Optimising Maintenance, Repair, and Operations (MRO) for Seamless Operations
Enhance your maintenance strategies by managing the MRO for improved equipment reliability and operational efficiency.
Start Free Trial Watch VideoContents
- What is MRO?
- Why is MRO important?
- What are the functions of MRO?
- What is an example of an MRO?
- Types of MRO
- What are MRO materials or MRO inventory?
- Which industry uses MRO?
- How to manage your MRO with a CMMS?
- Types of MRO maintenance in a manufacturing industry
- Best Practices for an Effective MRO Strategy
- How Does MRO Affect Supply Chain Management and Inventory Management?
- What are the benefits of actively managing the MRO?
What is MRO?
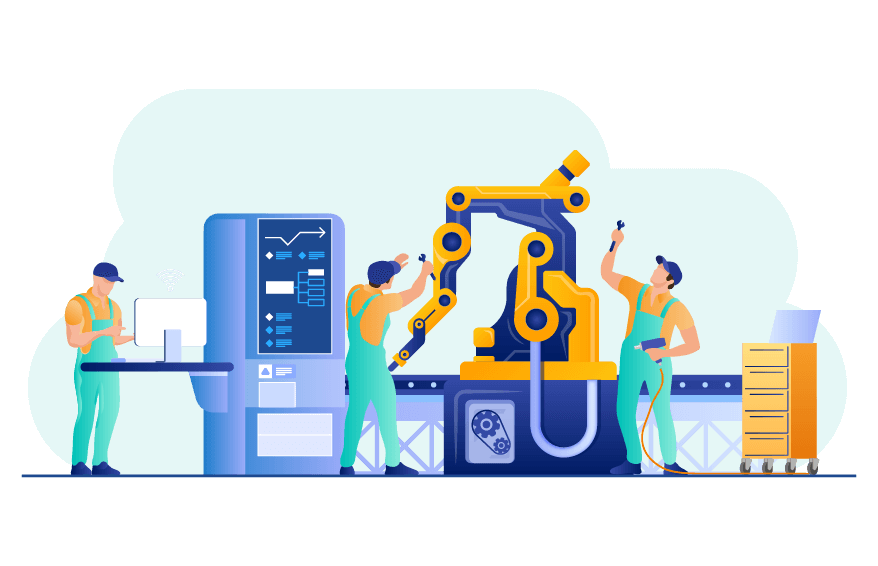
MRO stands for Maintenance, Repair and Operations or Overhaul in an industry. The set of operations and activities required to keep the company's facilities and production process running smoothly, MRO is associated with the upkeep of the shopfloor, which includes the physical maintenance of the structure, systems or equipment used for the production process. MRO management ensures that everything works correctly, prevents future equipment problems, and helps extend the items' lifespan if maintained correctly.
Why is MRO important?
MRO includes everything the maintenance team does to keep the facility in proper working condition. MRO is necessary to ensure the smooth running of operations and to keep the production process running without failure without directly involving in the manufacturing process. This ensures that the equipment, systems and tools are properly stocked, maintained and in safe-to-use condition. Businesses consider MRO important because of its effect on costs, productivity and the safety of the facility to optimise the inventory levels, streamline procurement and improve the supply chain relationship and stay ahead of equipment failures. Without MRO, manufacturers cannot operate, as their daily activities can become interrupted without MRO.
What are the functions of MRO?
Most organisations usually rely on different kinds of machinery, technology system or equipment to run their facility. To maintain all these items in the proper working condition, it is required to have continuous maintenance efforts that keep the assets. MRO's main objective is to ensure that the departments always have the right kind of materials that are needed to be effective. By keeping all the crucial supplies in place, MRO helps accomplish the organisational goals, including reducing downtime, increasing safety, extending equipment lifecycle, minimising overstocks and protecting customer deliveries.
A strong MRO directly impacts the company's KPIs, ranging from equipment downtime, maintenance backlogs and overtime, asset performance and operational metrics. MRO also helps the organisation maintain customer satisfaction, maintain continuous production, follow lean practices and secure the right type of equipment every time. MRO also helps to reduce downtime, manage preventive maintenance and streamline the plants.
What is an example of an MRO?
