Contents
- Implementing Emergency Maintenance Procedures
- Why are Emergency Maintenance Plans important?
- How to Deal with Emergency Maintenance Situations?
- How can you set up an effective Emergency Maintenance Procedure with CMMS in your industry?
- What are the Challenges of Emergency Response? How to Overcome them?
- Risks of not having a defined Emergency Maintenance Procedures
- CMMS for Maintenance Needs- No tool, No gain!
Implementing Emergency Maintenance Procedures
You will probably know the complexities of managing emergency maintenance requirements and repairs within the shop floors housing critical assets. From planning for emergencies to handling emergency maintenance procedures, the need for robust emergency maintenance protocols and suitable maintenance software is undeniable.
Mitigating emergency situations on your shop floor requires proactive strategies like conducting risk assessments and implementing maintenance procedures to promptly manage safety accidents and equipment failures. However, it is important to understand the steps for setting up effective emergency maintenance procedures. Let's move on and understand why manufacturers develop effective emergency maintenance procedures for their shop floors.
Why are Emergency Maintenance Plans important?
Emergency maintenance plans outline protocols and procedures for responding to emergency maintenance needs in an industry. These structured strategies can swiftly address unexpected equipment failures, safety incidents, or environmental hazards. Emergency maintenance typically focuses on escalation procedures, emergency task assignments, and resource allocation strategies. By establishing clear guidelines and responsibilities, emergency maintenance plans enable organisations to respond promptly to critical situations, restore functionality, and maintain operational continuity.
During emergencies, the maintenance team is responsible for mitigating safety concerns on a shop floor. Establishing emergency maintenance procedures and plans is vital across industries as it offers several benefits, including:
- Minimising Downtime: Effective emergency maintenance plans and procedures minimise downtime by swiftly addressing equipment failures or safety issues, ensuring continuity of operations.
- Enhancing Safety: Established maintenance procedures prioritise employee safety by providing clear protocols for handling emergencies, reducing the risk of accidents and injuries.
- Protecting Assets: With predefined maintenance plans, industries safeguard critical assets, preventing costly damage and prolonging equipment lifespan.
- Improving Efficiency: Streamlined procedures enable quick identification and resolution of issues, optimising workflow efficiency and productivity.
- Boosts Reputation: Industries with reliable emergency maintenance plans demonstrate commitment to safety and reliability, enhancing their reputation among customers and stakeholders.
- Cost Savings: Proactive maintenance procedures help industries avoid costly repairs and downtime associated with emergencies, resulting in significant long-term cost savings.
- Facilitates Decision-Making: Clear protocols empower maintenance teams to make informed decisions during emergencies, minimising confusion and managing response times.
- Building Resilience: Well-established emergency maintenance plans build organisational resilience, enabling industries to effectively withstand unexpected challenges and disruptions.
- Ensuring Business Continuity: Having robust emergency maintenance procedures and plans ensures uninterrupted operations, safeguarding business continuity and sustainability.
- Serves as Reference for future Maintenance: Tracking and documenting the emergency maintenance procedures carried out during emergencies serves as a reference for future maintenance, ensuring streamlined procedures and improved preparedness.
How to Deal with Emergency Maintenance Situations?
When dealing with emergency maintenance situations, it's crucial to recognise that worker safety and asset health are significant concerns for manufacturers. Implementing an emergency maintenance plan with well-defined procedures can significantly aid such scenarios. Otherwise, it will significantly impact your Overall Equipment Effectiveness (OEE), as the equipment is unavailable for production during an emergency. Therefore, swift and effective maintenance measures must be in place to mitigate the impact on OEE and minimise downtime. It is important to have an emergency maintenance plan to prepare for unexpected emergency situations. You can consider the following ideas while dealing with emergency maintenance on your shop floor:
- Conduct thorough root cause analysis to identify underlying issues promptly.
- Utilise emergency maintenance checklists to ensure systematic and comprehensive troubleshooting.
- Prioritise safety measures and risk mitigation strategies during emergency maintenance operations.
- Focus on swift resolution to minimise downtime and operational disruptions.
- Collaborate effectively with cross-functional teams to expedite problem-solving efforts.
- Document all actions taken and lessons learned for future reference and continuous improvement.
How can you set up an effective Emergency Maintenance Procedure with CMMS in your industry?
