How to improve Production Efficiency in your Manufacturing Industry?
August 2, 2023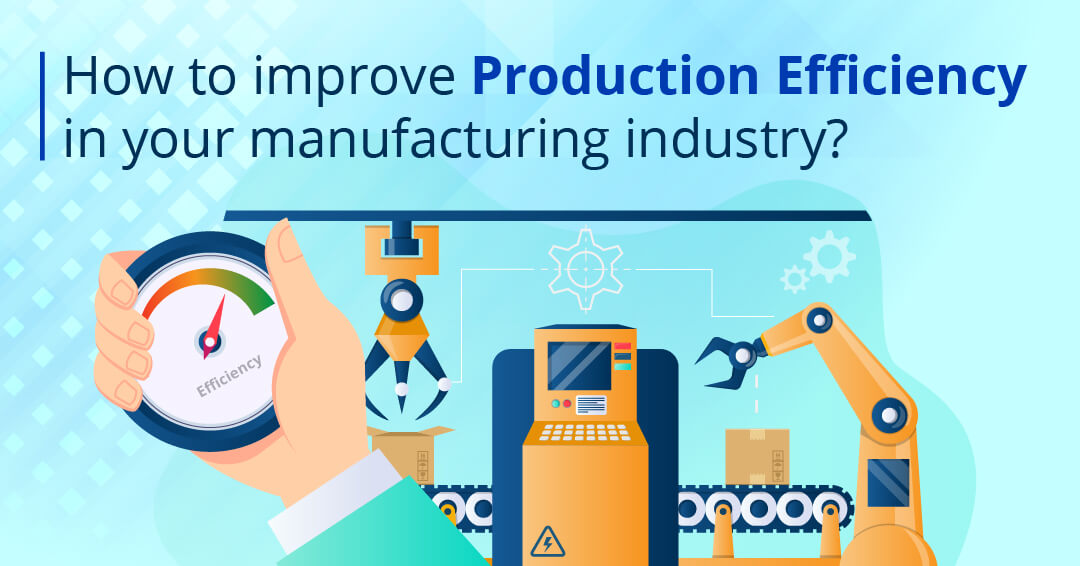
Streamlining production processes is crucial for delivering high-quality products on time, exceeding customer expectations, and gaining a competitive edge. To achieve this, manufacturers must continuously improve their operations and optimise production processes. This can be done through automation, advanced analytics, and digitalisation.
Let’s see how to enhance production efficiency for your organisation in 8 simple steps.
What is Production Efficiency?
Production efficiency refers to how well resources, such as raw materials, labour, and technology, are utilised to produce goods or services with minimal waste and maximum output.
It forms a critical aspect of manufacturing processes as it directly impacts a company's cost-effectiveness, competitiveness, and profitability. The goal is to produce goods or deliver services in a timely, cost-effective, and sustainable manner, meeting the quality standards and customer demands.
Key aspects of Production Efficiency
- Resource Management: Efficiently using raw materials, energy, and human resources to avoid unnecessary waste and costs.
- Technology and Automation: Implementing modern technologies to streamline production processes, reduce errors, and increase productivity.
- Workflow and Process Design: Analysing and redesigning workflows and processes to eliminate bottlenecks and optimise production flow.
- Lean Manufacturing Principles: Adopting principles such as reducing waste, Just-in-Time manufacturing (JIT), and continuous improvement to enhance efficiency.
- Total Productive Maintenance (TPM): Ensuring equipment reliability and minimising downtime through proactive maintenance strategies. Organisations use CMMS as a comprehensive solution for maintenance to manage their maintenance schedules efficiently.
- Data Analytics: Collecting and analysing production data to identify inefficiencies, make informed decisions, and drive improvements.
- Employee Involvement: Encouraging a culture of continuous improvement and involving employees in identifying and implementing efficiency-enhancing ideas.
8 easy steps to improve Production Efficiency
Step 1: Conduct a comprehensive Production Audit
Conducting a comprehensive production audit is important if you aim to improve production efficiency. This audit can offer valuable insights into the current state of production processes, allowing businesses to pinpoint improvement areas.
- Identifying Bottlenecks: Reviewing the entire production process helps to identify bottlenecks where workflow gets obstructed, leading to delays and inefficiencies. By pinpointing these bottlenecks, businesses can prioritise areas that need immediate attention and rectification.
- Data Collection and Analysis: The production audit relies heavily on data collection, gathering information about production output, cycle times, downtime occurrences, and resource consumption. Businesses can use advanced data analytics tools to gain valuable insights from this data, facilitating data-driven decision-making in subsequent stages of the improvement process.
