Predictive & Preventive Maintenance - TPM
April 28, 2022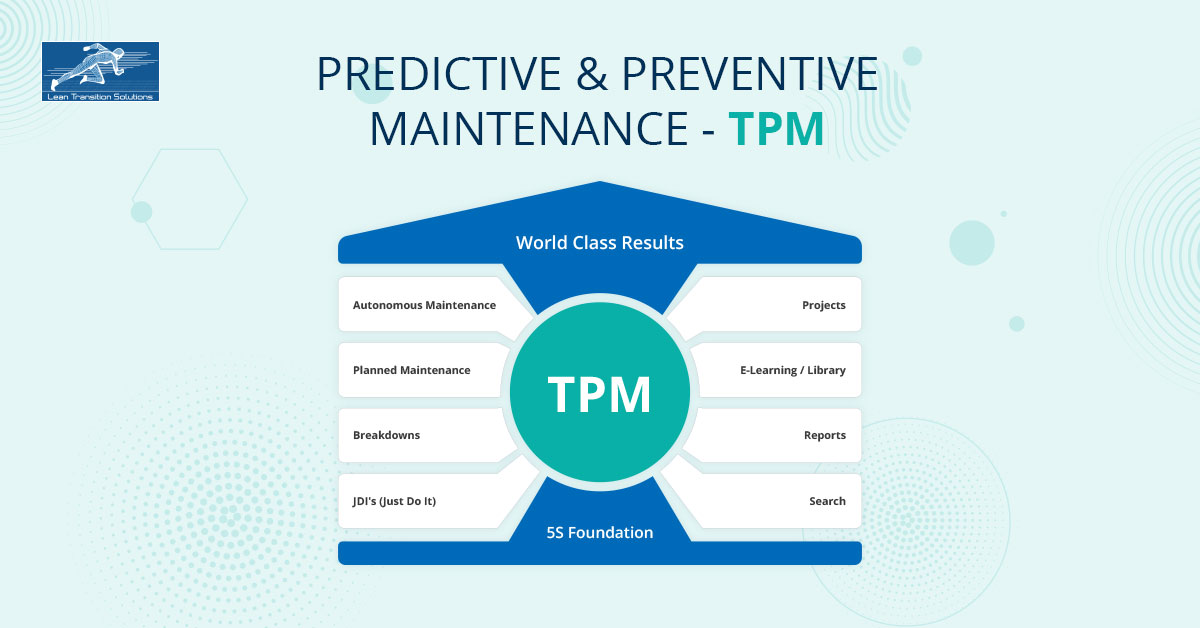
The immeasurable impact of Total Productive Maintenance (TPM) in Manufacturing has been proven over the past few decades. Manufacturers started implementing TPM following Nippondenso, the Japanese manufacturer who implemented TPM for the first time. One of the essential principles of TPM is to increase production and satisfices employee morale and job participation. Employee participation and training are crucial for overall TPM effectiveness. To achieve the prime target, which is the elimination of waste, TPM must be implemented to address both equipment and employee participation. This will sometimes be a pain point for manufacturers as they fail to attract the right amount of employee participation.
When machines are down or not working to the optimum condition, it severely impacts the "Bottom Line". Avoiding these hurdles will help the manufactures to achieve the primary goals of Total Productive Maintenance like:
Increase Equipment Effectiveness
Maintenance Prevention
Improve Maintenance Efficiency and Effectiveness
Active Participation of Operators in Periodical Maintenance
Enhance the Skills of People Involved
By identifying these critical reasons, Lean Transition Solutions Ltd developed the LTS-TPM system called 'TITAN'. This trustworthy software platform will enable organisations to have people and machines running to the optimum level and maintain and improve the uptime of machines and reduce the overall manufacturing cost. TITAN gives you the power to manage your bespoke requirements and maintenance flow. Titan empowers the TPM manager to manage and coordinates all the TPM activity through the Web or Mobile interface.