MRO mainly includes a wide category of consumables, tools and spare parts in the supply chain materials. The most common MRO example includes industrial equipment like pumps, motors, electric saws, pliers, safety equipment, the consumables like janitorial or office supplies, and the maintenance supplies like lubrication liquids or repair tools.
Types of MRO
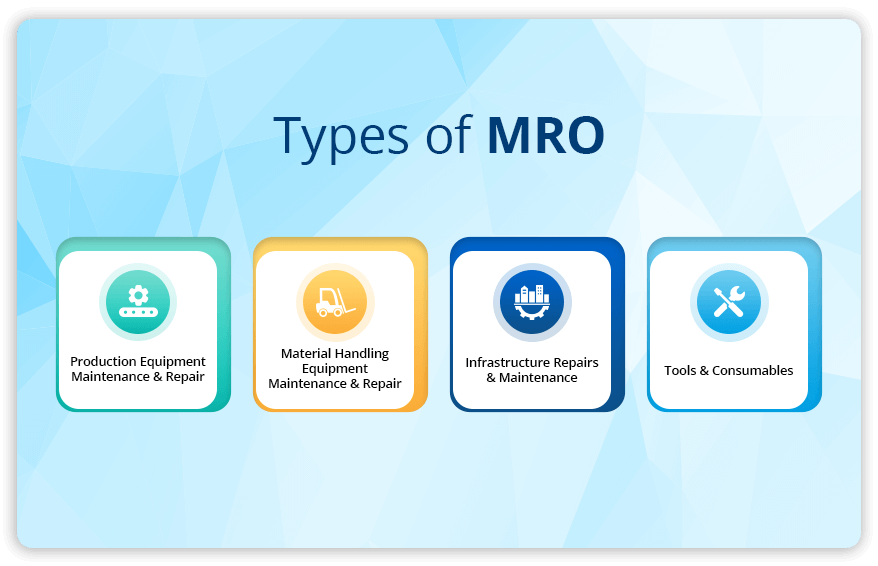
-
Production Equipment Maintenance and Repair:
To avoid disruption in the production process, the maintenance of the critical assets and systems is focused on this type of MRO, which mainly includes routine and emergency maintenance, purchase of condition monitoring equipment, replacement parts inventory management and supplier management. With time, machines wear and tear more and need more frequent upkeeps, with critical asset breakdowns or malfunctions affecting productivity. Switching to proactive maintenance strategies such as predictive and preventive maintenance helps the shopfloors stay on top of the maintenance and improve the asset uptime, availability and reliability. Usually, the preventive maintenance MRO keeps an eye on the spare parts stocks and orders that are likely to break. Also, the emergency maintenance of the production equipment falls under this category. -
Material Handling Equipment Maintenance and Repair:
Depending on the material needed to make a product, different types of machinery, such as forklifts, storage systems, bulk containers, conveyor systems, robotic arms and pallet positioners, are needed in the industry. These items are most important for moving the raw materials and components through the production lines and also help to transport the finished products to loading bays, where the workers ship them to the customers. This material handling equipment remains operable to avoid idle time. Although they do not directly involve in the production process, they still play a vital role in the overall production process. Therefore, including these types of MRO operations are necessary. -
Infrastructure Repairs and Maintenance:
The facility itself is essential, and businesses failing to prioritise the upkeep of the facility infrastructure pose a serious threat to the business. Serious flaws, faults or malfunctions in the industry floor can negatively affect productivity like any other faulty equipment. This type of maintenance includes cleaning services, HVAC systems servicing, pest control, lighting, grounds maintenance and building maintenance. -
Tools and Consumables:
This category of MRO is broad because it includes many minor pieces of equipment depending on the company's business, from the hand tools and the other items required to execute the maintenance and repairs. MRO tools and consumables include small power tools such as electric saws, hand tools such as pliers, PPEs, lubrication liquids, adhesives, welding rods, sandpapers and office supplies. These small items have the chance to get lost in larger facilities, and hence utmost care should be taken for this MRO during the maintenance planning.
What are MRO materials or MRO inventory?
