How does TPM drive innovation in Manufacturing Operations ?
May 13, 2024Since the advent of the First Industrial Revolution, the manufacturing industry has continually embraced innovation through technological advancements and process optimisation to meet evolving market demands. From the introduction of assembly lines to the adoption of automated robotics and IoT sensors, the manufacturing sector has thrived on the principles of adaptability and progress.
Within manufacturing operations, Total Productive Maintenance (TPM) has emerged as a catalyst for driving innovation, facilitating continuous improvement initiatives and operational excellence. With its foundation built on the eight pillars of TPM—Autonomous Maintenance, Planned Maintenance, Administrative & Office TPM, Quality Maintenance, Focused Improvement, Early Equipment Management, Training and Education, Safety, Health, and Environment (SHE)—TPM empowers organisations to optimise equipment reliability, streamline processes, and foster a culture of continuous improvement. This blog post will explore how TPM can drive manufacturing innovation and help businesses stay ahead in a constantly evolving technological landscape with changing consumer demands.
What is TPM in Manufacturing?
TPM, or Total Productive Maintenance in production and operations management, is a systematic approach to maximise the effectiveness of manufacturing equipment. Seiichi Nakajima, the father of TPM, developed the internationally accepted TPM benchmark in Japan between 1950 and 1970. TPM focuses on proactive and preventive maintenance, involving operators in the maintenance process to ensure equipment availability, reduce downtime, and enhance overall productivity. TPM aims to eliminate six big losses through activities such as autonomous maintenance, planned maintenance, and continuous improvement initiatives, fostering a culture of ownership and accountability among workers. Total Preventive Maintenance (TPM) is utilised interchangeably with Total Productive Maintenance, sharing the same acronym - TPM.
Understanding TPM Foundational Components
A comprehensive understanding of Total Productive Maintenance (TPM) begins with its foundation, which encompasses 5S and the Eight Pillars of Total Productive Maintenance. The 5S methodology focuses on organising the workplace, meanwhile, the eight pillars of TPM are essential for establishing and maintaining a proactive maintenance culture.
5S in TPM
In TPM, 5S is a vital component for workplace organisation and efficiency:
Sort: Eliminate unnecessary items and organise the workplace.
Set in Order: Arrange tools and materials in a systematic manner for easy access.
Shine: Regularly clean and maintain the workspace to ensure safety and functionality.
Standardise: Establish standardised procedures for maintaining cleanliness and organisation.
Sustain: Implement practices to sustain the improvements made through 5S, fostering a culture of continuous improvement.
8 pillars of Total Productive Maintenance(TPM)
Autonomous Maintenance (Jishu Hozen): Empowers operators to take responsibility for routine equipment care, including cleaning, inspection, and basic maintenance tasks, fostering a sense of ownership, making each operator a crucial part of the maintenance process.
Planned Maintenance (Keikaku-Hozen): Involves scheduling regular maintenance activities based on data-driven insights and equipment condition monitoring to prevent breakdowns and optimise maintenance efficiency.
Focused Improvement (Kobetsu Kaizen) : This TPM pillar focuses on problem-solving. It encourages cross-functional teams to identify and address root causes of equipment inefficiencies, implementing small-scale improvements continuously to enhance overall productivity.
Early Equipment Management (EEM): Focuses on optimising the design, installation, and commissioning of new equipment to ensure reliability, ease of maintenance, and alignment with production goals.
Quality Maintenance (Hinshitsu Hozen) : Integrating quality checks and inspections into the maintenance process aims to prevent defects and errors, ensuring consistent product quality and customer satisfaction.
Education and Training: Provide employees with the necessary skills and knowledge to operate, maintain, and improve equipment effectively, fostering a culture of continuous learning and development.
Administrative and Office TPM: Extends TPM principles to administrative and office environments, optimising processes, reducing waste, and improving overall efficiency beyond the shop floor.
Safety, Health, and Environment (SHE): This pillar of TPM is not just a priority; it's a responsibility. It emphasises safety, health, and environmental sustainability by implementing measures to prevent accidents, mitigate risks, and comply with regulations, ensuring a safe and sustainable work environment for all stakeholders.
What makes TPM significant in Industry 4.0?
