What is Machine Maintenance and Why is it important?
April 12, 2024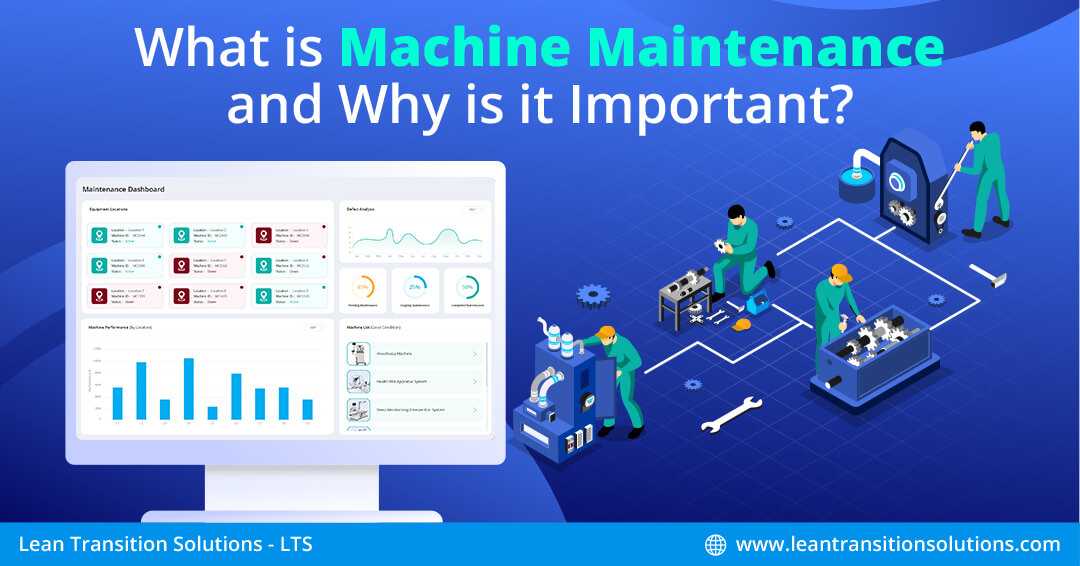
Adopting a digital maintenance management system is more than just solving your maintenance issues; it's about redefining your maintenance practices to ensure optimal equipment performance. Effective maintenance practices are the backbone of every successful shop floor operation in various industries, from ensuring uptime and productivity to extending equipment lifespan and preventing costly breakdowns.
In this blog, let's discuss the importance of machine maintenance, explore its impact on operational efficiency, and uncover the key strategies maintenance experts adopt to optimise maintenance processes to keep your shop floor operations running like a clock!
What is Machine Maintenance?
Machine maintenance is the systematic process of ensuring that industrial machinery and equipment remain in optimal condition to achieve continuous operational performance and efficiency. It involves a range of preventive measures, such as regular inspections, cleaning, lubrication, and replacement or repair of worn-out parts, aimed at preventing breakdowns, extending equipment lifespan, and minimising downtime. By adhering to maintenance schedules and implementing appropriate maintenance procedures, organisations can enhance safety, optimise machine performance, reduce costs, increase uptime and ensure regulatory compliance in industrial operations.
Why is Machine Maintenance important?
Executing machine maintenance using industrial machine maintenance software improves efficiency and productivity, which leads to business success. But why exactly is machine maintenance so important? Let's explore the key benefits of machine maintenance below:
Preventing Machine Breakdowns: Regular machine maintenance using a machine maintenance software helps identify and address potential maintenance issues before they escalate into costly breakdowns, hence minimising downtime and managing production interruptions.
Extending Equipment Lifespan: Proper maintenance practices, such as lubrication, cleaning, and spare part replacements, can be effectively managed using equipment maintenance tracking software. A Machine maintenance management system can significantly extend a machine's lifespan, maximising its Return on Investment (ROI) and reducing the need for frequent replacements.
Ensuring Safety: Well-maintained machines are less likely to malfunction or pose safety hazards to operators, reducing the risk of workplace accidents and injuries.
Optimising Performance: Maintenance tasks, such as calibration and alignment, ensure machines operate at peak performance levels, delivering consistent operation and quality.
Cost Savings: Investing in preventive maintenance offered by a machine shop maintenance software is often more cost-effective than reactive repairs, as it helps avoid expensive emergency repairs and spare part replacements.
Regulatory Compliance: Many industries are subjected to regulations and Standard Operating Procedures (SOPs) governing equipment maintenance and safety. Adhering to these requirements through regular maintenance using an equipment maintenance tracking app ensures compliance and mitigates maintenance risks.
Environmental Impact: Efficiently maintained machines using a machine maintenance system consume less energy, produce fewer emissions, and minimise bottlenecks, which reduces waste, contributing to environmental sustainability and reducing carbon footprint.
Customer Satisfaction: Machine reliability leads to consistent product quality and timely delivery, enhancing customer satisfaction, reputation building and loyalty.