MRO materials or MRO inventory usually belong to the indirect spending of organisational purchases where items are not directly used in production. The maintenance department uses MRO items to maintain their company structures, equipment and assets in proper working condition and ensure the smooth running of the business. MRO inventory includes supplies, spare parts and other materials needed for routine maintenance, repair or overhaul. Purchases usually under the MRO items include maintenance tools and equipment, replacement parts for production equipment, personal protective equipment and office supplies. However, this inventory does not become a part of the finished goods offered to the customers.
Which industry uses MRO?
MRO forms an inevitable part of various industries.
-
Manufacturing:
For any manufacturing industry, be it automotive, aerospace, electronics or consumer goods, MRO activities are highly important to maintain and repair the production equipment, machinery and tools. -
Transportation:
The transportation industry, whether airlines, railways or shipping and logistics, depends on MRO practices to maintain its fleet of vehicles, aircraft, locomotives and shipping containers. Regular inspections, repairs and replacement of the components ensure safety and improve the efficiency. -
Energy industry:
Power plants, oil refineries, gas pipelines and other energy utilities sectors need MRO services to ensure the reliable operation of the infrastructure, including the turbines, generators, transformers, pumps or valves. -
Healthcare:
MRO in the healthcare facilities involved in maintaining and repairing medical equipment such as MRI machines, X-Ray equipment, surgical instruments or patient monitoring systems. -
Food and Beverage:
For the Food and beverage industry to maintain the production lines, packaging machinery, refrigeration systems and processing equipment, ensuring compliance with quality and safety standards. -
Mining industry:
Mining operations rely on MRO practises to maintain their heavy machinery, drilling equipment, conveyor systems and processing plants, ensuring uninterrupted production.
How to manage your MRO with a CMMS?
Managing Maintenance, Repair, and Operations (MRO) using a Computerised Maintenance Management System (CMMS) can significantly enhance the efficiency and effectiveness of the maintenance management processes. Here are some critical steps and considerations for managing MRO with a CMMS:
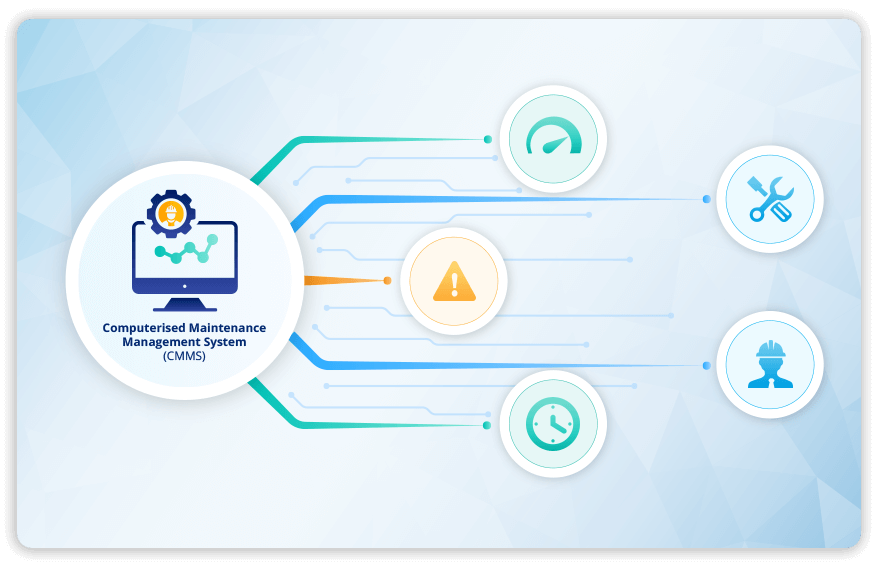
-
Define your MRO requirements:
Start by identifying the maintenance, repair, and operations activities relevant to your organisation, which may include routine preventive maintenance, reactive repairs, inventory management, work orders, asset tracking, and more. -
Select a suitable CMMS:
Research a CMMS that aligns with your specific MRO needs. Look for features such as work order management, asset management, inventory tracking, reporting capabilities, and integration options with other systems. -
Set up your CMMS:
Configure the CMMS to match your organisation's structure, assets, and workflows. In this step, the asset information is added, preventive maintenance schedules are created, user roles and permissions are defined, inventory items are set up, and notification/alert settings are established. -
Populate Asset data:
Enter relevant asset information into the CMMS, such as equipment specifications, maintenance history, warranty details, and vendor information. This will help track asset performance, identify recurring issues, and facilitate maintenance planning. -
Establish Preventive Maintenance Plans:
Utilise the CMMS to create and schedule preventive maintenance tasks based on manufacturer recommendations, industry best practices, or your organisation's specific requirements. Set up automated notifications for upcoming maintenance activities. -
Generate work orders:
When maintenance or repair tasks are needed, generate work orders within the CMMS. Include asset identification, problem description, required parts/tools, priority level, and assigned technicians here. -
Track and manage inventory:
Use the CMMS to monitor MRO inventory levels, track stock usage, reorder parts when necessary, and maintain accurate inventory records. Set up alerts for low stock or critical items to ensure timely replenishment. -
