How to choose the right Asset Maintenance Strategy?
March 26, 2024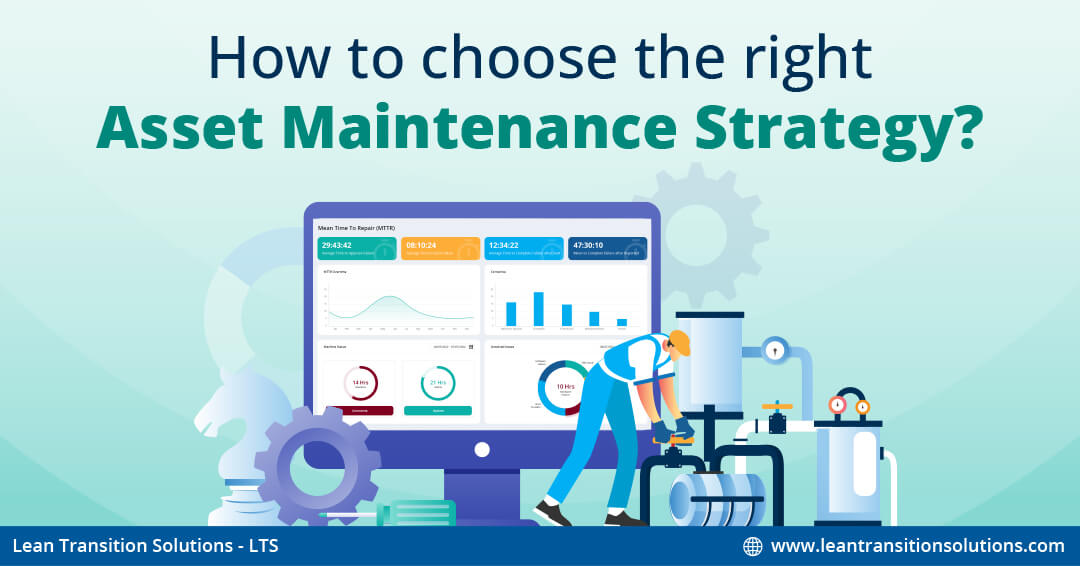
It's no surprise when the maintenance costs bother you, even when you're committed to selecting the best strategies for your assets. The maintenance world can offer you various maintenance practices, but finding the perfect maintenance strategy feels like searching for a needle in a haystack. Manufacturers continually strive to minimise maintenance costs and ensure workplace safety while maximising asset efficiency.
You may have reached here while navigating the maze of countless asset maintenance strategies available in the industry. Don't worry. By the end of this exploration, you will have your answers! Let's unlock the secrets to achieving cost-effective maintenance practices without compromising performance or safety.
What is a Maintenance Strategy?
A maintenance strategy is a systematic approach businesses adopt to manage the upkeep, repair, and optimise their assets, equipment, and infrastructure. It involves deploying specific maintenance techniques, schedules, and methodologies to maximise asset reliability, minimise downtime, and extend operational lifespans.
Different types of Maintenance Strategies adopted in industries
Maintenance strategies encompass a variety of approaches, including:
Reactive Maintenance: While reactive maintenance can be cost-effective in the short term, it often leads to unplanned downtime, higher repair costs, and decreased productivity. Reactive maintenance addresses maintenance issues when equipment or assets fail or malfunction. Various approaches to reactive maintenance include:
Breakdown Maintenance: A reactive approach to repairing equipment post-failure, aimed at minimising downtime and prioritising urgent repairs.
Run to Failure Maintenance: Operating equipment until failure, relying on monitoring for replacements or repairs to optimise cost savings.
Corrective Maintenance: Addressing identified issues and failures after a malfunction and ensuring equipment functionality and safety.
Emergency Maintenance: Immediate response to critical failures, prioritising safety and operational continuity while minimising downtime.
Preventive Maintenance: In contrast to reactive maintenance, preventive maintenance involves scheduled inspections, servicing, and repairs to prevent equipment failures before they occur. By proactively addressing and identifying potential issues, businesses can minimise disruptions to operations and optimise asset performance.
