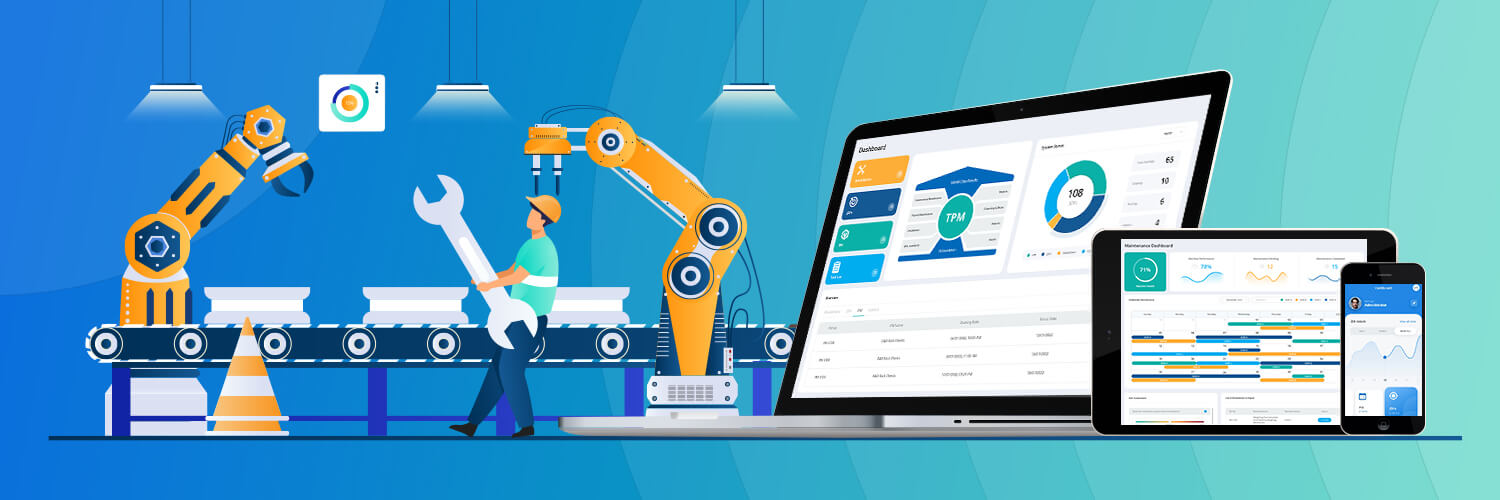
Revolutionising Maintenance Operations:
The Impact of CMMS Software Implementation on Titan WheelsTitan Steel Wheels, a leading global manufacturer of off-highway and auto crane multi-piece wheels based in Cookley, England, began its journey towards operational excellence by implementing lean practices in collaboration with LTS. However, their journey was impeded by significant challenges highlighting the criticality of an efficient Total Productive Maintenance(TPM) system in sustaining lean operations. This case study explores how the company addressed this challenge by changing its maintenance approach, improving machinery performance, and promoting a culture of continuous improvement.
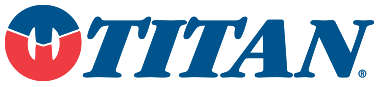
Client Overview
Titan Steel Wheels. is a renowned manufacturer of heavy-duty wheels that cater to various industries, including construction, mining, earth moving, and materials handling. With a strong foundation, their wheels are trusted for its durability and innovation. Titan also offers a complete line of wheels, tyres and undercarriage products for a wide range of off-the-road equipment. With a worldwide network of dealers, Titan is a global brand that original equipment manufacturers and operators can count on for durable products and quality service.
Challenges Faced: Reevaluating Maintenance in Lean Operations
Maintenance Impact on Lean Initiatives:
Titan Wheels encountered a significant challenge in the process of integrating Total Productive Maintenance (TPM) into their lean operations. This challenge stemmed from the adverse effects of machine downtime on production efficiency, directly impacting their lean initiatives' success. The detrimental setback of maintenance issues and breakdowns offset the advantages of their lean efforts, specifically their attempts to implement TPM.