Execute work orders:
Assign work orders to appropriate technicians and track their progress within the CMMS. Update work order status, record labour hours, document completed tasks, and note any additional parts or services utilised. -
Capture maintenance data:
Regularly update the CMMS with maintenance data, including work performed, repairs made, parts replaced, and associated costs. This information serves as a valuable resource for analysing equipment performance, identifying trends, and making data-driven decisions. -
Analyse performance and generate reports:
Leverage the reporting and analytics capabilities of the CMMS to gain insights into MRO activities. Monitor Key Performance Indicators (KPIs) such as asset downtime, maintenance costs, work order completion rates, and Overall Equipment Effectiveness (OEE). Use this data to identify areas for improvement and optimise maintenance processes. -
Continuously improve:
Regularly review and refine your MRO processes based on the insights and analysis derived from the CMMS. To ensure ongoing improvement, incorporate technician feedback, monitor system utilisation, and stay updated on industry best practices.
By effectively utilising a CMMS for MRO management, you can streamline maintenance operations, increase asset reliability, optimise inventory levels, and make informed decisions to improve overall operational efficiency.
Types of MRO maintenance in a manufacturing industry
In the manufacturing industry, Maintenance, Repair, and Operations (MRO) can be categorised into several types based on their nature and purpose.
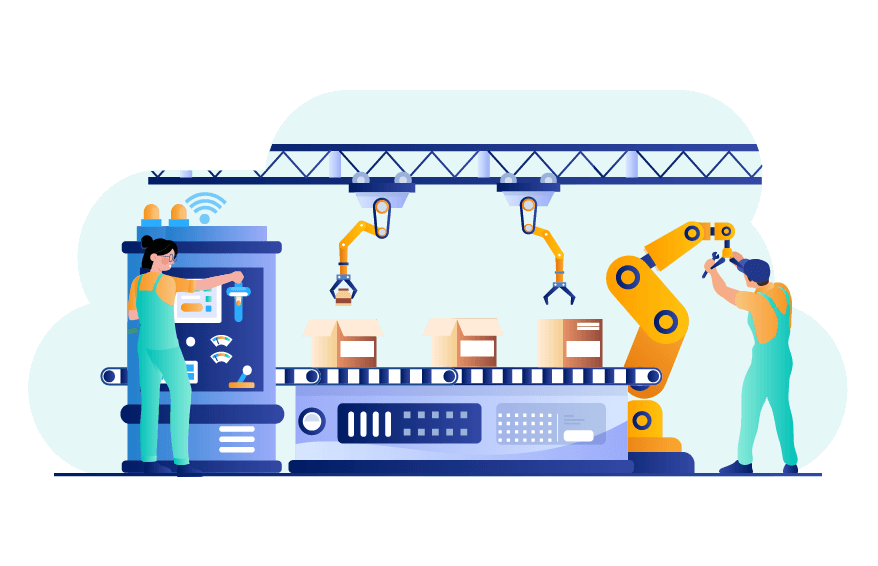
-
Preventive Maintenance (PM):
This type involves regularly scheduled inspections, servicing, and repairs to prevent equipment failure and ensure optimal performance. PM tasks include lubrication, cleaning, calibration, adjustments, and component replacements based on equipment manufacturer recommendations or industry best practices. -
Corrective Maintenance:
Corrective maintenance, also known as reactive or breakdown maintenance, is performed in response to unexpected equipment failures or malfunctions. It involves troubleshooting, diagnosing the problem, and repairing or replacing faulty components to restore the equipment's functionality. Corrective maintenance aims to minimise downtime and get the equipment back into operation quickly. -
Predictive Maintenance (PdM):
Predictive maintenance utilises advanced techniques and technologies, such as condition monitoring, sensors, and data analysis, to predict when equipment failures are likely to occur. By continuously monitoring equipment parameters, PdM aims to detect early signs of deterioration or impending failures, allowing maintenance activities to be scheduled before a breakdown happens. This approach helps to optimise maintenance resources and minimise unplanned downtime. -
Shutdown or Outage Maintenance:
This is performed during planned shutdown periods or scheduled equipment outages. It involves comprehensive inspections, repairs, overhauls, and upgrades that cannot be accomplished during regular production operations. Shutdown maintenance often includes major equipment inspections, replacement of critical components, system upgrades, and performance testing. -
Calibration and Testing:
Calibration maintenance involves verifying and adjusting equipment to ensure it meets specified accuracy and performance standards. This is particularly important for measuring devices and instruments used in manufacturing processes. Testing maintenance focuses on conducting various tests, such as load, pressure, or performance tests, to evaluate equipment performance, safety, and compliance with regulatory requirements. -
Spare Parts Management:
Effective management of spare parts is crucial for minimising equipment downtime. MRO maintenance in this context involves inventory management, stock replenishment, parts sourcing, cataloguing, and tracking. It ensures that the necessary spare parts are readily available when needed, reducing the time required to repair equipment. -
Safety Maintenance:
Safety maintenance activities aim to ensure a safe working environment for employees and compliance with safety regulations. This includes inspections and maintenance of safety equipment, emergency, ventilation, fire suppression, personal protective equipment (PPE), and safety signage.