Predictive Maintenance: Predictive maintenance relies on data analytics, IoT sensors, and monitoring systems to predict equipment failures based on patterns and trends. By analysing real-time data and performance metrics, businesses can anticipate maintenance needs, schedule interventions strategically, and avoid costly downtime.
Condition-Based Maintenance (CBM): Similar to predictive maintenance, condition-based maintenance involves monitoring equipment conditions and performance indicators to determine maintenance requirements. By assessing factors such as temperature, vibration, and lubrication levels, businesses can tailor maintenance activities to specific asset conditions, optimising efficiency and reliability.
Reliability-Centred Maintenance (RCM): Reliability-Centred Maintenance is a comprehensive approach that prioritises maintenance activities based on the criticality and consequences of asset failures. Businesses can optimise resource allocation, enhance asset reliability, and minimise operational disruptions by identifying failure modes, analysing risks, and implementing targeted maintenance strategies.
Benefits of having a good Maintenance Strategy
Implementing an effective maintenance strategy offers several advantages for your business.
Improved Asset Reliability: By implementing proactive maintenance practices, businesses can enhance asset reliability, minimise unplanned downtime, and maximise operational availability.
Cost Reduction: Optimal maintenance strategies help businesses reduce repair costs, extend asset lifespans, and minimise the need for costly emergency repairs.
Enhanced Safety: Regular maintenance activities ensure equipment operates safely and complies with regulatory standards, minimising the risk of accidents, injuries, and environmental hazards.
Increased Productivity: By minimising downtime and optimising asset performance, businesses can enhance productivity, meet production targets, and maintain a competitive edge.
Strategic Resource Allocation: Maintenance strategies enable businesses to allocate resources effectively, prioritise critical assets, and optimise maintenance schedules based on operational needs and business objectives.
Factors influencing Maintenance Strategy selection
Asset Criticality and Importance: Assessing the significance of assets to operations, prioritising maintenance strategies accordingly to minimise disruptions and maximise productivity.
Maintenance Cost Considerations: Evaluating the financial implications of different maintenance approaches, balancing expenses with the need for reliable equipment performance.
Regulatory Compliance Requirements: Adhering to industry regulations and standards, ensuring that maintenance strategies meet legal obligations and safety protocols.
Maintenance Complexity and Age: Consider the complexity of maintenance and age of equipment while selecting a maintenance strategy. Choose tailored approaches to address the maintenance needs and challenges of your specific assets.
Operational Environment and Conditions: Recognising the unique operational environment and conditions in which equipment operates, adapting maintenance strategies to optimise performance and longevity while minimising risks.
Assessing Maintenance Strategies for Right Selection
Maintenance Strategy | Cons | Pros | Suitable Applications |
Reactive Maintenance | Immediate response to equipment or asset failures | Higher risk of unplanned downtime | - Non-critical equipment - Low-cost assets with minimal impact on shop floor operations |
Preventive Maintenance | Time-Based or Scheduled Maintenance strategies to reduce unexpected failures | May lead to unnecessary maintenance costs or maintenance activities | Equipment with predictable failure patterns and critical assets requiring consistent operational performance. |
Predictive Maintenance | Utilises data-driven insights to anticipate failures | Requires sophisticated monitoring assets or equipment and data analysis tools | Complex machinery with identifiable failure precursors and assets where downtime is costly |
Condition-Based Maintenance | Maintenance triggered by equipment condition parameters | Relies on accurate monitoring systems or sensors | Assets with clear indicators of deterioration and equipment prone to wear and tear |
Reliability- Centred Maintenance | Focuses on critical assets and optimises maintenance efforts | Requires thorough analysis and planning; initial implementation may be time-consuming | - High-value assets with complex systems - Industries where downtime is costly |
Key Considerations in Maintenance Strategy Selection
Asset Performance History and Data Availability
Evaluate historical performance data and maintenance records to identify recurring issues and failure trends.
