CMMS to Improve Safety and Risk Management
December 16, 2024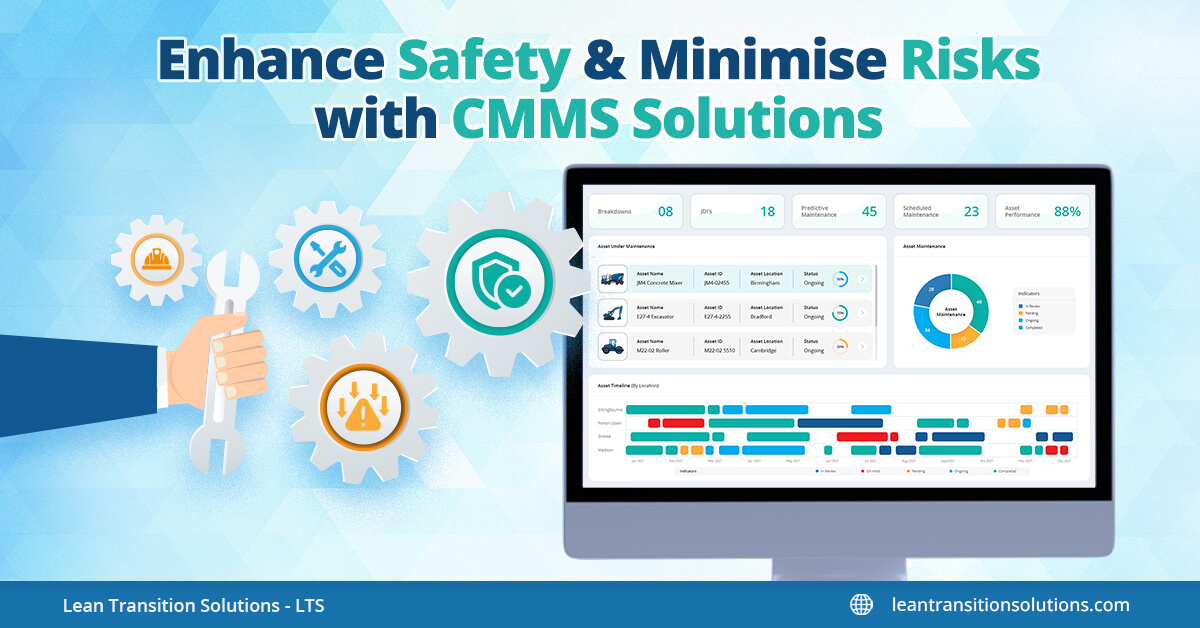
Think of an organisation managing a factory in which each screw, wire, and wheel are synchronised to be as smooth as possible while also being safe. Now, picture a sudden discord: One day, a machine misfires, safety alarms don’t work, and chaos breaks out. It’s like a small leak in a dam is ignored until water starts looking for another way to escape. Risk management is not a mere procedural formality; safety is fundamental to the way your business operates. This blog explores how to make safety not only a priority but a standard with the power of a Computerised Maintenance Management System (CMMS).
CMMS isn’t merely a tool—it’s the guardian of your operational safety. It transforms risk and safety management from reactive firefighting into a proactive, sustainable process. The key features of CMMS like detailed risk assessments, compliance tracking and automated alerts for inspections ensure that the risks are managed before they escalate. By enabling seamless tracking of audits and incidents, and real-time monitoring, it makes the organisational approach to safety from reactive to proactive.
What’s at Stake? The Hidden Costs of Overlooking Safety and Risks
Failing to adhere to safe practices and risk control procedures may be compared to constructing a home on weak ground; sooner or later, some flaws will be observed. The effects may concern different spheres of an organisation’s activity and create significant challenges which are given below.
Increased Downtime: Poor risk management and missed maintenance halt operations which leads to equipment failures and production losses.
Affect employee well-being and morale: When the workers perceive the workplace to be unsafe, it affects their willingness to stay with the organisation and productivity.
Operational inefficiencies: Unaddressed risks can lead to impacting equipment, cascading failures and resource allocation.
Regulatory Non-compliance: Failing to follow safety standards invites citations, and inspections and may lead to shut down from governing bodies.
Long-term Business Instability: Accidents and non-compliance have effects that reach far and compromise the long-term viability and put off investors and stakeholders.
Smart Maintenance: CMMS, your safety guardian
Yes, CMMS elevates safety to a priority level with its features tailored for risk mitigation.
Understand those features which ensure a safer workplace.
Preventive Maintenance Scheduling: Safety First, Always
Real-Time Alerts: Your Risk Radar
- Asset Tracking: Knowing the Risks at All Times
Incident Reporting: Learn and Adapt
Safety Inspection Checklists: Your Digital Protocol Manager
CMMS reduces hazardous breakdown by automating preventive maintenance that ensures equipment operates at peak efficiency. It mitigates the risks before they arise by keeping critical systems in check and generating systematic schedules.
If any issues or abnormalities arise, CMMS sends notifications to specific teams to address these issues in real-time. This form of instant communication helps prevent the development of possible threats.
Asset tracking, one of the major features of CMMS tracks the condition of all critical assets. It monitors wear and tear, schedules replacements, and guarantees that such equipment is either fixed or replaced to prevent it from becoming a risk factor to the organisation.
Through real-time incident reporting and historical analysis, CMMS integrates the data into analysis. This helps to determine the patterns and improvements needed to take in safety policies.