These are the common examples of the types of MRO maintenance commonly found in the manufacturing industry. Organisations may also have specific maintenance categories based on their unique processes, equipment, and industry requirements.
Best Practices for an Effective MRO Strategy
Developing an effective Maintenance, Repair, and Operations (MRO) strategy is crucial for optimising equipment performance, minimising downtime, and reducing overall costs. Find the best practices to consider when formulating your MRO strategy here.
-
Asset Criticality Assessment:
Conduct an asset criticality assessment to determine the importance of each piece of equipment or asset to your operations. Assign a criticality rating based on factors such as impact on production, safety risks, and financial implications. This assessment helps prioritise maintenance efforts and allocate resources effectively. -
Data-Driven Decision Making:
Collect and analyse relevant data to drive decision-making. Utilise historical maintenance records, equipment performance data, failure patterns, and other relevant metrics to identify trends, predict failures, and optimise maintenance schedules. Implement a Computerised Maintenance Management System (CMMS) to facilitate data management and analysis. -
Preventive Maintenance Optimisation:
Develop a robust Preventive Maintenance (PM) program based on equipment manufacturer recommendations, industry best practices, and historical data. Regularly review and update PM tasks to ensure they align with equipment needs and optimise maintenance intervals. This approach helps prevent unexpected breakdowns, extend equipment lifespan, and reduce corrective maintenance needs. -
Reliability-Centred Maintenance (RCM):
Implement a reliability-centred maintenance approach, where maintenance activities are focused on addressing the root causes of failures and improving overall equipment reliability. RCM involves identifying failure modes, assessing their consequences, determining appropriate maintenance tasks, and optimising maintenance intervals to maximise reliability while minimising costs. -
Spare Parts Management:
Establish an efficient spare parts management system to ensure the availability of critical components when needed. Conduct regular inventory assessments, track consumption patterns, and implement reliable reordering processes. Consider centralising spare parts storage and implementing barcoding or RFID systems for accurate inventory management. -
Vendor Management:
Develop strong relationships with reliable suppliers and vendors to ensure timely delivery of quality parts and services. Negotiate favourable contracts, establish performance metrics, and conduct regular evaluations to ensure vendors meet your quality, delivery, and cost-effectiveness expectations. -
Training and Skill Development:
Invest in training and skill development programs for maintenance personnel. Ensure they have the necessary technical knowledge, skills, and certifications to perform their tasks effectively. Encourage continuous learning and stay updated on new technologies and maintenance practices through workshops, seminars, and industry conferences. -
Safety and Compliance:
Prioritise safety in all maintenance activities. Implement proper safety protocols, provide appropriate personal protective equipment (PPE), and ensure compliance with safety regulations. Conduct regular safety audits, promote a safety culture, and encourage employees to report safety concerns or near-miss incidents. -
Continuous Improvement:
Foster a culture of continuous improvement within the maintenance team. Encourage feedback and suggestions from technicians, conduct regular performance reviews, and implement a system for capturing and implementing improvement ideas. Continuously monitor Key Performance Indicators (KPIs) and benchmark against industry standards to identify areas for enhancement. -
Collaboration and Communication:
Foster collaboration and effective communication between maintenance personnel, operations teams, and other stakeholders. Establish clear lines of communication, encourage knowledge sharing, and facilitate cross-functional cooperation to improve equipment reliability and overall operational efficiency.
