How can CMMS help in Facility Management ?
February 19, 2024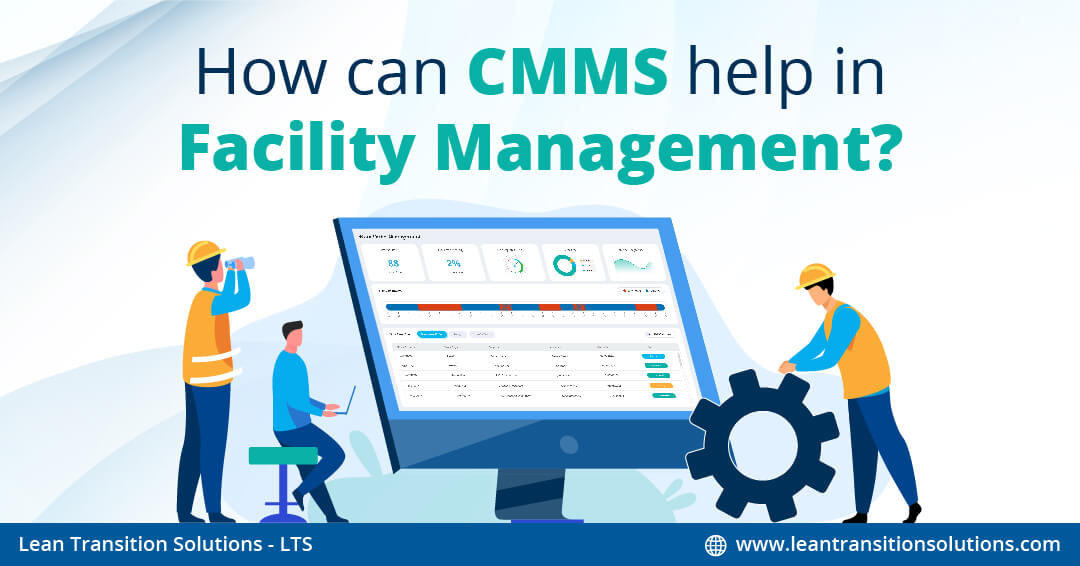
Facility managers often deal with the complexities of maintenance needs, repairs and overall upkeep of their facilities. Implementing CMMS becomes a strategic choice for many facility managers as it can do much beyond routine maintenance. CMMS is a comprehensive solution to managing, tracking, and enhancing facility maintenance operations, ultimately driving organisational success. Let's go ahead and understand more about facility management and how CMMS can be the right choice for facilities maintenance and operations.
What is Facility Management?
IFMA (International Facility Management Association) defines facility management as an organisational function integrating people, places, and processes within the built environment to improve people's quality of life and core business productivity. Facility management encompasses a range of tasks, such as space planning, maintenance scheduling, safety compliance, and environmental sustainability.
Facility managers coordinate these maintenance operations and optimise physical spaces within organisations to ensure the functionality, safety, and efficiency of each facility. Facility managers also play a prominent role in services and functions supporting core business, such as maximising resource utilisation and minimising maintenance costs. Ultimately, facility management aims to create efficient and sustainable environments that are comfortable and productive.
Key components of Facility Management
- Maintenance Operations: Systematic upkeep of physical assets, ensuring functionality and longevity through preventive, predictive, and reactive maintenance activities.
- Space Planning and Management: Strategic arrangement of physical spaces for efficiency and productivity, optimising layouts and resources, and adapting spaces to meet changing needs.
- Safety and Security: Protecting occupants, assets, and property from risks and hazards through safety protocols, risk assessments, maintenance of safety equipment, and compliance with regulations.
- Environmental Sustainability: Minimising environmental impact through energy-efficient practices, waste reduction, adoption of renewable energy, and sustainable materials and technologies.
- Risk Management: Identifying, assessing, and mitigating risks impacting operations, safety, or financial stability through contingency plans, emergency response protocols, security breach checks, and regulatory compliance.
Why is Facility Management important?
It is good to have an efficient facility management strategy for your organisation, as it plays a pivotal role in ensuring success. Facility management is important because it optimises the use of physical spaces, enhances operational efficiency, and ensures compliance with safety and regulatory standards. By implementing effective facility management practices, organisations reduce costs, minimise downtime and extend the asset lifespan. Additionally, facility management contributes to a conducive and productive environment for employees and stakeholders, supporting the overall goals and objectives of the organisation.