An effective CMMS software provides customisable safety checklists and built-in inspection templates. These tools eliminate the possibility of overlooking certain compliance requirements, making audits very smooth.
How to Build a Safety-First Culture with CMMS?
The creation of the safety-first culture in the organisational context is implemented from three aspects, including the leadership, employees, and technology. This kind of system evolution can be supported by a CMMS which offers solutions for a systematic approach to managing, engaging and improving. Here’s a step-by-step approach to achieving this.
1. Leadership: Setting the Tone for Safety
Develop a clear strategy by integrating maintenance and safety.
Choose a CMMS system suitable to the organisation’s requirements
Provide enough resources for the system application and personnel training.
Demonstrate the impact of CMMS on organisational safety.
2. Training: Empowering Your Workforce
Navigate CMMS features like asset tracking, safety inspections, and compliance management.
Include drills and simulations, using details from the CMMS to prevent hazards.
Use the system’s reporting tools and make improvements.
3. Technology Integration: Making Safety a Priority with CMMS
Asset Inventory: Uploads all-important asset information to the CMMS or classifies them according to risk and maintenance requirements.
Schedule Safety Checks: Automate routine activities like inspections, compliance audits, and emergency drills.
Data Centralisation: Integrate maintenance history and incidents in the CMMS to provide a unified view of risks.
Customise Dashboards: Set up dashboards for constant tracking of safety metrics and Key Performance Indicators (KPIs).
Safety Protocol Integration: Link safety checklists directly to work orders
4. Fostering a Long-Term Safety Culture
Continuous Improvement: Leverage the analytical nature of CMMS to improve aspects of safety management continually, drawing from data.
Employee Engagement: Encourage the teams to focus on accomplishing the safety objectives recorded in the CMMS to foster motivation and morale amongst the teams.
The Holistic Approach of CMMS to Risk Management
Maintenance is a field which involves the management of risks. It is associated with employees or machines and is one of the key performance indicators taken into consideration. Even though safety risks are essential in plant operational activities the maintenance manager needs to take charge of other risks that may affect the operation’s efficiency, profitability or longevity of an organisation. These risks may be inherent in operations, stemming from manufacturing issues, unplanned failures, equipment breakdowns, regulation violations, and even company financial problems. If these risks are not managed adequately, they result in excessive maintenance costs, production delays, and even environmental harm.
Let's understand the risks associated with the organisation and the solutions provided by the CMMS to mitigate them.
Unexpected breakdowns due to lack of proactive maintenance.
CMMS solution: Predictive maintenance tools schedule repairs before a failure occurs, analyse asset data and minimise costly repairs and downtime.Financial risks due to unexpected costs from inefficient maintenance practices
CMMS solution: Tools used for tracking the budget and cost growth allow an analysis of expenditures for the maintenance of the company and keeping the costs in the appropriate scope.Compliance and regulatory risks
CMMS solution: Scheduling and reporting made automatic, guarantees compliance with regulatory requirements for maintenance processes which avoids expensive fines.Stock outs or excess inventory cause Inventory and Supply chain risks
CMMS solution: Inventory management features of CMMS optimise material usage, monitor tracks, trigger restocks and ensure timely maintenance.Resource Allocation & Labour Management Risks due to poor resource planning
CMMS solution: Automated task scheduling features of CMMS illustrate the right needful tools and the right available people. It also reduces workload blockages by optimising labour.
Titan CMMS: The non-negotiable tool for Safety and Risk management
Meeting potential risks is inherent in factories, offices and other workplaces – but being unprepared isn’t. A CMMS has all the functions your organisation needs for effectively assessing, controlling, and mitigating risks. It closes the loop on vulnerabilities and highlights safety as a core organisational culture.
Titan CMMS, the control maintenance management system software of LTS, is the right tool for transforming your maintenance strategy into a proactive, risk-reducing powerhouse. It keeps the workplace compliant and safe through its key features which are given below.
Titan CMMS Features for Safety and Risk Management
* Automated Maintenance Scheduling
* Real-Time Alerts
* Compliance Management
* Mobile Accessibility
* Preventive and Predictive maintenance
* Asset Condition Monitoring
* Inventory and Parts Management
* Risk Assessment and Mitigation Tools
By implementing Titan CMMS, it is possible to optimise all maintenance operations and minimise organisational risks. Request a demo of Titan CMMS now and oversee your safety measures, compliance, and productivity.
FAQs
1. How does CMMS enhance organisational safety?
A Computerised Maintenance Management System (CMMS) enhances organisational safety by improving maintenance scheduling, identifying hazards, tracking equipment, managing inventory, monitoring safety issues and meeting regulatory requirements.
2. What is the risk-based maintenance framework?
Risk-based maintenance framework is a methodology that works on identifying the risk of failure of assets and its failure modes to generate a maintenance plan that aims to reduce risks.
3. What is TPM in risk management?
In maintenance, TPM is the acronym for Total Productive Maintenance which is an approach to attain perfect production with no defects, no breakdowns and no accidents. TPM focus on preventive and proactive maintenance.
4. What is an example of risk-based maintenance?
A general example of risk-based maintenance is servicing high-risk machinery based on its failure probability and impact.
5. What is safety preventive maintenance?
Safety preventive maintenance can be defined as the process of systematically keeping track of potential safety risks in the assets and equipment for the purpose of preventing accidents and subsequent injuries.