Contents
- What is a Maintenance Report?
- Why is Maintenance Reporting important?
- How can you submit a Maintenance Report?
- What types of Maintenance Issues should be reported?
- What happens after you submit a Maintenance Request?
- What are the key benefits of creating a Maintenance Report?
- Why should Maintenance Data be accurate and complete?
- How quickly are Maintenance Issues addressed after reporting?
- What should be included in a Maintenance Report?
- Are there any specific instructions for reporting recurring Maintenance Issues?
- Is it possible to report multiple Maintenance issues in one submission?
- How often should routine maintenance be reported?
- Is it possible to provide feedback on the Maintenance Process?
- What Metrics and KPIs can measure the performance of your Maintenance Activity?
- How do Maintenance technicians contribute to the overall efficiency of a Maintenance Program?
- What role does mobile accessibility play in enhancing the effectiveness of Maintenance Reporting?
- How does automation in Maintenance Reporting contribute to operational efficiency?
- Maintenance Report Example
What is a Maintenance Report?
A Maintenance Report is a concise document that outlines maintenance activities performed on equipment, facilities, or systems. It typically includes information on repairs, maintenance logs, inspections, and any replacements carried out during a specific time frame. The purpose of a Maintenance Report is to provide a comprehensive overview of the maintenance status, ensuring transparency and facilitating informed decision-making for ongoing facility or equipment management. It is a valuable tool for tracking maintenance costs, identifying recurring issues, and planning preventive measures to optimise operational efficiency and reduce downtime.
Why is Maintenance Reporting important?
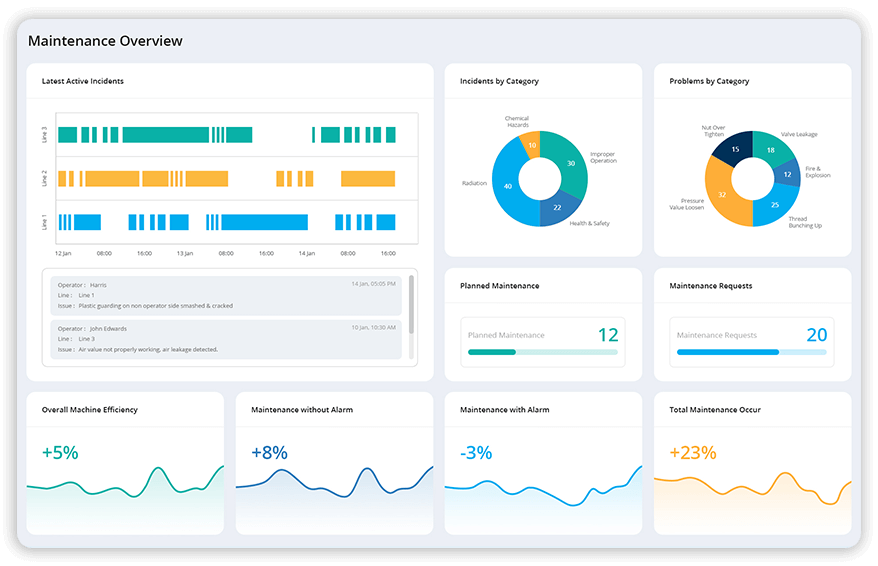
Maintenance Reporting is crucial for effective facility and equipment management, providing a detailed account of maintenance activities, repairs and inspections. These reports contribute to transparency, allowing stakeholders to track the performance and condition of assets over time. They act as a useful tool for decision-making, helping identify recurring issues, plan preventive measures, and optimise maintenance schedules. By documenting maintenance data, these reports enhance accountability, support regulatory compliance, and facilitate cost-effective resource allocation. Overall, Maintenance Reports are essential for informed decision-making, efficient operations, and the longevity of assets within an organisation.
How can you submit a Maintenance Report?
Preparing a Maintenance Report using CMMS software involves several steps to ensure accuracy and completeness. Here's a step-by-step guide:
- Choose the right CMMS Software: Access the CMMS system using your credentials to begin the reporting process.
- Navigate to the Maintenance Reporting Section: Locate the reporting or work order section within the CMMS dashboard.