- Key Performance Indicators (KPIs): During the audit, relevant KPIs such as Overall Equipment Efficiency (OEE), Production yield, Cycle time, and Inventory Turnover are measured and analysed to gauge current performance levels.
Step 2: Streamline Workflows and Processes
With the insights gained from the production audit, streamlining workflows and processes is the next step. By optimising tasks and ensuring a smooth production flow, businesses can reduce lead times, minimise waste, and enhance overall productivity.
- Implementing Lean Manufacturing Principles: Embracing Lean Manufacturing principles can revolutionise the production process. Businesses can eliminate unnecessary steps, reduce inventory levels, and create a more agile and efficient production environment by focusing on continuous improvement, waste reduction, and value maximisation.
- Eliminating Non-Value-Adding Activities: During the process of streamlining, it is vital to identify and eliminate non-value-adding activities that consume time and resources but do not contribute to the final product's quality or customer satisfaction. By doing so, businesses can redirect their efforts and resources towards more meaningful and impactful tasks.
Step 3: Invest in Automation and Technology
In today's rapidly evolving business landscape, embracing automation and cutting-edge technology is essential to achieve optimal production efficiency. By integrating technology-driven solutions, businesses can unlock new productivity, accuracy, and competitiveness levels.
- Automation and Robotics: Incorporating automation and robotics into production processes can reduce manual labour, eliminate human errors, and increase production speed. Robotic systems can handle repetitive tasks precisely, allowing skilled workers to focus on more complex and value-adding activities. This not only enhances efficiency but also improves the overall workplace safety.
- Digitalisation of Processes: Digitising production processes enables seamless data capture, analysis, and information flow. By transitioning from paper-based to digital workflows, businesses can streamline operations, reduce paperwork, and enhance data accessibility. Digitalisation also facilitates better coordination between teams and enables real-time tracking of production metrics.
Step 4: Workforce Optimisation
While technology and automation play a crucial role in improving production efficiency, the significance of an empowered and skilled workforce cannot be overlooked. Optimising the workforce involves nurturing a culture of continuous improvement, enhancing collaboration, and recognising employee contributions.
- Training and Skill Development: Investing in training and skill development programs ensures that employees have the knowledge and expertise to operate new technologies and adapt to changing production processes. By empowering the workforce with up-to-date skills, businesses can improve productivity, reduce errors, and foster a sense of competence and confidence among employees.
- Teamwork and Communication Enhancement: Strengthening teamwork and communication within the organisation is essential for smooth production processes. By promoting open communication channels, cross-functional collaboration, and shared goals, businesses can break down silos and ensure the entire workforce is aligned towards achieving production efficiency targets.
Step 5: Supply Chain Integration
To further enhance production efficiency, businesses must integrate their supply chain seamlessly. A well-integrated supply chain ensures timely availability of raw materials, reduces lead times, and improves overall production effectiveness.
- Collaboration with Suppliers: Building strong collaborative relationships with suppliers is crucial for a smooth supply chain operation. By working closely with suppliers and sharing information, businesses can anticipate potential disruptions, negotiate favourable terms, and ensure a reliable and efficient supply of raw materials.
- Demand Forecasting and Inventory Planning: Utilising data-driven demand forecasting techniques helps businesses accurately predict customer demands. By aligning production schedules with forecasted demands, companies can optimise inventory levels, reduce excess stock, and prevent stockouts, resulting in streamlined production and improved customer satisfaction.
- Vendor Managed Inventory (VMI): Adopting Vendor Managed Inventory allows suppliers to take responsibility for monitoring and replenishing inventory levels. This approach eliminates manual inventory management, reduces lead times, and ensures that businesses always have the required materials, optimising production schedules.
Step 6: Quality Control and Assurance
Maintaining high-quality standards is essential to ensure that production efficiency efforts result in products that meet or exceed customer expectations. Quality control and assurance measures help identify and rectify defects, minimise waste, and enhance overall product reliability.
- Total Quality Management (TQM): Total Quality Management involves every level of the organisation continuously seeking quality improvement. By promoting a customer-centric culture, empowering employees, and focusing on continuous improvement, TQM ensures that quality becomes ingrained in all aspects of the production process.
- Six Sigma Methodology: Six Sigma aims to reduce defects and variations in production processes. By applying statistical analysis and problem-solving techniques, Six Sigma identifies the root causes of defects and drives process improvements, significantly reducing defects and enhancing overall quality.
- Statistical Process Control (SPC): Statistical Process Control uses statistical methods to monitor and control production processes. By collecting and analysing process data, SPC enables businesses to identify real-time variations and deviations from quality standards. This proactive approach allows for timely corrective actions and prevents defects from occurring.