In the landscape of Industry 4.0, characterised by the pervasive adoption of advanced technologies such as Artificial Intelligence (AI), robotics, and 3D printing, Total Productive Maintenance (TPM) emerges as a critical strategy for manufacturing competitiveness. TPM enhances equipment uptime and efficiency and is a vital framework for seamlessly integrating new technologies into existing production processes. For instance, TPM methodology can be tailored to ensure regular cleaning and maintenance of robots or 3D printers, mitigating the risk of contamination or pollution. Moreover, TPM facilitates effectively utilising data generated by Industrial Internet of Things (IIoT) sensors by providing structured analysis and actionable insights. This synergy between TPM and Industry 4.0 technologies empowers factories to optimise their operations, adapt to changing marketing trends, and maintain a competitive edge in the digital era.
Role of TPM in Driving Manufacturing Innovation
Innovation in the manufacturing industry is crucial for staying competitive and meeting evolving consumer demands. Total Productive Maintenance (TPM) drives manufacturing innovation by optimising equipment performance, empowering frontline workers, and promoting continuous improvement. Let's examine the role of TPM in boosting innovation in manufacturing sectors in detail.
Enhanced Equipment Reliability
TPM prevents breakdowns and extends equipment lifespan, ensuring continuous equipment operation.
By minimising unplanned downtime, TPM implementation can maximise production output.
Increased Productivity
The TPM method optimises equipment performance and reduces idle time, increasing production efficiency.
TPM fosters a proactive mindset, where maintenance is integrated seamlessly into operations.
Improved Quality
The TPM approach reduces defects and variability in product quality through proactive maintenance and process optimisation.
Manufacturers can consistently meet quality standards by adhering to TPM practices, leading to higher customer satisfaction and loyalty.
Empowered Workforce
TPM encourages the active involvement of operators in maintenance tasks, empowering them to take ownership of equipment reliability and contribute to ongoing process improvement.
Implementing TPM practices encourages collaboration and innovation at all levels of the organisation.
Cost Savings
Through proactive maintenance and effective asset management, TPM helps reduce maintenance costs and extends the lifespan of equipment, leading to substantial long-term cost savings.
TPM eliminates wasteful practices and promotes efficient resource utilisation.
How do you implement TPM in a Manufacturing Organisation?
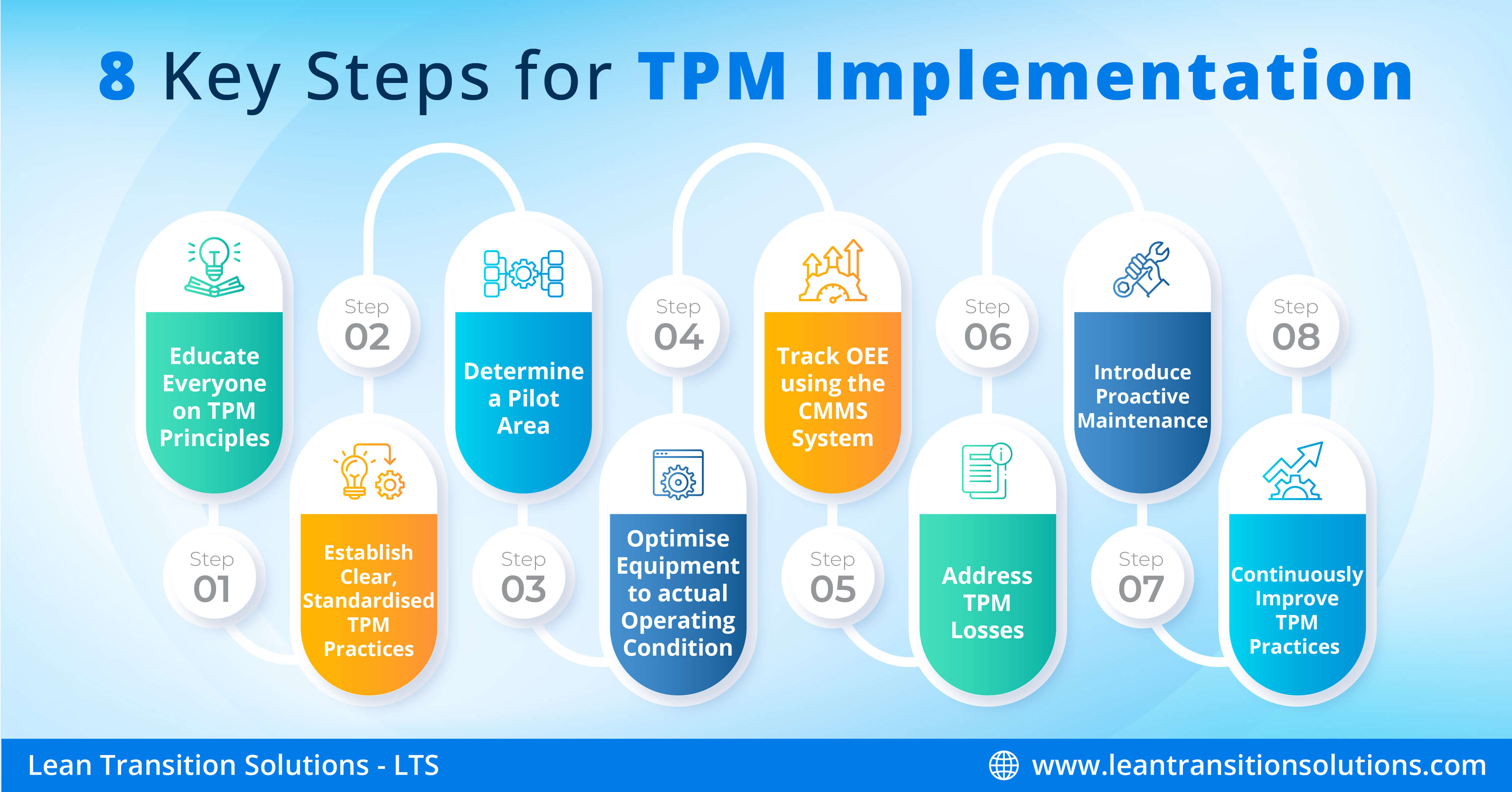
Implementing Total Productive Maintenance (TPM) in your manufacturing organisation can significantly enhance operational efficiency and equipment reliability. Each step is pivotal in laying a robust foundation for successful TPM implementation, ensuring sustainable improvements and fostering a culture of continuous enhancement.