- Select "Create New Report" or Equivalent: Choose the option to initiate a new maintenance report within the CMMS interface.
- Fill in Basic Details: Enter essential information, including the date and time of the maintenance activity, the specific location, and the equipment or assets involved.
- Describe the Maintenance Activity: Clearly articulate the nature of the maintenance work performed, detailing repairs, inspections, or preventive measures.
- Attach Supporting Documents : Include relevant documents, images, or files that provide additional context or support the maintenance report if applicable.
- Establish Accountability: Record the names or roles of individuals who conducted or supervised the maintenance activity for accountability.
- Include Detailed Notes or Observations : Provide any pertinent information, such as abnormalities, potential issues, or recommendations for future actions.
- Review and Submit: Review the completed maintenance report for accuracy and completeness. Once satisfied, submit the report to the CMMS.
- Receive Confirmation and Updates: Confirm that the maintenance report has been submitted successfully, and if applicable, expect updates on the status of the maintenance request.
What types of Maintenance Issues should be reported?
Any maintenance issues, whether preventive or corrective, should be promptly reported for effective facility management. This includes equipment breakdowns , malfunctioning machinery, safety hazards, and routine maintenance requirements. Additionally, any abnormalities, unusual sounds, or signs of wear and tear should be reported to address potential problems before they escalate. Reporting these issues ensures timely intervention, reduces downtime, and supports a proactive approach to maintenance. In a comprehensive reporting system, details such as date, time, location, and the nature of the issue are documented, contributing to data-driven decision-making and the optimisation of maintenance strategies.
What happens after you submit a Maintenance Request?
After submitting a Maintenance Request, the process typically involves review and prioritisation by maintenance personnel. The request is logged into the CMMS (Computerised Maintenance Management System), and its urgency and impact on operations are assessed. Maintenance teams then plan and schedule the necessary activities, allocating resources accordingly. The requester may receive updates on the status of the request, and once addressed, details of the completed maintenance are documented for future reference. This systematic approach ensures a timely response to maintenance needs, fosters transparency, and contributes to the overall efficiency of facility management.
What are the key benefits of creating a Maintenance Report?
- Early Issue Detection: Identifies potential equipment problems before they escalate.
- Reduced Downtime: Minimises unplanned downtime through proactive maintenance.
- Optimised Performance: Enhances equipment efficiency and longevity.
- Cost Savings: Reduces overall maintenance costs by addressing issues promptly.
- Regulatory Compliance: Ensures adherence to industry standards and safety compliance requirements.
- Data-Driven Decision Making: Provides insights for informed decision-making based on maintenance trends.
- Preventive Maintenance : Facilitates the implementation of preventive maintenance schedules.
- Documentation for Audits: Acts as a record for compliance audits and quality assurance.
- Enhanced Safety: Improves workplace safety by addressing potential hazards.
- Asset Management : Supports effective management of equipment throughout its lifecycle.
- Increased Productivity: Ensures equipment availability, boosting overall production output.
- Improved Planning: Enables better planning for resource allocation and future maintenance activities.
Why should Maintenance Data be accurate and complete?
Accurate and complete maintenance data is essential for effective decision-making and streamlined operations. Inaccuracies or omissions in maintenance records can lead to inefficient resource allocation, increased downtime, and compromised asset performance. Precise data enables organisations to proactively identify patterns, predict equipment failures, and implement preventive measures. CMMS systems ensure accuracy by providing a centralised platform for recording and managing maintenance data. These systems facilitate real-time data entry and actively trigger maintenance requests based on predefined schedules or condition-based triggers. With accurate and comprehensive maintenance data, organisations can enhance asset reliability, optimise maintenance processes, and make informed decisions to maximise operational efficiency.
How quickly are Maintenance Issues addressed after reporting?
The speed at which maintenance issues are addressed after reporting varies based on urgency, severity, and organisational processes. Critical issues, such as equipment breakdowns and safety hazards, are addressed immediately to minimise downtime and prevent further damage. Organisations with well-established maintenance protocols and efficient CMMS systems can promptly prioritise and address reported issues. In contrast, routine or non-urgent matters may follow a predefined maintenance schedule. Quick response times are crucial in preventing disruptions, optimising asset performance, and upholding overall operational efficiency. Regular monitoring and feedback mechanisms within the maintenance process contribute to a responsive system that ensures timely issue resolution.