Maintenance Management Deficiency:
Struggling to balance TPM principles with the challenges of machine breakdowns, Titan Wheels recognised the essential need for a robust maintenance management solution that specifically incorporated TPM practices. Such a solution was vital to address maintenance issues proactively and minimise machine downtime, ultimately enhancing their ability to realise the full potential of lean efforts, especially when combined with TPM.
Centralised Solution Necessity:
The absence of a centralised maintenance system that integrated TPM practices led to challenges in coordinating tasks, managing employee shifts, and tracking machine downtimes within Titan Wheels. Communication gaps between departments resulted in delayed responses to maintenance needs and breakdowns. The lack of a streamlined system hindered resource allocation and efficient work progress monitoring, particularly in the context of TPM implementation.
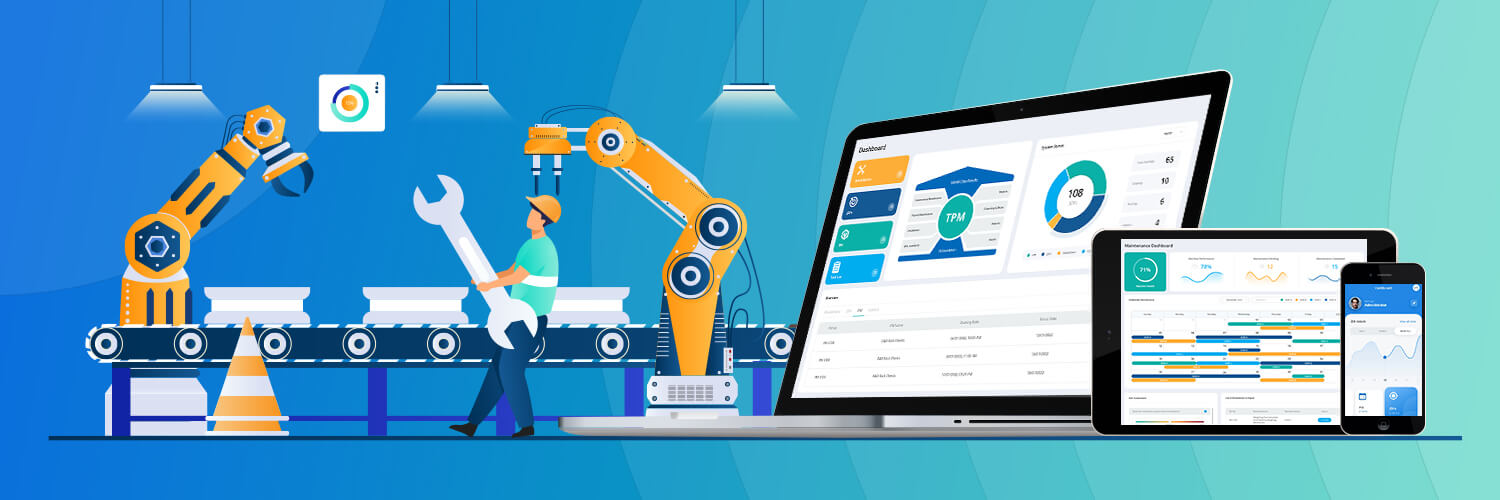
Solution: Embracing Maintenance Optimisation
Titan Wheels adopted Titan CMMS software to address these challenges and streamline maintenance management processes.
Autonomous Maintenance and Focused Improvement:
The system encouraged preventive and autonomous maintenance practices, contributing to longer machine lifespans and reduced downtime.
Breakdown Management:
The software enabled the prompt reporting of the breakdowns within the departments. Maintenance gets scheduled immediately, allowing the technicians to be assigned to shifts without delay. The technicians can access their tasks in real-time, guaranteeing efficient and quick resolution of any issues.
Planned Maintenance:
Using Titan CMMS for scheduling planned maintenance has significantly streamlined the workflow. The calendar-based system enabled them to create comprehensive maintenance plans with all necessary details, such as required parts and tools. Risk assessments and audits are conducted along with tracking real-time maintenance progress, enabling efficient updates and team collaboration.