- Error Prevention Techniques: Implementing error prevention techniques such as Poka-Yoke (Mistake-Proofing) and FMEA (Failure Mode and Effects Analysis) can prevent errors and defects during production. By designing processes and systems to be inherently error-resistant, businesses can minimise the likelihood of defects and enhance overall product quality.
Step 7: Regular Maintenance and Calibration
To ensure sustained production efficiency, businesses must prioritise regular maintenance and calibration of equipment and machinery. Neglecting maintenance can lead to unexpected breakdowns, increased downtime, and compromised product quality. CMMS (Computerised Maintenance Management System) can help in regular maintenance activities by providing a centralised platform for scheduling, tracking, and managing maintenance tasks, enabling timely inspections, preventive maintenance, and efficient resource allocation.
- Regular Equipment Maintenance: Implementing a well-defined maintenance schedule for all equipment and machinery is crucial. Regular maintenance activities, such as cleaning, lubrication, and parts replacement, help prevent premature wear and breakdowns, ensuring the equipment operates at peak performance levels. CMMS helps with equipment maintenance by facilitating regular inspections and data logging, enabling the identification of wear and tear patterns and potential equipment breakdowns through asset vibrations or heat generation.
- Predictive Maintenance Practices (PM): Adopting Predictive Maintenance practices involves using data analytics and IoT sensors to monitor real-time equipment conditions. By predicting potential failures and addressing them proactively, businesses can schedule maintenance when needed, avoiding unplanned downtime and optimising production efficiency. By utilising the data collected, CMMS can trigger preventive maintenance actions, reducing unplanned downtime and extending the lifespan of critical equipment.
- Ensuring Equipment and Machinery are Properly Calibrated: Proper calibration of equipment and machinery is essential to maintain accuracy and consistency in production processes. Regularly calibrating instruments and machines guarantees optimal performance, minimising variations and defects in the final product.
- Asset Performance Management (APM): Asset Performance Management involves leveraging technology to monitor equipment performance, identify potential issues, and optimise asset life cycles. APM enables businesses to make data-driven decisions about maintenance and replacement, maximising the efficiency and lifespan of critical assets. A crucial part of managing asset performance involves utilising a CMMS, which functions as a thorough database of asset information such as maintenance history, downtime records, and maintenance schedules.
- Scheduling Maintenance to Minimise Downtime: Strategic planning of maintenance activities is essential to minimise downtime and disruptions to production. By scheduling maintenance during planned downtime or periods of low production demand, businesses can maintain a consistent workflow and avoid significant production losses. CMMS can be valuable software in scheduled maintenance activities as it enables businesses to create and manage maintenance schedules, ensuring that tasks are allocated and performed at the most reasonable times, minimising disruptions to production.
Step 8: Continuous Improvement Culture
Fostering a culture of continuous improvement is fundamental to sustaining and enhancing production efficiency. A culture that encourages innovation, learning, and feedback empowers employees to contribute to the organisation's success.
- Kaizen Philosophy: Embracing the Kaizen philosophy involves incremental improvements in all aspects of the production process. Encouraging small, continuous changes and involving employees at all levels in the improvement process creates a sense of ownership, leading to a more efficient and innovative workplace.
- Encouraging Feedback and Suggestions: It is essential to establish channels for employees to share their feedback, suggestions, and ideas for process improvement. By valuing and implementing employee contributions, businesses tap into their workforce's collective knowledge and creativity, leading to innovative solutions and enhanced efficiency.
Measuring Production Efficiency
Measuring production efficiency can be achieved through the Overall Equipment Efficiency (OEE) score, which quantifies the effectiveness of a manufacturing process.
OEE is calculated as a percentage and takes into account three key factors:
- Availability (the percentage of scheduled time the equipment is operational).
- Performance (the speed at which the equipment runs compared to its maximum speed)
- Quality (the percentage of defect-free products produced)
According to OEE measures, sound production is indicated by a score close to 100%. A 60-80% score is considered efficient in manufacturing processes. It signifies that the production process runs at peak performance, with minimal downtime, optimal speed, and high-quality output.
By continuously monitoring and striving to improve OEE, businesses can ensure efficient utilisation of resources, maximise productivity, and achieve excellence in production.
As consumer demands evolve and market dynamics shift rapidly, companies must continuously find ways to improve their processes and operations. The comprehensive approach of integrating production audits, process streamlining, technology adoption, and workforce optimisation empowers businesses to adapt, innovate, and maintain a competitive edge.
Moreover, production efficiency translates into tangible benefits such as cost savings, increased output, shorter lead times, and improved product quality, directly contributing to higher customer satisfaction and loyalty.
By prioritising production efficiency as a core business objective, companies can embark on a path of continuous growth and prosperity, solidifying their position as industry leaders and delivering value to customers and stakeholders.