What should be included in a Maintenance Report?
- Description of Maintenance Activity: Clearly articulate the nature of the maintenance work performed, detailing repairs, inspections, or preventive measures.
- Date and Time: Specify when the maintenance activity took place to establish a timeline for tracking and analysis.
- Location: Identify the specific site or equipment location where the maintenance occurred for accurate record-keeping.
- Equipment Involved: Clearly state the equipment, machinery, or assets subject to maintenance to ensure precision in reporting.
- Detailed Notes or Observations: Include any pertinent information, such as abnormalities, potential issues, or recommendations for future actions.
- Attachments: If applicable, attach relevant documents, images, or files that provide additional context or support the maintenance report.
- Personnel Involved: Record the names or roles of individuals who conducted or supervised the maintenance activity for accountability.
- Status Updates: Specify the current status of the equipment or facility post-maintenance to track the effectiveness of the performed activities.
Are there any specific instructions for reporting recurring Maintenance Issues?
For reporting recurring maintenance issues:
- Follow established protocols outlined by the organisation.
- Use designated reporting channels, such as the maintenance request system or a specialised platform within the CMMS (Computerised Maintenance Management System).
- Provide detailed information on the nature of the issue, including past occurrences, to assist maintenance teams in identifying patterns and implementing effective solutions.
- If available, use any documentation or photos that can provide context and aid in addressing the root cause of the recurring problem.
Timely and precise reporting of recurring issues supports a proactive approach to maintenance, minimising disruptions and promoting long-term asset reliability.
Is it possible to report multiple Maintenance issues in one submission?
Yes, many maintenance reporting systems allow for the submission of multiple maintenance issues in a single request. This streamlines the reporting process, enabling users to communicate concerns efficiently within one submission. By consolidating various issues, users can provide comprehensive details, including descriptions, locations, and priorities, facilitating a more organised and prioritised response from maintenance teams. This feature enhances user convenience, promotes thorough communication, and effectively manages diverse maintenance needs within an organisation.
How often should routine maintenance be reported?
Routine maintenance should be reported on a predefined schedule or as per established protocols within an organisation. Reporting frequency is often determined by factors such as equipment type, industry regulations, and organisational policies. Typically, routine maintenance reports are submitted at regular intervals, allowing for the systematic tracking of asset conditions and the timely scheduling of preventive measures. Consistent and timely reporting ensures that equipment remains in optimal condition, minimising the risk of breakdowns and supporting overall operational efficiency.
Is it possible to provide feedback on the Maintenance Process?
It is possible and essential to provide feedback on the maintenance process. Many organisations encourage feedback mechanisms to improve efficiency and address concerns. A CMMS (Computerised Maintenance Management System) facilitates this feedback loop by offering a platform for users to share their insights and experiences with the maintenance process. Users can provide feedback on the responsiveness of the maintenance team and the effectiveness of solutions and suggest improvements. Utilising the CMMS for feedback ensures a systematic and documented approach, allowing organisations to analyse input, implement necessary changes, and continuously enhance their maintenance processes for optimal performance.
What Metrics and KPIs can measure the performance of your Maintenance Activity?
Several maintenance metrics and KPIs (Key Performance Indicators) can effectively measure the performance of maintenance activities. Metrics such as Mean Time to Repair (MTTR), Mean Time Between Failure (MTBF), Planned Maintenance Percentage (PMP) and Overall Equipment Effectiveness (OEE) provide insights into the efficiency of maintenance processes. Tracking Preventive Maintenance Compliance (PMC), equipment downtime, and work order completion rates are crucial maintenance KPIs. These indicators offer a comprehensive view of maintenance performance, enabling organisations to assess reliability, optimise resource allocation, and enhance overall operational efficiency. Regularly monitoring these metrics ensures a proactive approach to maintenance management and supports data-driven decision-making for continuous improvement.
How do Maintenance technicians contribute to the overall efficiency of a Maintenance Program?