8 Key Steps for TPM Implementation are:
Step 1: Educate Everyone on TPM Principles
To kickstart Total Productive Maintenance implementation, a comprehensive understanding of TPM principles among all stakeholders, from frontline operators to top management, is necessary. Conducting TPM training sessions helps align everyone with the core principles of TPM, fostering a shared vision and commitment towards improving Overall Equipment Effectiveness (OEE) and reducing downtime.
Step 2: Establish Clear, Standardised TPM Practices
Clarity and consistency are paramount when establishing Total Productive Maintenance (TPM) procedures and practices. Develop standardised protocols and guidelines, such as a TPM checklist and TPM template, that outline maintenance routines, operational standards, and performance metrics. This ensures uniformity across different departments and facilitates the seamless execution of TPM systems. By implementing these structured frameworks, organisations can effectively monitor equipment health, streamline workflows, and optimise productivity in line with the principles of TPM (Total Productive Maintenance).
Step 3: Determine a Pilot Area
Selecting a pilot area serves as a testbed for Total Productive Maintenance implementation, allowing organisations to refine strategies and address challenges on a small scale before total deployment. Choose an area with diverse equipment types and operational complexities to assess the applicability and effectiveness of Total Productive Maintenance principles across various scenarios.
Step 4: Optimise Equipment to actual Operating Condition
A cornerstone of TPM is restoring equipment to its optimal operating condition. Implement preventive maintenance schedules, conduct equipment inspections, and use predictive maintenance techniques to minimise breakdowns and maximise equipment uptime. Use TPM software solutions like CMMS (Computerised Maintenance Management System) to streamline maintenance activities and enhance equipment reliability.
Step 5: Track OEE using the CMMS system
Utilise lean TPM software solutions like Computerised Maintenance Management System (CMMS) to monitor and analyse Overall Equipment Effectiveness (OEE). CMMS software enables real-time tracking of equipment performance, downtime, productivity and maintenance metrics, empowering organisations to identify areas for improvement and prioritise corrective actions effectively.
Step 6: Address TPM Losses
Identify and address the six big losses in manufacturing—breakdowns, setup and adjustments, idling and minor stoppages, reduced speed, defects, and yield losses. Implement the lean TPM method to systematically eliminate waste and inefficiencies, optimise production processes, and enhance overall equipment effectiveness.