Types of Machine Maintenance
Various machine maintenance strategies are employed to ensure smooth functioning and equipment longevity. These strategies range from reactive approaches to proactive methodologies aimed at preventing issues before they occur.
Each type of machine maintenance strategy offers unique benefits and challenges, and selecting the most suitable approach depends on factors such as equipment criticality, operational requirements, and available resources. Let's explore the different types of machine maintenance and their significance in optimising operational efficiency, increasing uptime and minimising downtime.
Reactive Maintenance: Reactive maintenance, or breakdown maintenance, involves repairing equipment to standard operating conditions only when maintenance issues arise. This often results in unplanned downtime and higher repair costs.
Run-to-fail Maintenance: In this strategy, machines are operated until they fail or stop working completely, with no proactive maintenance performed in advance. It's typically employed for non-critical equipment where downtime is acceptable and repair costs are lower than preventive maintenance expenses.
Routine Maintenance: Routine maintenance involves regular, scheduled inspections, cleaning, and lubrication to keep machinery operating smoothly. It helps identify potential issues early and prevents unexpected breakdowns.
Corrective Maintenance: Corrective maintenance is performed in response to identified faults or failures, aiming to restore equipment to its normal operating condition. Though proper planning is required to minimise downtime and operational disruptions, corrective maintenance is performed only after the equipment fails or breaks down.
Preventive Maintenance: This proactive approach involves scheduled maintenance tasks performed at intervals to prevent equipment failures. It includes time-based preventive maintenance, where tasks are performed based on predetermined time intervals, and usage-based preventive maintenance, where equipment usage metrics trigger machine maintenance.
Condition-based maintenance: Condition-based maintenance relies on real-time equipment condition monitoring through sensors and other tools. Maintenance tasks are performed based on the actual condition of the machine, optimising maintenance schedules and reducing unnecessary downtime.
Predictive Maintenance: Predictive maintenance utilises data analytics and machine learning algorithms to predict equipment failures before they occur. By analysing historical data and equipment performance metrics, maintenance tasks are scheduled and executed promptly, minimising downtime or repair costs.
Prescriptive maintenance: Prescriptive maintenance not only predicts equipment failures but also recommends specific actions to mitigate or prevent them. It utilises advanced analytics and AI-driven insights to provide actionable recommendations for optimising maintenance strategies and improving overall equipment reliability.
Ways to improve Machine Maintenance and Uptime
Improving machine maintenance using a heavy equipment management system in your industry requires attention to four key areas: planning, protection, precision, and measurement. Manufacturers try various strategies to keep their machines in optimal conditions that ensure continuous operational performance. But how can you keep your machines in peak operational conditions? Let's understand in detail.
Set up basic condition monitoring with CMMS: Implement a CMMS system to regularly assess the condition of machinery and equipment. This facilitates early detection of potential issues before they escalate into costly failures.
Provide training and support: Offer comprehensive training programs to equip maintenance teams with the necessary skills and knowledge to operate and maintain equipment effectively, reducing the risk of errors and machine malfunctions.
Keep Maintenance logs: Maintain detailed records of equipment usage, maintenance activities, and any incidents or abnormalities, facilitating comprehensive equipment management, maintenance and troubleshooting.
Develop effective maintenance plans: Create standardised maintenance plans containing spare parts and work orders to carry out tasks efficiently and effectively, ensuring consistent and timely machine maintenance procedures.
Conduct Maintenance Inspections: Regular maintenance inspections allow timely replacement of worn parts, prevent further damage, and ensure smooth operation. A maintenance checklist or template ensures that every maintenance initiative is executed properly without fail.
Monitor performance metrics: Track maintenance metrics or Key Performance Indicators related to maintenance activities, such as equipment downtime, Mean Time Between Failures (MTBF), and maintenance costs, to assess performance, identify areas for improvement, and optimise maintenance processes.
Implement CMMS for maintenance tasks: Utilise a Computerised Maintenance Management System (CMMS) to streamline maintenance operations; including work order management, inventory management, asset tracking and mobile maintenance, enhancing overall maintenance efficiency and organisation.
Establish a proper lubrication schedule: Develop and adhere to a comprehensive lubrication schedule tailored to the specific requirements of each machine, ensuring proper lubrication to minimise friction, wear, and component failure.
Use efficient Cleaning Procedures: Keep equipment like oil filters or purifiers clean to prevent buildup, corrosion, and overheating, ensuring optimal performance and equipment longevity.
Recheck alignment and calibration: Regularly inspect machines and recalibrate the machinery if necessary to ensure optimal alignment and calibration, maximising operational accuracy, efficiency, and equipment longevity.
How to set up Machine Maintenance with a CMMS software?
Choose a CMMS software: Select a suitable Computerised Maintenance Management System (CMMS) based on your organisation's needs and budget.
Asset inventory: Input all machines and equipment into the CMMS database to create a comprehensive asset inventory.
Establish maintenance schedules: Define and schedule preventive maintenance tasks based on equipment manufacturer recommendations and operational requirements.