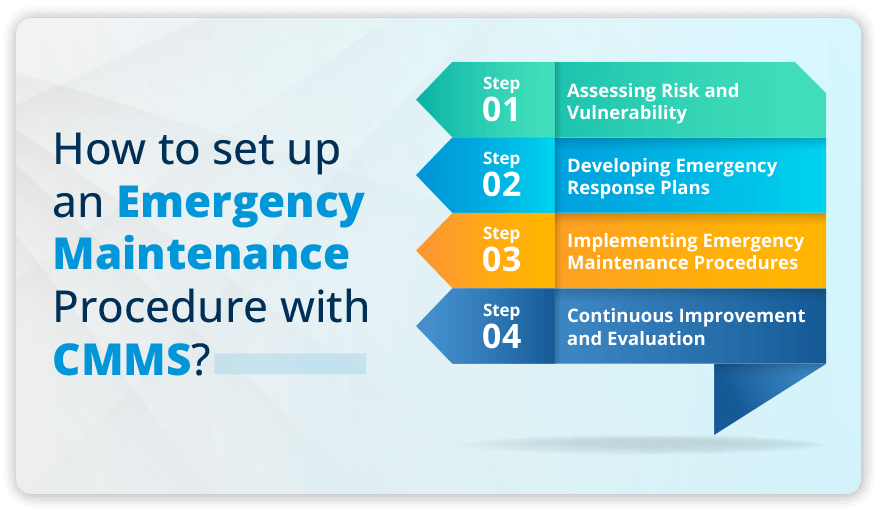
Setting up effective emergency maintenance procedures in any industry ensures preparedness and responsiveness in critical situations. What if manufacturers lack a specific tool or system like CMMS to manage their emergency maintenance needs? It's not practical to appoint many maintenance personnel to monitor the real-time conditions of equipment or assets on a factory floor with millions of processes, assets, and machinery. CMMS (Computerised Maintenance Management System) can help manufacturers with every maintenance need that arises on a factory floor.
Let's examine the four steps taken by maintenance professionals using the CMMS system to establish a reliable maintenance procedure during emergencies.
-
Step 1: Assessing Risk and Vulnerability
- Identify Critical Assets and Systems: Begin by identifying the key assets and equipment critical to your industrial operations. This includes machinery, systems and other essential components necessary for day to day operations on the shopfloor. An asset maintenance checklist can help you here.
- Run Risk Assessments: Conduct comprehensive risk assessments using the CMMS system to identify potential hazards, vulnerabilities, and equipment failure points within your operations. To prioritise risks, consider factors such as equipment reliability, environmental risks, and regulatory compliance.
- Evaluate Potential Emergency Scenarios: Use CMMS software to assess various emergency scenarios, considering equipment reliability, historical maintenance needs or data, and predictive analytics. Create maintenance procedures tailored to different emergency situations to ensure preparedness and effective maintenance response.
-
Step 2: Developing Emergency Response Plans
- Establish Clear Communication Channels: Establish clear communication channels and protocols for disseminating emergency maintenance alerts, instructions, and updates. Ensure all maintenance personnel know how to report emergencies and have access to CMMS mobile applications for real-time communication.
- Define Roles and Responsibilities: Clearly define specific roles and responsibilities for all maintenance personnel involved in emergency response efforts. Utilise CMMS to assign, schedule and track maintenance tasks. Also, prioritise your workplace safety by designating individuals or teams responsible for specific tasks, such as evacuation coordination, equipment shutdown, or first aid during emergencies.
- Making Response Protocols for Different Scenarios: Creating emergency response protocols and procedures tailored to different emergency scenarios identified during the risk assessment phase. Outline step-by-step instructions for mitigating risks, containing incidents, and restoring operations safely and efficiently.
-
Step 3: Implementing Emergency Maintenance Procedures
- Training and Preparedness Programs: Provide training and preparedness programs to ensure that maintenance personnel are adequately trained and equipped to respond to emergencies effectively. Conduct drills and simulations to practise emergency response procedures as necessary.
- Procuring necessary Equipment and Resources: Ensure that equipment, tools, supplies, and resources are readily available to support emergency maintenance activities. This includes emergency kits, personal protective equipment, an emergency maintenance checklist, and specialised tools for containment and repair. Use CMMS to manage inventory and procurement processes, ensuring necessary resources are readily available for emergency maintenance activities.
- Documenting Emergency Responses and Results: To facilitate post-incident analysis and evaluation, systematically document all emergency responses and outcomes. Using CMMS software, maintenance technicians can generate detailed maintenance reports; including emergency response times, maintenance actions taken, and learned outcomes to identify improvement areas and for future reference.
-
Step 4: Continuous Improvement and Evaluation
- CMMS for Continuous Monitoring and Reporting: CMMS can continuously monitor, track, schedule, manage and report maintenance activities to understand the effectiveness of emergency maintenance procedures. Maintenance KPIs (Key Performance Indicators) such as response times, downtime, incident resolution rates, and OEE (Overall Equipment Effectiveness) are tracked and monitored to identify trends and improvement areas.