Assess the availability and reliability of data sources, including equipment logs, sensor readings, and maintenance reports.
Utilise historical data to inform predictive maintenance strategies and optimise resource allocation.
Equipment Failure Modes and Patterns
Conduct a comprehensive analysis of equipment failure modes and patterns to identify underlying causes and vulnerabilities.
Determine the likelihood and impact of different failure scenarios on operational continuity and productivity.
Tailor maintenance strategies to address specific failure modes and mitigate associated risks effectively.
Maintenance Team Skills and Expertise
Assess the skill sets, qualifications, and experience levels of maintenance personnel responsible for executing maintenance tasks.
Provide the necessary training and professional skill development opportunities to enhance technical competencies and problem-solving capabilities.
Ensure maintenance teams have the knowledge and resources to implement selected maintenance strategies effectively.
Technology and Tools for Maintenance Monitoring and Analysis
Evaluate the availability and adaptability of Computerised Maintenance Management System (CMMS) software for maintenance monitoring and analysis.
Leverage CMMS software capabilities for asset tracking, work order management, preventive maintenance scheduling, and performance analysis.
Integrate CMMS software with other enterprise systems to streamline data management and facilitate decision-making processes.
Integration with Asset Management Systems
Ensure alignment between maintenance strategies and broader asset management objectives and practices.
Utilise CMMS systems to facilitate seamless integration with asset management systems, enabling holistic asset lifecycle management.
CMMS software tracks asset performance, monitors maintenance activities, and optimises asset utilisation and reliability.
Maintenance Strategy Example
Let's consider the Maintenance Strategy Implementation example in a Marine Vessel.
By implementing these maintenance strategies, marine vessels can optimise asset reliability, minimise downtime, ensure regulatory compliance, and enhance operational efficiency and safety at sea.
Assessment of Equipment and Assets
Conduct comprehensive assessments of critical assets onboard, including engines, propulsion systems, and safety equipment.
Identify Key Performance Indicators (KPIs) such as engine hours and fuel consumption rates for performance tracking.
Preventive Maintenance Schedules
Develop preventive maintenance schedules based on manufacturer recommendations and regulatory standards.
Schedule routine inspections and component replacements to prevent equipment failures and ensure safety compliance.
Integration of Condition Monitoring Technologies
Integrate condition monitoring technologies like vibration analysis and thermal imaging to detect equipment degradation early.
Implement real-time monitoring systems for proactive maintenance during vessel operations.
Utilisation of Computerised Maintenance Management Systems (CMMS)
Implement CMMS to streamline maintenance workflows and track maintenance history.
Use CMMS to schedule tasks, allocate resources efficiently, and ensure regulatory compliance.
Training and Development of Maintenance Personnel
Provide specialised training for maintenance personnel on marine-specific practices and safety protocols.
Foster a culture of safety awareness and proactive maintenance through regular training sessions
Implementation of Spare Parts Management Strategies
Establish inventory management systems to track spare parts and critical components.
Maintain adequate stock levels and establish supply chain partnerships for timely procurement.
Continuous Improvement and Performance Monitoring
Regularly review maintenance performance metrics and KPIs for improvement opportunities.
Conduct post-maintenance reviews and root cause analyses to address equipment failures effectively.
As manufacturers navigate the complexities of asset management, selecting the right maintenance strategy emerges as a critical determinant of long-term success and asset upkeep. By evaluating and optimising maintenance practices, businesses can mitigate risks, enhance reliability, and drive sustainable growth in today's competitive landscape.
If manufacturers go ahead with their maintenance plans without a proper solution to manage the diverse needs of their critical assets, it can be challenging at times. By integrating CMMS as an all-in-one solution, manufacturers can streamline maintenance workflows, track performance metrics, and foster a culture of continuous improvement practices.
With the right maintenance strategy and powerful tools like CMMS, the path of sustainable growth, resilience, and success in the maintenance operations of your assets is within reach!