Machine Improvement Task Lists:
The CMMS also allowed management of the machine improvement tasks, irrespective of their association with breakdowns. These tasks are systematically scheduled and tracked, like breakdown and maintenance processes. Risk assessments were conducted, and progress was monitored, ensuring a systematic task approach.
Employee and Machine Management:
Titan CMMS organised and allocated the employees into their departments, teams, and shifts. Machines were allocated to departments based on their locations. Each machine had associated checklists detailing required tasks, responsible individuals, and task deadlines. Efficient allocation of technicians and resources based on schedules and machine requirements maximised workforce utilisation.
Reports and Analysis:
The CMMS software generated various reports, including breakdown, maintenance, and employee reports. These reports provided insights into machine downtime, Mean Time Between Failures (MTBF), Mean Time To Repair (MTTR), and other key metrics. This data facilitated informed decision-making and continuous improvement initiatives.
Mobile App:
The CMMS Mobile Maintenance App enabled operators and technicians to access the system remotely through iOS and Android devices. This mobile access streamlined issue resolution, preventing delays in addressing maintenance tasks.
Employee, Hierarchy and Team Management:
Forming a centralised employee management system, Titan CMMS organised and allocated employees to their departments, teams, and shifts, streamlining workforce management. Real-time updates fostered better department collaboration, enabling smoother maintenance operations.
Scorecard and KPI Management:
The CMMS software generated various reports with real-time metrics, including breakdown, maintenance, and employee reports, providing insights into key metrics, such as Mean Time Between Failures (MTBF) and Mean Time To Repair (MTTR).
Project, Resource Library and Discussion Area:
In comprehensive Project Management, Titan CMMS facilitated the scheduling and tracking of maintenance tasks. The Document Management system acted as a library for storing department-specific files, enhancing collaboration and knowledge sharing. Discussion areas allowed real-time communication to the employees to collaborate effectively, ensuring quick issue resolution.
Inventory and Supplier Management:
The CMMS system enabled tracking of parts and inventory levels, ensuring that necessary components were always available. Supplier integration streamlined the procurement process, reducing lead times and providing a steady supply of critical parts.
Results and Benefits: A Paradigm Shift in Operations
Titan Steel Wheels' commitment to transforming maintenance and embracing lean principles yielded significant outcomes:
-
01Enhanced Productivity
The streamlined processes and real-time updates enabled faster response to breakdowns, reducing machine downtime and enhancing overall productivity.
-
02Resource Utilisation
Efficient allocation of technicians and resources based on schedules and machine requirements optimised workforce utilisation.
-
03Data-Driven Decisions
Accurate data and reports facilitated data-driven decision-making, improving maintenance strategies and minimising disruptions.
-
04Improved Collaboration
Centralised communication and real-time updates fostered better department collaboration, leading to smoother maintenance operations.
-
05Continuous Improvement
The software's feedback mechanisms and continuous improvement questions encouraged a culture of proactive enhancement in maintenance practices.
-
06Mobile Access
The mobile app empowered technicians to address tasks remotely, reducing response time and enabling faster execution.
-
07Collective Responsibility
The introduction of real-time data collection fostered a culture of accountability, encouraging active problem-solving and collective contributions to the organisation's success. Transparent access to real-time data encouraged employees to delve deeper into issues to prevent a recurrence.
-
08Operational Excellence
The journey provided invaluable insights beyond machinery maintenance, encompassing data-driven decision-making and a commitment to continuous improvement.
-
09Maintenance Optimisation:
The TPM encouraged focus preventive and autonomous maintenance practices, contributing to longer machine lifespans and significantly reducing downtime.
-
10Real-time Communication:
Discussion areas provided a platform for employees to communicate and collaborate effectively, ensuring rapid issue resolution. Real-time communication enhanced the agility of the maintenance teams, resulting in faster response times.
