hand, broken parts and operational faults cause unplanned equipment failure, which the company did not intend to happen.
In such cases, efficient CMMS intervention can be beneficial. CMMS maintain organisational equipment daily and avoids unforeseen breakdowns. Other actions it takes include:
MTTR is a metric that measures the average time needed to repair a machine, which means the time necessary to make the failed system fully functional again. This involves the time required to recognise the failure, diagnose the problem and solve the issue. By tracking MTTR, organisations can maintain their strategies by analysing the reliability and availability of systems.
The CMMS calculate MTTR by tracking work orders, maintenance team schedules and repair history. Have a look at how CMMS software tracks the Mean Time to Repair:
Schedule compliance is a metric that determines the functionality and productivity of the scheduled maintenance process. Through this measurement, the managers get insights about timely work completion. It compares the total number of schedules with how many of them were completed. Maintenance distraction, lowered performance, and breakdowns cause low schedule compliance. This will result in missing tasks and targets.
CMMS can ensure a high Schedule compliance percentage by performing root cause analysis and guiding corrective actions. The actions taken by the CMMS software to deliver high-schedule compliance are given below.
The maintenance backlog contains the tasks that need to be completed but are not scheduled for completion. It is determined for the entire maintenance operation. A maintenance backlog is necessary for measuring the performance of an organisation, and it provides more granular data about the sales backlog. Completing the backlog tasks within the scheduled time is vital for preventing asset breakdown and nurturing a productive and safe workplace. Ensuring maintenance tasks are resolved promptly reduces the risk of the overall process.
CMMS software plays a significant role in managing maintenance backlog by centralising the schedules, prioritising urgent tasks and ensuring resources are appropriately allocated. Look at how this happens.
Through the measurement of the gold standard metric of Overall Equipment Effectiveness (OEE), organisations can understand the performance of equipment that identifies the truly productive time. OEE is the combination of Availability (the function of the asset as needed), Performance (the asset produces quantity) and Quality (the quality items the asset produces). An OEE of 100% means that each product is of perfect quality, running at the fastest possible speed, and has no time lost due to equipment failures or breakdowns.
CMMS software can calculate OEE accurately and identify the areas needed for improvement. With the OEE calculation, CMMS provide informed decisions, continuous improvement and optimised performance.
CMMS tracks performance data and quickly generates work orders for detected issues. Other key benefits it provides are given below.
The metric Maintenance Cost as Percent of RAV helps to calculate the cost-effectiveness of the operation of the maintenance program in which the RAV stands for Replacement Asset Value. It can be obtained by calculating the yearly maintenance expenditure for an asset divided by the replacement value of that asset.
Higher maintenance costs imply that the business spends nearly as much as it would on completely replacing a facility. A low RAV percentage indicates a well-optimised maintenance strategy, and a Moderate RAV percentage reflects a balanced approach.
The CMMS captures the costs, failure trends, and maintenance histories by automating maintenance data management. Look at the benefits of having a CMMS for tracking Maintenance Costs as Percent of RAV
Planned maintenance percentage (PMP) is a vital metric that is taken to assess the effectiveness of preventive maintenance programs. It measures the amount of time spent on planned maintenance tasks compared to all maintenance tasks in a given time.
This metric can be used to track the time spent on maintenance. It also indicates the time spent on fixing corrective issues and unplanned downtime events. Maintenance managers need to calculate PMP at weekly, monthly or yearly intervals.
With the use of an effective CMMS, the organisation gets more insights into resource allocation, cost-effectiveness, and equipment longevity. Other key benefits it provides are given below.
Average days to complete work orders is a maintenance metric that shows the average days it takes to complete a work order. A higher value of average days to complete a work order indicates the issues that prevent work order completion. This metric helps the organisation identify the causes of issues in the maintenance program.
CMMS plays a significant role in reducing Average days to complete work orders by streamlining the work order process. The actions taken by CMMS to provide insights about it are given below.
Asset efficiency metric is important for analysing the effectiveness of the maintenance process. It shows how well the equipment is running and helps to overcome the daily challenges. The efficiency of equipment is determined by evaluating it within the aspects of safety regulation adherence, minimum repair costs, and repair procedure.
The three dimensions of asset efficiency are asset availability, asset performance and asset yield. Higher asset efficiency indicates the use of assets to create revenue in the most optimal way.
CMMS ensures better asset management with systematic planning, optimising and planning assets for higher efficiency. Let's have a look at what CMMS do to ensure higher asset efficiency.
Elevate your Maintenance game with CMMS-Driven Metric Insights
Maintenance metrics, the lifeblood of effective maintenance, highlight the levels of asset availability, repair productivity, schedule reliability, and cost. However, without the availability of a proper tool, such as a Computerised Maintenance Management System CMMS, controlling and improving these metrics is practically incomprehensible. CMMS makes valuable insights, enhances asset longevity, and supports proactive decisions by automatically tracking essential maintenance metrics.
From equipment downtime to asset efficiency, maintenance metrics act as the backbone of a data-driven, proactive approach. If you are willing to convert maintenance issues into tangible results, then it's time to get a CMMS. The individual metrics and the insights CMMS provide do more than maintain assets: they build value, optimise costs and keep your business running seamlessly. Start using CMMS software today and take your maintenance approach to a truly world-class level.
FAQs
1. What is the maintenance metric?
Maintenance metrics are the Key Performance Indicators (KPIs) that act as the backbone of an organisation's data-driven, proactive approach. It is useful to measure the efficiency, reliability and effectiveness of an organisation's maintenance efforts.
2. What is the meaning of world-class maintenance?
World-class maintenance is a strategic approach to maintenance operation that adheres to the highest standards, minimising Key Performance Indicators like downtime and ensuring high work order completion rates, typically within the top 5% of industrial benchmarks.
3. What are the essential World-Class Maintenance Metrics?
Equipment downtime
Maintenance backlog
Asset efficiency
Mean Time to Repair
Average days to complete work orders
Planned Maintenance Percentage
Maintenance Cost as Percent of RAV
Schedule compliance
Overall Equipment Effectiveness
4. How to measure maintenance metrics?
Maintenance metrics can be measured by evaluating the performance of maintenance activities. With a computerised Maintenance Management System (CMMS) makes valuable insights, enhances asset longevity and supports proactive decisions by automatic tracking of essential maintenance metrics.