- Collecting Feedback and Lessons Learned: Feedback from maintenance personnel involved in emergency response efforts to gather insights and learning outcomes. Encourage open communication and collaboration to identify strengths, weaknesses, and opportunities for enhancing emergency maintenance procedures.
- Updating and Refining Emergency Maintenance Procedures: Regularly review and update emergency maintenance procedures based on feedback, changes in industry and best practices for emergency maintenance plans and procedures. Continuously refine and optimise emergency maintenance procedures to ensure they remain practical, relevant, and effective.
Simplify Emergency Maintenance with Titan CMMS
What are the Challenges of Emergency Response? How to Overcome them?
- Lack of Preparedness: Organisations may struggle to respond effectively to emergencies without adequate preparation. Establishing comprehensive emergency response plans, conducting regular training drills, and utilising software solutions like CMMS to automate maintenance processes with real-time updates can help you here.
- Time and Communication Constraints: Emergency situations often demand immediate action, leaving little time for decision-making and coordination. Streamlined communication channels, clear protocols, and regular training can help mitigate time constraints. CMMS technology provides automation, enabling faster responses and efficient maintenance task management.
- Uncertainty and Complexity of Incidents: Emergencies are characterised by uncertainty and complexity, making it challenging to anticipate and respond effectively. Contingency plans, risk assessment frameworks, and predictive analytics offered by CMMS can help organisations identify potential risks in advance and develop proactive mitigation strategies.
- Safety Concerns: Safety is paramount during emergency response efforts. Organisations must prioritise the well-being of personnel and stakeholders by implementing rigorous safety protocols, providing adequate training, and leveraging technology solutions like CMMS to monitor safety compliance and address safety concerns promptly.
- Limitation of Resources: Limited availability of maintenance technicians, equipment, and supplies can hinder emergency response efforts. Organisations must prioritise resource allocation, invest in adequate training and equipment, and leverage technology solutions like CMMS to optimise resource utilisation and support efficient task management.
Risks of not having a defined Emergency Maintenance Procedures
What can you expect if you run a business without well established emergency maintenance procedures? There are several situations where your business needs an emergency maintenance plan with well established protocols to prevent costly downtime. Let’s understand in detail.
- Unexpected Equipment Breakdowns: Sudden machinery failures require immediate attention to minimise downtime. When critical equipment fails, troubleshooting, repairs, or replacements are necessary for swift functionality restoration.
- Unforeseen Safety mishaps: Safety incidents or hazardous situations require prompt action to mitigate risks and ensure personnel safety. During a safety accident, first aid or evacuation procedures are suitable measures that must be adopted.
- Environmental Hazards: Emergencies like leaks or chemical spills demand quick containment to prevent ecological damage. Maintenance managers must take quick measures, such as containment procedures, cleanup, and compliance with industrial regulations, during events that result in environmental hazards.
- Sudden Power Outages: Shop floors may experience unexpected electrical supply loss, disrupting overall operational activities. Emergency responses, including root cause identification, power restoration, and continuity backup solutions, are adopted during such situations.
- Facility Damages: Structural damage, fires, or floods threaten facility integrity. During such events, safety assessments, repairs, and recovery methods are undertaken.
- Supply Chain Disruptions: Events like parts shortages disrupt maintenance activities. To prevent operational disruptions, sourcing alternatives, expediting deliveries, or implementing contingency plans must be considered.
- Cybersecurity Breaches: Breaches are attacks that compromise maintenance systems or data integrity. So as to mitigate the impact, immediate responses like isolating systems, implementing security measures, and restoring backups are taken during security breaches.
CMMS for Maintenance Needs- No tool, No gain!
The CMMS system is widely adopted across manufacturing , automotive, healthcare, food & beverages, construction, plant hire, energy, marine vessels and many other industries. The CMMS solution offers features like asset management, work order tracking, maintenance scheduling, inventory management, and reporting capabilities necessary for all maintenance activities. By using CMMS software, industries can streamline their maintenance activities, improve efficiency, and reduce downtime, ultimately enhancing overall operational performance and asset reliability. As we conclude, you might have understood that emergency maintenance needs result from unforeseen events disrupting your operational continuity and profitability. Investing in CMMS software is essential to ensure seamless operations while minimising disruptions. With robust features like preventive maintenance scheduling and real-time monitoring, CMMS empowers manufacturers to manage their maintenance needs and respond swiftly ahead of emergencies proactively. CMMS is a must-have maintenance solution on your factory floor to ensure operational continuity, safety, productivity and efficiency. Don't wait until it's too late – implement CMMS to achieve your business goals with minimum downtimes and safety mishaps.