By incorporating these best practices into your MRO strategy, you can enhance the effectiveness and efficiency of your maintenance operations, reduce downtime, and achieve better overall equipment performance.
How Does MRO Affect Supply Chain Management and Inventory Management?
Maintenance, Repair, and Operations (MRO) activities significantly impact supply chain and inventory management. MRO requires strong supplier relationships, efficient lead time management, and supply chain resilience to ensure timely spare parts and resource availability. Effective inventory management for MRO involves maintaining an adequate inventory of spare parts, minimising stockouts and downtime, optimising costs, and implementing accurate tracking systems. Proper management of MRO activities in conjunction with supply chain and inventory management enables organisations to optimise maintenance operations, reduce downtime, control costs, and enhance overall operational efficiency. Close coordination between maintenance, procurement, and inventory management teams is crucial for achieving these goals.
What are the benefits of actively managing the MRO?
Actively managing Maintenance, Repair, and Operations (MRO) activities offer several benefits to organisations.
-
Increased Equipment Reliability:
Active MRO management proactively helps identify and address equipment issues. By implementing preventive maintenance programs, regularly inspecting and servicing equipment, and promptly addressing repairs, organisations can improve equipment reliability, reduce breakdowns, and minimise unplanned downtime. -
Enhanced Operational Efficiency:
Effective MRO management optimises maintenance processes, streamlines workflows, and reduces the time required for repairs. This leads to improved operational efficiency, increased production uptime, and smoother workflow continuity. -
Cost Reduction:
Active MRO management can result in cost savings for organisations. By implementing preventive maintenance, organisations can prevent costly breakdowns and extend the lifespan of equipment. Additionally, proper inventory management ensures the availability of critical spare parts while minimising inventory holding costs and reducing the need for emergency procurement at higher prices. -
Improved Safety and Compliance:
Regular maintenance and repair activities contribute to a safer work environment by ensuring that equipment operates optimally. Active MRO management helps organisations comply with safety regulations and industry standards, reducing the risk of accidents and regulatory penalties. -
Optimal Resource Allocation:
Organisations can allocate maintenance resources effectively by actively managing MRO activities. This includes assigning skilled technicians, optimising labour hours, and efficiently scheduling maintenance tasks. Proper resource allocation improves productivity, reduces idle time, and maximises the utilisation of maintenance personnel. -
Data-Driven Decision Making:
Active MRO management involves collecting and analysing maintenance data, which provides valuable insights into equipment performance, failure patterns, and maintenance costs. By leveraging this data, organisations can make informed decisions regarding maintenance strategies, asset replacement, spare parts management, and process improvements. -
Extended Asset Lifespan:
Proactive maintenance practices, including preventive maintenance and timely repairs, can extend the lifespan of equipment and assets. Organisations can maximise the return on investment by keeping equipment in optimal condition, delaying capital expenditures for replacements, and improving asset longevity. -
Improved Customer Satisfaction:
Effective MRO management improves product quality, reduces production disruptions, and delivers reliable service. This enhances customer satisfaction, loyalty, and a positive brand image.
Overall, actively managing Maintenance, Repair, and Operations brings numerous benefits to organisations, including increased equipment reliability, enhanced operational efficiency, cost reduction, improved safety, optimal resource allocation, data-driven decision-making, extended asset lifespan, and improved customer satisfaction.