How can CMMS help in Facility Management?
CMMS (Computerised Maintenance Management System) aids facility management by centralising maintenance tasks, automating work orders, and enhancing asset performance. The CMMS software enables a proactive approach through maintenance scheduling, minimising downtime and extending asset lifespan.
By using CMMS software, facility managers can:
- Systematically track maintenance tasks and schedules across all facilities.
- Implement preventive maintenance strategies to minimise downtime and extend equipment lifespan.
- Measure maintenance metrics to identify areas for improvement and optimise resource allocation.
- Streamline work order management processes, ensuring timely and efficient resolution of maintenance issues.
- Analyse real-time maintenance data and ensure maintenance operations to generate maintenance reports.
- Enhance compliance with regulatory standards and industry best practices.
Benefits of using CMMS Software in Facility Management
- Streamlines Maintenance Processes: CMMS software automates and organises maintenance tasks, schedules, and workflows, reducing manual efforts and improving overall efficiency.
- Improves Data Accuracy and Accessibility: CMMS ensures accurate and easily accessible data related to asset management, maintenance history, and inventory and helps in maintenance planning.
- Enhances Work Order Management: CMMS enables efficient creation, assignment, and tracking of work orders, ensuring timely completion of maintenance tasks and minimising downtime.
- Facilitates Predictive Maintenance Strategies: CMMS software uses machine learning and predictive analytics to predict equipment failures, enabling proactive maintenance interventions and preventing costly breakdowns.
- Supports Decision Making with Maintenance Reports: CMMS generates insightful analytics and reports on maintenance performance, asset health, and resource utilisation, empowering facility managers to make informed decisions and optimise maintenance strategies.
How to implement CMMS for Facility Management?
Implementing a CMMS (Computerised Maintenance Management System) for Facility Management involves several steps. By following these steps, organisations can effectively implement a CMMS for facility management, streamline maintenance processes, and enhance operational efficiency. Here's a breakdown of the process:
Step 1 - Assessment and Planning
- Assess current maintenance processes, workflows, and needs.
- Involve key stakeholders in the planning process.
- Define goals and objectives for implementing the CMMS.
- Determine the budget and resources required for implementation.
Step 2 - Research and Selection
- Research and find out the best CMMS software solution available in the market.
- Evaluate features, scalability, user-friendliness, and compatibility with existing systems.
- Consider cloud-based vs. on-premise solutions based on organisational needs.
- Select the most suitable CMMS software based on evaluation criteria.
Step 3 - Customisation and Configuration
- Customise the CMMS software to align with specific facility management requirements.
- Configure user roles and permissions to ensure appropriate access levels.
- Set up preventive maintenance schedules, work order templates, asset tracking categories, and inventory management modules.
- Import existing data (equipment lists, maintenance history, etc.) into the CMMS database.
Step 4 - Training and Documentation
- Provide comprehensive training sessions for staff members who will be using the CMMS.
- Conduct hands-on workshops and simulations to familiarise users with the CMMS interface and functionalities.
- Provide ongoing assistance for troubleshooting and establish a supporting system.
Step 5 - Pilot Testing
- Conduct a pilot test of the CMMS system with a small group of users or in a specific department.
- Gather feedback on usability, performance, and any issues encountered during the pilot phase.
- Make necessary adjustments and refinements to the CMMS configuration based on user feedback.
Step 6 - Full Deployment
- Roll out the CMMS system across the entire facility or organisation.
- Monitor system performance and user adoption during the initial deployment phase.
- Address any technical issues or user concerns promptly to ensure a smooth transition.
Step 7 - Continuous Improvement
- Establish regular reviews and assessments of CMMS performance and usage.
- Solicit feedback from users and stakeholders on improvement areas.
- Implement updates, upgrades, and additional training as needed to optimise CMMS functionality.
CMMS Facility Management : Best Practices to improve efficiency
- Regularly update maintenance schedules and procedures based on CMMS data analysis.
- Continuously refine CMMS configurations to align with evolving facility needs and industry best practices.
- Encourage open communication and feedback loops among facility management teams to address issues promptly.
- Leverage CMMS-generated reports to optimise resource allocation and budgeting for maintenance activities.
- Implement mobile access to the CMMS system for real-time updates and on-the-go management.