Create work orders: Generate work orders for scheduled maintenance tasks and assign them to designated technicians or teams.
Track maintenance activities on CMMS dashboards: Record details of completed maintenance tasks, including date, time, labour, and materials used.
Monitor Equipment Health: Utilise CMMS features to track equipment performance metrics and identify potential issues before they escalate.
Implement predictive maintenance: Integrate predictive maintenance techniques such as condition monitoring and predictive analytics to anticipate equipment failures and plan maintenance accordingly.
Analyse Maintenance Reports: Use CMMS-generated reports and analytics to assess maintenance effectiveness, identify trends, and optimise maintenance strategies over time.
Importance of Machine Maintenance in different Industries
Manufacturing Sector: Machine maintenance in manufacturing is crucial for ensuring uninterrupted production line processes, optimising efficiency, and maintaining product quality. By conducting routine inspections, lubrication, and repairs, manufacturers can minimise the risk and accidents to ensure workplace safety. You can perform preventive maintenance checks on your machines and consider specific challenges in maintaining your equipment in peak operating conditions.
Automotive Industry: Machine maintenance is essential for the smooth operation of assembly lines, machining processes, and vehicle testing equipment in the automotive industry. Well-maintained machinery enhances productivity, facilitates timely production schedules, and upholds stringent quality standards. Consider how automotive manufacturers like you prioritise machine maintenance tasks in their industry.
Healthcare Industry: Machine maintenance in the healthcare industry is vital for properly functioning medical equipment, diagnostic tools, and patient care systems. Healthcare facilities can uphold regulatory compliance and deliver high-quality care by adhering to maintenance schedules and conducting thorough inspections. Do you ensure that medical equipment in your facility is always in optimal condition after CMMS implementation? If yes, you may have already reaped the benefits of CMMS software for your healthcare sector!
Construction Industry: In the construction and infrastructure sector, machine maintenance using a machine maintenance app is essential for the asset performance and longevity of heavy equipment, such as excavators, cranes, and bulldozers. Timely maintenance prevents equipment failures, minimises project delays, and enhances job site safety. But how can you integrate machine maintenance into your construction project timelines? CMMS implementation is the right solution you can make without a doubt!
Many more Industries: Beyond the mentioned sectors, machine maintenance is indispensable across various industries, including food & beverages Industry, energy production, marine vessels, plant hire and more. Regardless of the industry, regular maintenance of machinery and equipment is fundamental for maximising operational efficiency, ensuring workplace safety, and meeting regulatory requirements. Check for ways to adapt maintenance strategies to suit the specific needs and operational processes of your industry. A CMMS system can be a suitable choice for your industry to meet your specific maintenance requirements.
Overcome your Machine Maintenance Challenges with these tips!
Implement predictive maintenance for proactive problem-solving.
Utilise IoT sensors for real-time monitoring and data-driven insights.
Train staff on advanced machine maintenance techniques and equipment operation.
Regularly audit and update your maintenance schedules for efficiency.
Invest in quality spare parts and reliable CMMS providers for long-term asset reliability.
Example of Machine Maintenance with CMMS
Let's understand machine maintenance with an industrial example so that you can relate to it much more!
Consider a scenario where a large-scale construction project was underway, and a crucial piece of equipment, the excavator, unexpectedly failed due to a hydraulic system malfunction.
This failure resulted in significant delays, cost overruns, and missed project deadlines, causing frustration among stakeholders and workers alike.
In the next project, the construction company invested in a Computerised Maintenance Management System (CMMS) to prevent similar setbacks!
By using a CMMS software, they could:
Monitor the excavator's performance and condition in real-time.
Analyse sensor data from critical components of the excavator.
Predict the maintenance needs of the excavator before failures occur.
Track and schedule timely maintenance for the excavator.
Receive alerts indicating potential issues with the excavator's hydraulic system.
Ensure the excavator remains in optimal operational condition.
Track maintenance metrics like OEE
Make detailed maintenance reports including graphs, statistics and maintenance technicians involved in the excavator's maintenance process.
Minimise downtime and reduce maintenance costs as the excavator functions well.
As a result of implementing CMMS and adopting advanced maintenance strategies, the construction company experienced improved equipment reliability, enhanced workplace safety and optimised workflow efficiency.
Construction workers can confidently carry out their tasks, knowing that equipment failures are addressed promptly. Timely delivery of your construction project can increase your reputation and overall project success!
Don't you wish to execute successful machine maintenance within your industry? Everything starts with reliable machine operations and workplace safety. Businesses can achieve exceptional performance levels by prioritising machine maintenance and implementing advanced solutions like Computerised Maintenance Management Systems (CMMS).
In a study by Deloitte, it was found that predictive maintenance typically boosts productivity by 25%, slashes breakdowns by 70%, and decreases maintenance costs by 25% on average. With CMMS, predictive and preventive maintenance strategies, and machine condition monitoring, you can ensure equipment reliability, minimise downtime, and enhance workplace safety. So, invest in your success today by making machine maintenance a top priority and watching your industry thrive.