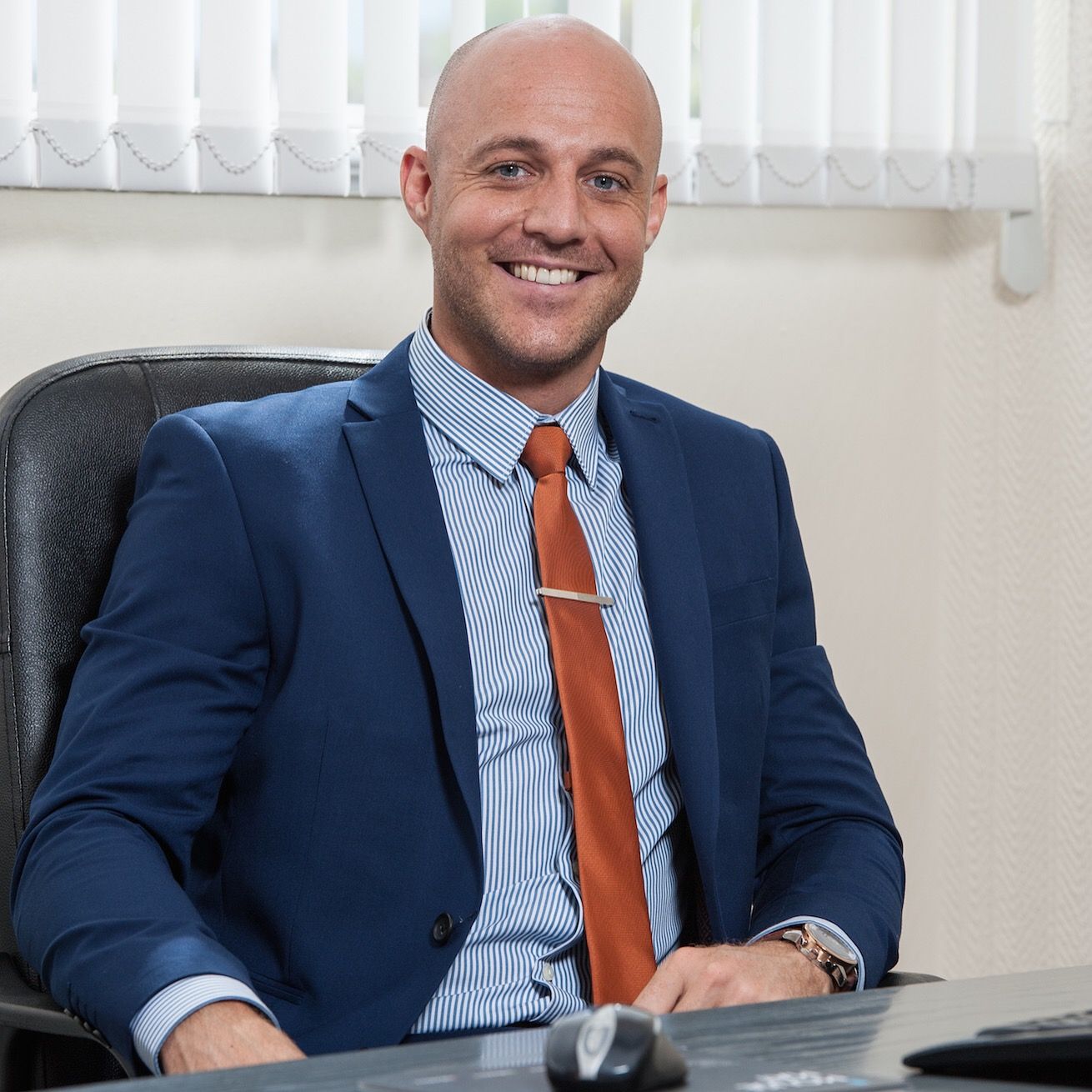
JACOB HIGLEYLean Manufacturing Manager at Titan
Titan Wheels' experience underscores the potential of addressing maintenance intricacies within a lean framework. It serves as an inspiring testament to the power of innovation and collaboration, demonstrating how a holistic approach to TPM management can drive productivity, empower employees, and propel an organisation towards operational excellence. Through the strategic adoption of Titan CMMS software, Titan Wheels transformed its maintenance journey from a challenge into an opportunity for growth. The result was heightened machine productivity, more efficient resource utilisation, and a workforce empowered to contribute to the organisation's excellence. The fusion of technology, mindset transformation, and innovative strategies yielded a harmonious symphony that elevated Titan Wheels to new operational excellence heights.