- Establish maintenance KPIs (Key Performance Indicators) to monitor CMMS effectiveness and drive continuous improvement efforts.
- Review and update asset inventories within the CMMS database.
- Collaborate with vendors and contractors to integrate external maintenance services seamlessly into the CMMS workflow.
Difference between CMMS and CAFM
CAFM (Computer-Aided Facility Management) and CMMS (Computerised Maintenance Management System) serve distinct purposes in facility management. CAFM focuses on overall facility operations, including space management, asset tracking, and workplace optimisation. On the other hand, CMMS is specifically designed for maintenance management, facilitating preventive and reactive maintenance tasks, work order tracking, and asset maintenance history.
While different organisations may use various tools like ERP, CAFM, and CMMS for managing their facilities, relying solely on a single system may not be optimal. Proper integration between CMMS and CAFM can enhance operational efficiency, ensuring seamless coordination between maintenance and overall facility management functions.
Facility Management Examples across various industries
CMMS plays a key role in facility management across many industries, including manufacturing, automotive, healthcare, hospitality, oil & gas, mining & drilling, marine vessels, aerospace, FMCG, energy, plant hire, and more. Its robust features streamline maintenance operations, optimise asset performance, and ensure regulatory compliance, making it an indispensable tool for enhancing operational efficiency and reducing downtime across various industries.
Facility Management example in the Manufacturing
- Predictive Maintenance for Machinery: CMMS enables proactive monitoring and predictive maintenance of machinery, reducing downtime and optimising production efficiency.
- Inventory Management for Spare Parts: CMMS streamlines inventory management processes, ensuring the timely availability of spare parts for maintenance needs, thereby minimising disruptions in manufacturing operations.
- Compliance Tracking for Regulatory Standards: CMMS facilitates tracking and documenting compliance with regulatory standards and requirements, ensuring adherence to safety and quality protocols in the manufacturing sector.
Facility Management example in the Healthcare Industry
- Equipment Maintenance and Calibration: CMMS assists in scheduling and tracking maintenance tasks, including equipment maintenance and calibration, ensuring optimal performance and reliability of medical equipment.
- Patient Safety and Compliance: CMMS helps healthcare facilities maintain compliance with regulatory standards and protocols related to patient safety, infection control, and medical device management.
- Resource Allocation and Optimisation: CMMS aids in efficient resource allocation and optimisation, enabling healthcare facilities to manage staff, equipment, and supplies effectively to meet patient care demands while minimising costs.
Facility Management example in Commercial Real Estate
- Building Systems Maintenance: CMMS aids in the maintenance of building systems, including HVAC, plumbing, and electrical systems, by scheduling regular inspections, tracking work orders, facilitating preventive maintenance tasks, and ensuring optimal building performance and tenant satisfaction.
- Tenant Satisfaction and Retention: CMMS enhances tenant satisfaction and retention by promptly addressing maintenance requests, tracking service levels, ensuring timely resolution of issues, and fostering positive tenant experiences and long-term relationships.
- Energy Efficiency and Sustainability Initiatives: CMMS supports commercial real estate in implementing energy efficiency and sustainability initiatives by tracking energy consumption, scheduling energy audits, managing eco-friendly practices, and reducing operational costs and environmental impact.
Why is sustainability important in Facilities Management?
Sustainability in facility management is crucial for several reasons. CMMS leverages digitalisation to promote sustainable and green practices. CMMS facilitates paperless report generation and log-keeping, reducing reliance on paper documents, minimising environmental impacts, enhancing efficiency, and promoting facility management sustainability operations.
Implementing energy-efficient systems like CMMS supports green initiatives and reduces environmental impact, enhancing efficiency, minimising scrap, and effectively managing your budgets. These efforts contribute to environmental stewardship and long-term viability in facility management sustainability operations.
Time is crucial, and competition is fierce! To stay ahead, manufacturers must utilise the power of CMMS software to revolutionise their Facility management operations. By implementing CMMS, organisations can streamline maintenance processes, optimise resource allocation, and enhance their facility operations.
CMMS offers a centralised platform for tracking, scheduling, and measuring maintenance operations in various departments of industry. CMMS empowers facility managers to make the best decisions based on data, minimising downtime and maximising asset lifespan. It's time for manufacturers to embrace CMMS and elevate their facility management practices to new heights, setting themselves above in an increasingly competitive landscape.