Step 7: Introduce Proactive Maintenance
Transitioning from reactive maintenance to proactive maintenance practices can help to prevent equipment failures and unplanned downtime. Implementing Predictive Maintenance (PM) techniques, like Condition Monitoring and Reliability-Centred Maintenance (RCM) using CMMS software, to anticipate potential issues and perform maintenance activities proactively, minimising disruptions to production schedules.
Step 8: Continuously Improve TPM Practices
TPM implementation is an ongoing journey of continuous improvement. Foster a culture of Kaizen (continuous improvement) within the organisation, encouraging employees at all levels to identify opportunities for enhancing TPM practices and driving operational excellence. Regularly review TPM performance metrics, solicit feedback from frontline operators, and continuously incorporate outcomes to refine and evolve the TPM approach.
5 Tips for successfully implementing TPM program in your Manufacturing Organisation
1. Leadership Commitment and Support: Ensure top management actively champions TPM, provides necessary resources, and demonstrates commitment through participation in TPM initiatives, fostering a culture of continuous improvement from the top down.
2. Employee Training and Empowerment: Invest in comprehensive TPM training programs to empower employees with the skills and knowledge needed for TPM implementation, fostering a sense of ownership and accountability among operators for equipment maintenance and improvement initiatives.
3. Cross-Functional Collaboration: Form cross-functional teams comprising members from various departments to collaborate on TPM projects, leveraging diverse perspectives and expertise to address maintenance challenges and drive innovation throughout the organisation.
4. Transparent Communication Channels: Establish clear communication channels to facilitate open dialogue between management and employees, encourage feedback exchange, and ensure alignment with TPM goals and objectives at all organisational levels.
5. Continuous Monitoring and Improvement: Implement robust monitoring systems like CMMS to track maintenance Key Performance Indicators (KPIs). This enables data-driven decision-making and continuous improvement in TPM practices to optimise equipment reliability and overall manufacturing efficiency.
TPM's Impact on Manufacturing Innovation: A Practical Example
A leading automotive manufacturer successfully applied Total Productive Maintenance (TPM) techniques to its assembly line, with a strong focus on autonomous maintenance and planned maintenance. The outcome was a significant reduction in unscheduled downtime, leading to increased machine availability and a boost in production output.
Before TPM implementation, the assembly line frequently experienced unplanned equipment breakdowns, leading to significant downtime and reduced Overall Equipment Effectiveness (OEE). However, after implementing TPM practices, the manufacturer observed a remarkable improvement in KPIs (Key Performance Indicators), as illustrated in the table below:
KPI | Before TPM Implementation | After TPM Implementation |
Equipment Downtime | 15 hours per week | 5 hours per week |
OEE | 65% | 85% |
Maintenance Cost | £50,000 | £30,000 |
The implementation of TPM has led to transformative change, promoting manufacturing innovation through a proactive maintenance culture and continuous improvement. The manufacturer witnessed a substantial reduction in downtime and a marked improvement in machine availability by empowering operators to perform autonomous maintenance tasks and implementing planned maintenance schedules.
This enhanced operational efficiency allowed the company to consistently meet production targets, respond quickly to market demands, and ultimately drive innovation in product development and manufacturing processes.
In this example of Total Productive Maintenance, the emphasis on preventive maintenance and optimisation of equipment performance directly contributed to increased productivity, cost savings, and overall competitiveness in the automotive industry.
As the manufacturing landscape undergoes continuous transformation, adopting TPM principles has become essential for igniting manufacturing innovation and attaining operational excellence. TPM enables organisations to optimise equipment reliability, enhance productivity, and reduce costs by prioritising proactive maintenance practices and fostering a continuous improvement culture.
By implementing TPM techniques such as autonomous maintenance, planned maintenance, and cross-functional collaboration, manufacturing companies can overcome challenges in operational processes and significantly minimise downtime.
However, the success of TPM largely depends on the commitment and involvement of leadership. By setting clear organisational goals and providing necessary resources, leaders can empower employees at all levels to contribute to process optimisation. By prioritising TPM, manufacturing businesses can optimise their operational efficiency and cultivate an environment where groundbreaking ideas flourish, propelling them to the forefront of innovation and success.