Maintenance technicians play a pivotal role in enhancing the overall efficiency of a maintenance program. Their expertise in diagnosing and addressing issues impacts the reliability and performance of equipment. Technicians contribute by adhering to preventive maintenance schedules, promptly addressing reported issues, and ensuring the accuracy of maintenance reports. Collaborating with maintenance teams, they actively participate in troubleshooting, implementing solutions, and providing valuable feedback to optimise processes. Their proactive approach to maintenance tasks and efficient maintenance reporting systems facilitate a streamlined workflow, minimise downtime, and support the organisation's commitment to operational excellence. Maintenance technicians rely on maintenance logs to guide shop floor maintenance practices.
What role does mobile accessibility play in enhancing the effectiveness of Maintenance Reporting?
Mobile accessibility plays a key role in enhancing the effectiveness of maintenance reporting by providing on-the-go access to reporting systems. Maintenance technicians can conveniently submit reports directly from the field, ensuring real-time documentation of issues and activities. This immediacy improves response times, enables quicker decision-making, and enhances efficiency. Mobile accessibility also promotes collaboration, as maintenance teams can instantly communicate seamlessly and access critical information, contributing to a more agile and responsive maintenance process. This capability ensures that maintenance reporting aligns with the dynamic and fast-paced nature of field operations, ultimately optimising the performance of maintenance programs.
How does automation in Maintenance Reporting contribute to operational efficiency?
Automation in maintenance reporting significantly contributes to operational efficiency by streamlining and expediting the reporting process. Automated systems like CMMS can capture real-time data , reducing manual input errors and ensuring accuracy. Scheduled automatic reporting facilitates timely updates and preventive maintenance alerts, minimising downtime. Additionally, automation accelerates the workflow, allowing for quick response to reported issues and efficient allocation of resources. By eliminating manual bottlenecks, these systems enhance the overall speed, precision, and effectiveness of maintenance reporting, leading to optimised operational performance and resource utilisation.
Maintenance Report Example
CMMS (Computerised Maintenance Management System) shows remarkable versatility as an indispensable tool across diverse industries. CMMS seamlessly adapts to the unique needs of each sector, such as Manufacturing, Automotive, Construction, Energy, Plant hire, Healthcare, and many more. Its universal applicability lies in its ability to create maintenance reports efficiently, ensuring optimal equipment performance and operational excellence, regardless of the industry type.
Let’s look at an example of a maintenance report in the automotive sector where a fault occurred in a robotic arm in the welding section.
Maintenance Report | |||
---|---|---|---|
Equipment ID | ARB-123456 | Date and Time of Maintenance | January 2, 2024, 09:00 AM |
Location | Welding Section, Automotive Manufacturing Plant | Maintenance Personnel |
|
Description of Maintenance Tasks | Parts/Components Replaced |
---|---|
The maintenance activities were initiated to address a fault in the robotic arm (Equipment ID: ARB-123456) involved in the welding section. The tasks performed during maintenance included a comprehensive inspection, adjustments to the robotic arm's programming, and replacement of faulty components. |
|
Issues Identified |
---|
Issue 1:
The welding nozzle assembly exhibited signs of wear and tear, affecting the precision of the welding process.
Recommendations for further actions:
Establish a quarterly maintenance plan for all welding robotic arms, focusing on timely replacement of parts susceptible to wear and tear through maintenance inspections and identifying potential issues before they escalate.
|
Issue 2:
The motor drive unit showed irregularities in its performance, leading to occasional jerky movements of the robotic arm.
Recommendations for Further Action:
Implement a CMMS system to set a timely preventive maintenance schedule for the motor drive unit, including routine lubrication and monitoring for any unusual sounds or vibrations. This will minimise downtime and prevent major failures.
|
Conclusion |
---|
The maintenance activities performed on the robotic arm (Equipment ID: ARB-123456) have successfully addressed the identified issues. The recommendations are crucial for maintaining optimal performance and avoiding unplanned downtime in the welding section. Timely action is imperative to ensure the longevity and efficiency of the equipment. |
Attachments |
---|
|
Follow-Up |
---|
A follow-up meeting on January 10, 2024, at 2:00 PM to discuss any questions or concerns about the maintenance activities and recommendations outlined in this report. |